Completed
Make things from Ocean Plastic?
Me (Paul) and Nate are going to work in the Precious Plastic & Parley shipping container in the Maldives til May. While we’re here one of our focuses is learning about ocean plastic, particularly how the extended exposure to saltwater/UV/contamination affects its recyclability with the PP machines. We’ll share our research belowMore Information
Collect material
Created about 4 years agoUpdated about 4 years ago
One type in particular that stood out to me was plastic textile commonly used on boats in the form of rope and tarp.
The thing about these materials that I find interesting is that they’re so ubiquitous in coastal communities (at least the ones I’ve visited), but when I speak with people about them, they’re usually surprised to find out that they’re made of plastic.
One issue that’s particularly problematic when it comes to plastic textiles, especially in the ocean, is the fact that they’re made up of such small fibers, which inevitably degrade and pollute the environment over time. Once they’ve degraded, they become much more challenging to manage.
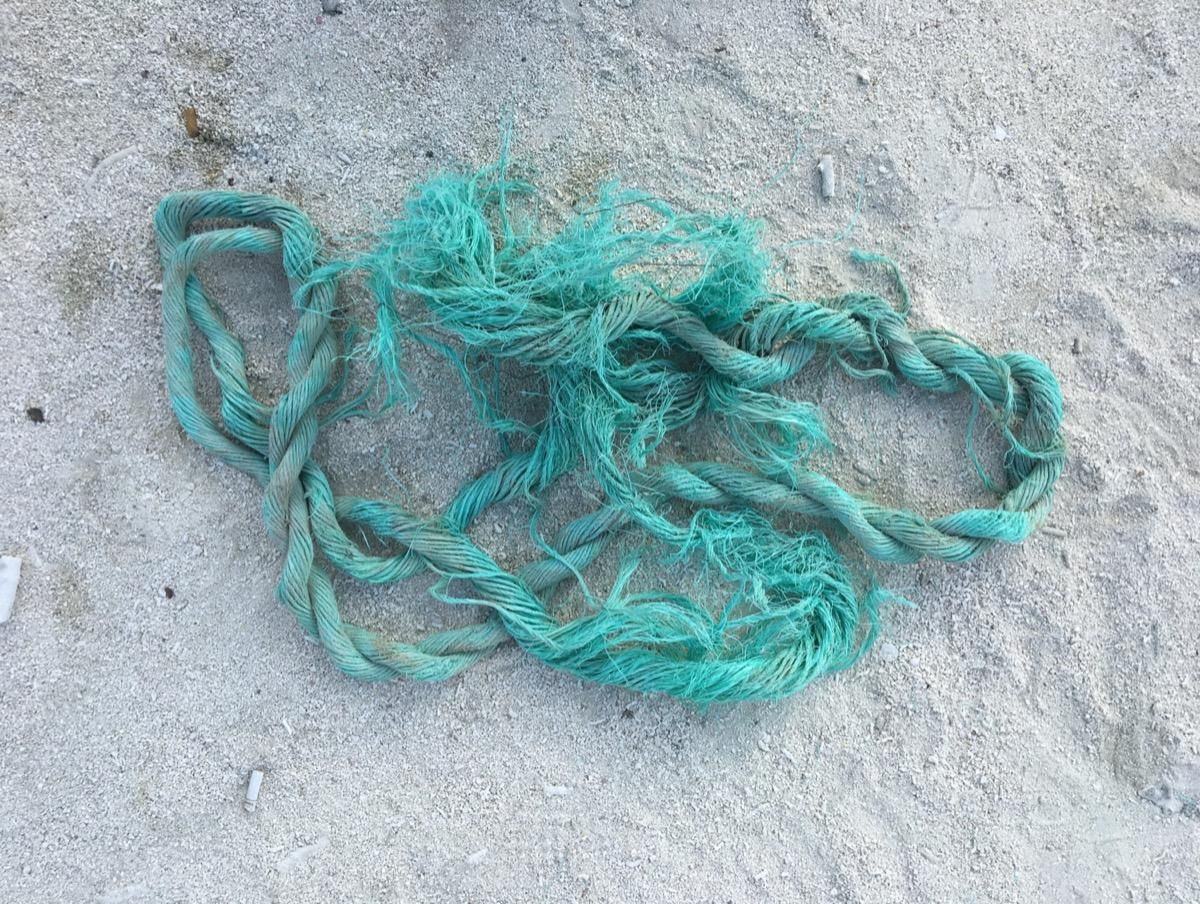
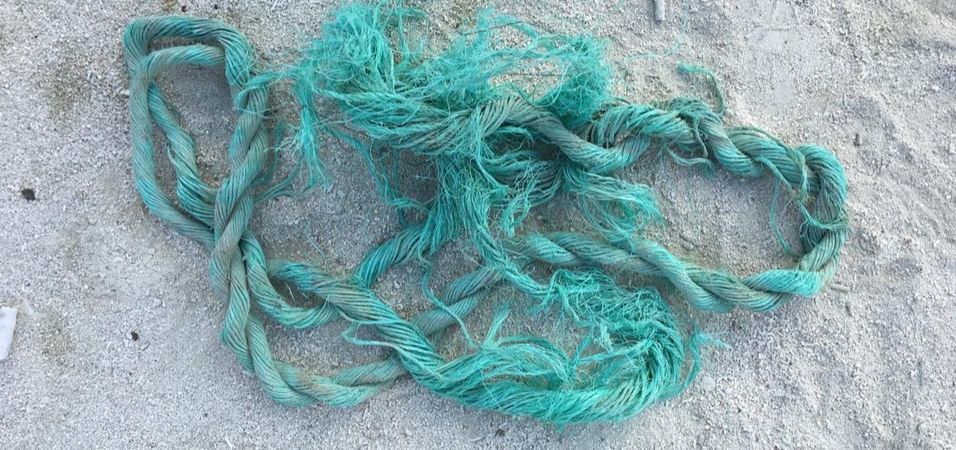
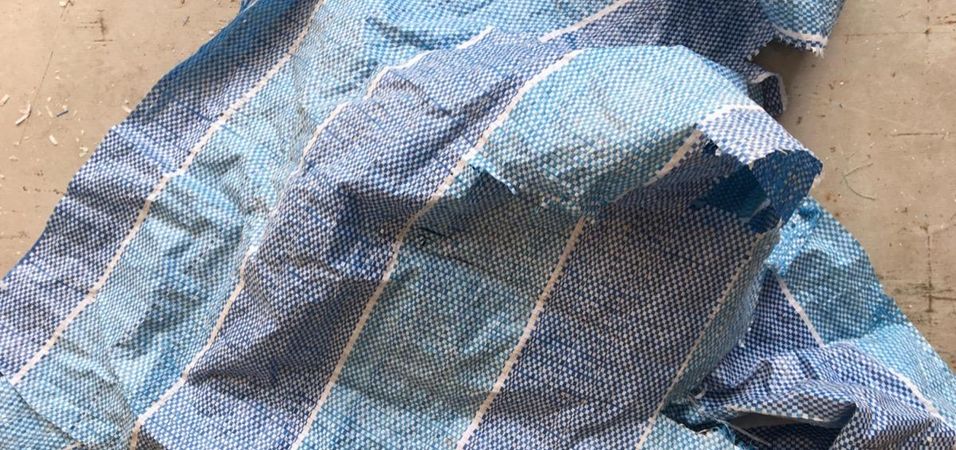
Sorting the waste
Created about 4 years ago
Then, I sorted through it to get a better understanding of the various categories that make up the sample.
In general, the items can be categorized as following:
–Conventional thermoplastics : oil bottles, etc. We have a pretty good understanding of how to recycle these. The main question is: how does degradation due to sun and sea exposure affect their properties? How do contaminants affect their recyclability?
-Marine textiles : rope, tarp, netting. These materials are often made from thermoplastics such nylon and PP, so in theory we should be able to recycle them.
-Conventional thermosets : rubber, etc. These don’t melt so we can’t recycle these using the same methods we use for thermoplastics.
-Foams / Expanded plastics : These can sometimes be recycled, however it isn’t my expertise so I won’t focus on it for now.
-Foils : Grocery bags, chip bags, etc. Foil compositions vary widely, sometimes being recyclable, sometimes not. Depending on progress in other categories, I might experiment with these but they will not be my main focus.
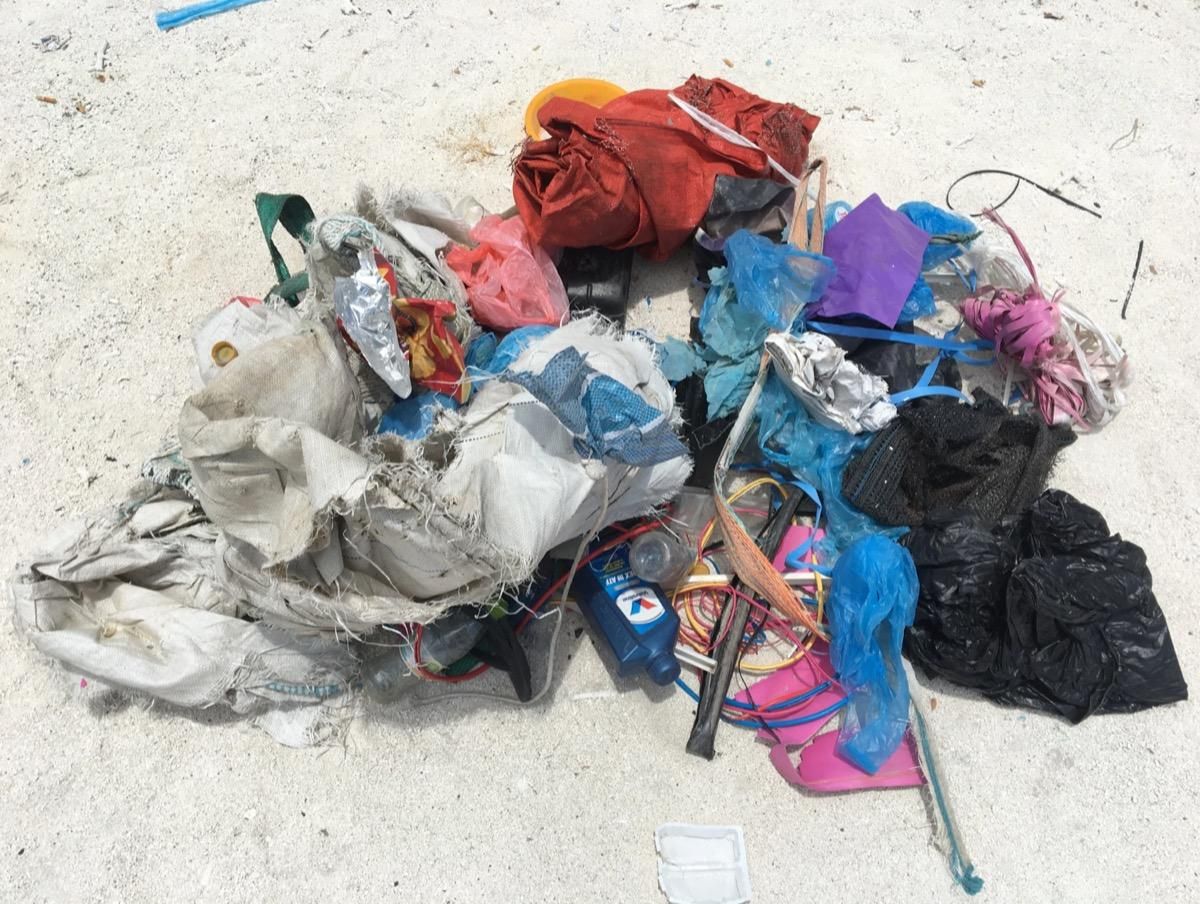
Sample #3 - Marine Textiles
Created about 4 years agoUpdated about 4 years ago
Of the plastics I collected, the category that caught my attention most was marine textiles – for a few reasons.
-Ubiquity : They’re used in huge quantities by shipping vessels all over the world for many different purposes – rope, storage bags, fish net, sunshade.
-Degradation : Because they’re made up of small fibers, they fray and degrade very easily into micro-plastics which are released into the environment.
-Useless : Once they start to break down, they’re rendered “useless” in their current form and often discarded once they reach this point. If we can recycle them, we could help prevent this form of pollution from happening as much.
-Knowledge : When speaking with people around the island about marine textiles, they’re usually surprised to find out that they’re made of plastic. Showing that they’re recyclable could give people more knowledge about materials that are so ubiquitous in their community, and hopefully help them make more informed decisions about how to use it in the future.
Below are some examples of degrading marine textiles I found on a 100-meter stretch of beach.
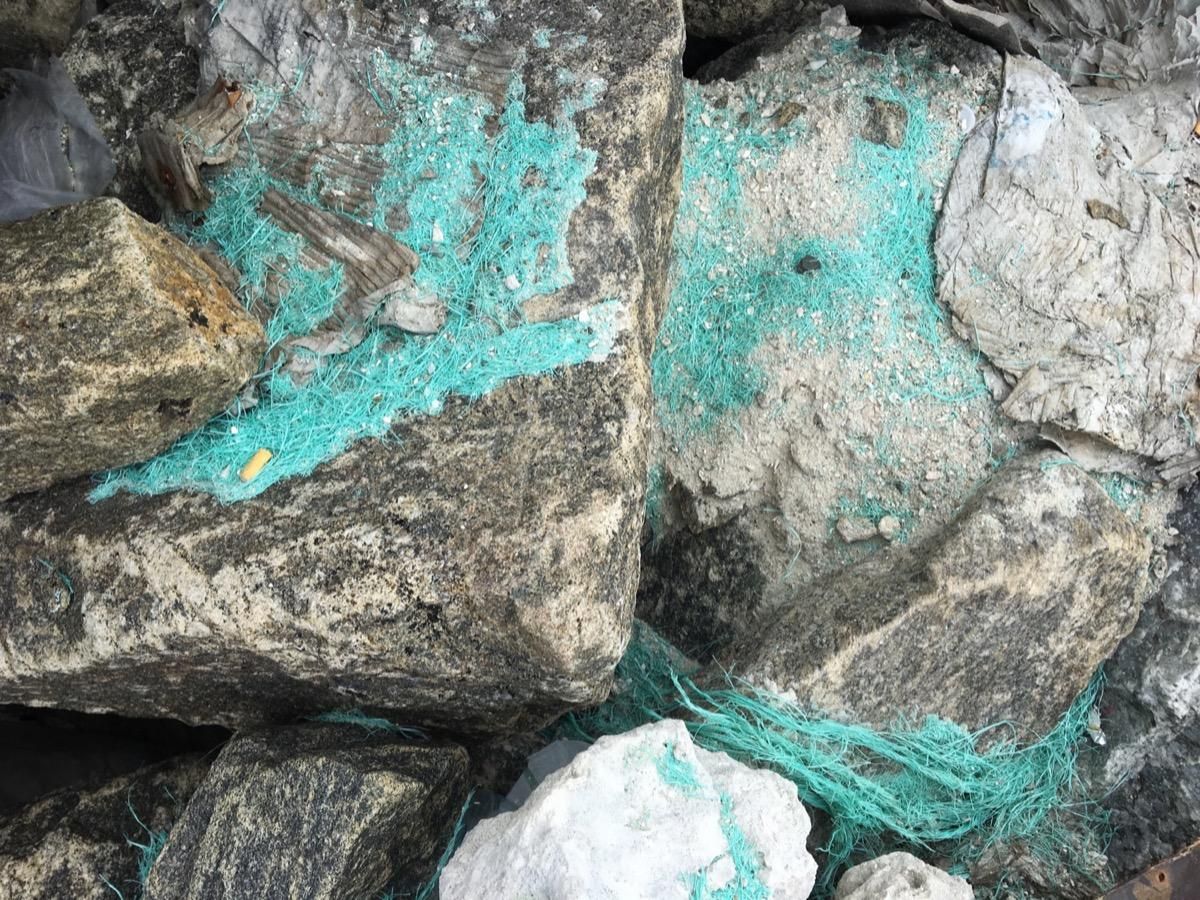
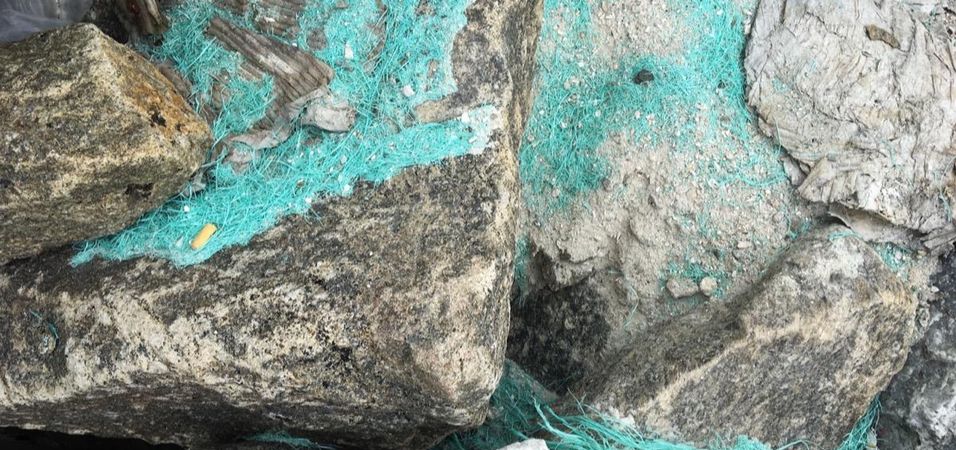
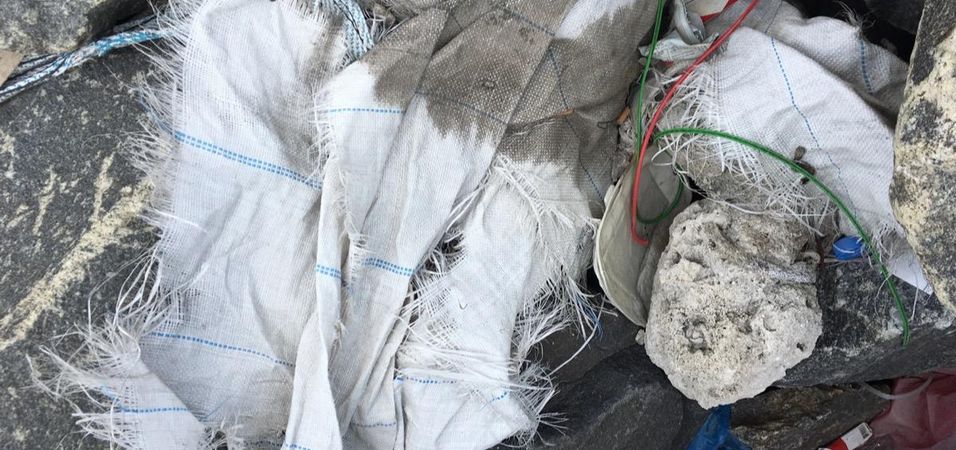
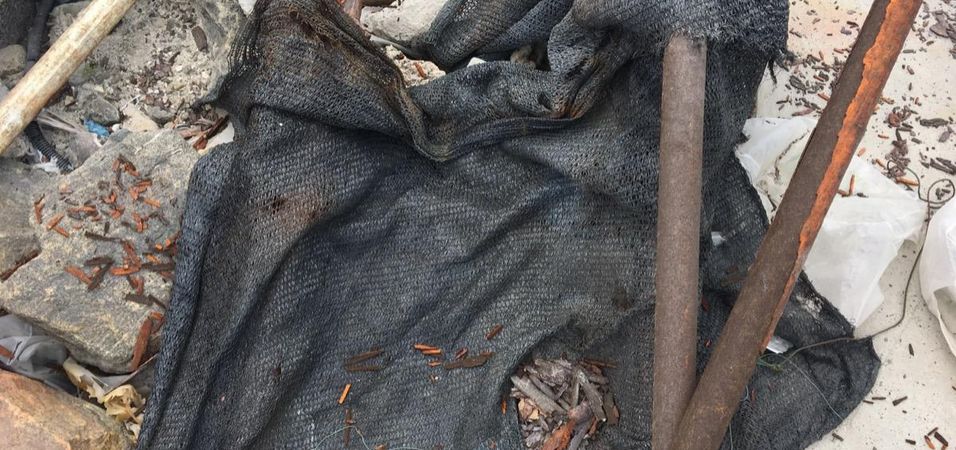
Experiment 01 – Marine Rope
Created about 4 years ago
To begin experiments, I collected some frayed marine rope and tested it in the injection machine to see if we could melt it down into a solid form which will be less prone to degradation over time.
For the time being, I’m just using a simple hex mold, but once proven that recycling these materials is possible, there are all sorts of directions we could take this.
Washing
Cleaning the rope was pretty easy. By dunking it in a water bath for a couple of minutes, most sand and other contaminants fell right off.
Injecting
Then I took the degraded parts of the rope that were no longer useful in their current form and loaded it into the injector.
The top band heaters were set to 210 and the nozzle at 220.
The material seems to flow really well without any problems.
Loading it into the injector was kind of a pain. Going to see if shredding beforehand helps. It seems like this material might be good in the extruder – and might work for your surf fins @hylasurf
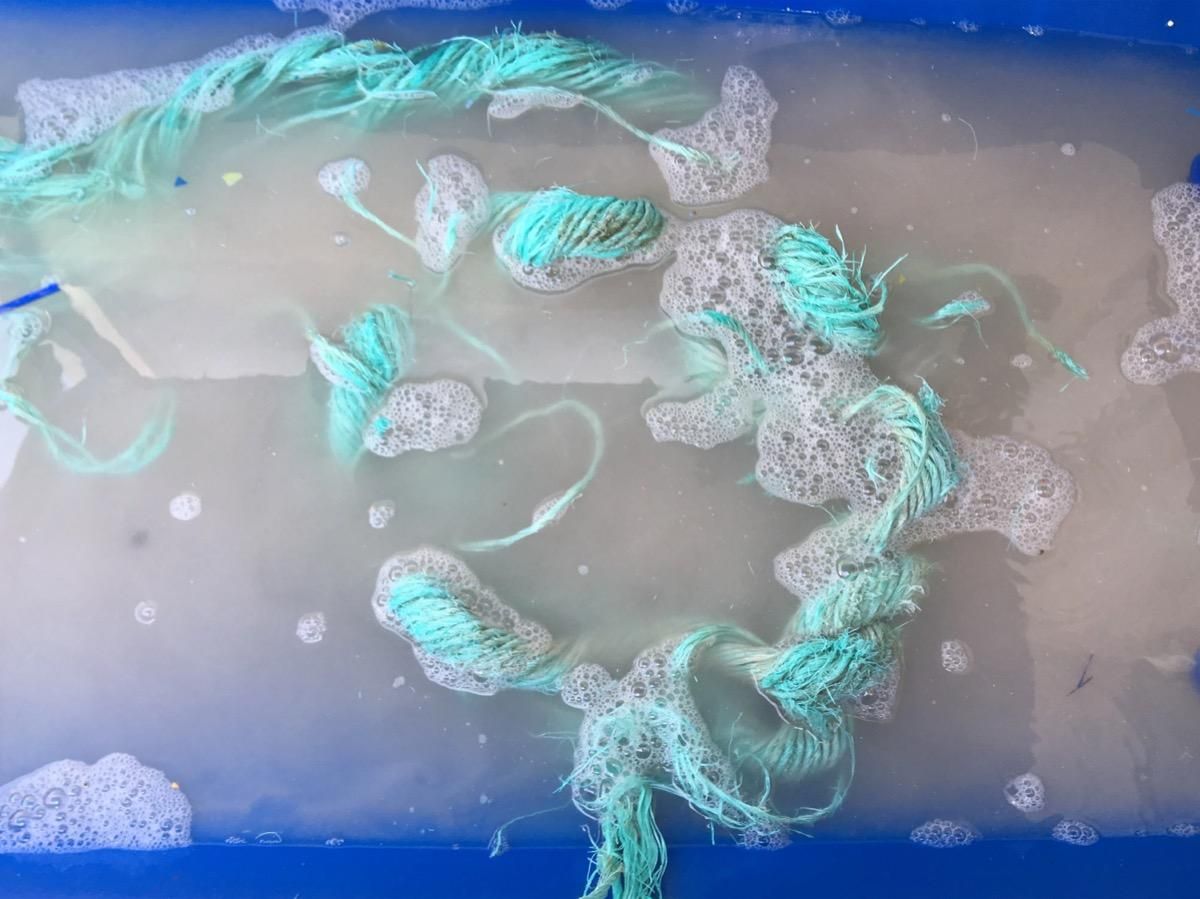
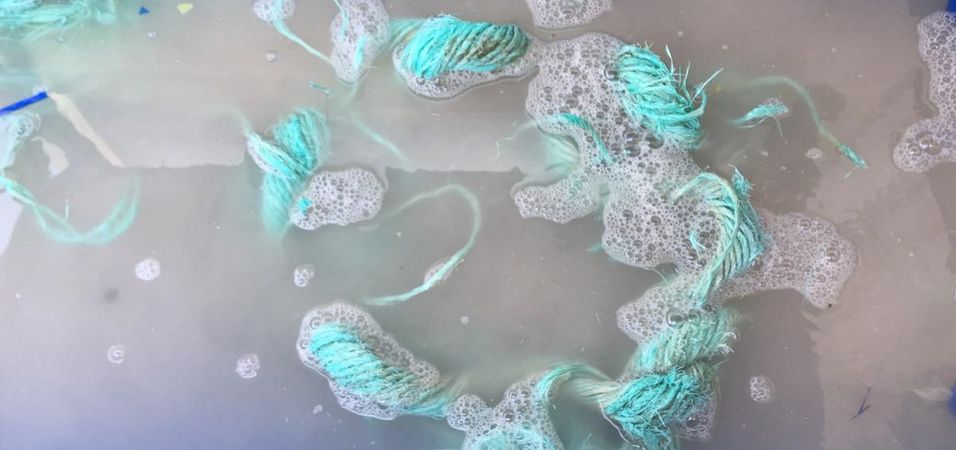
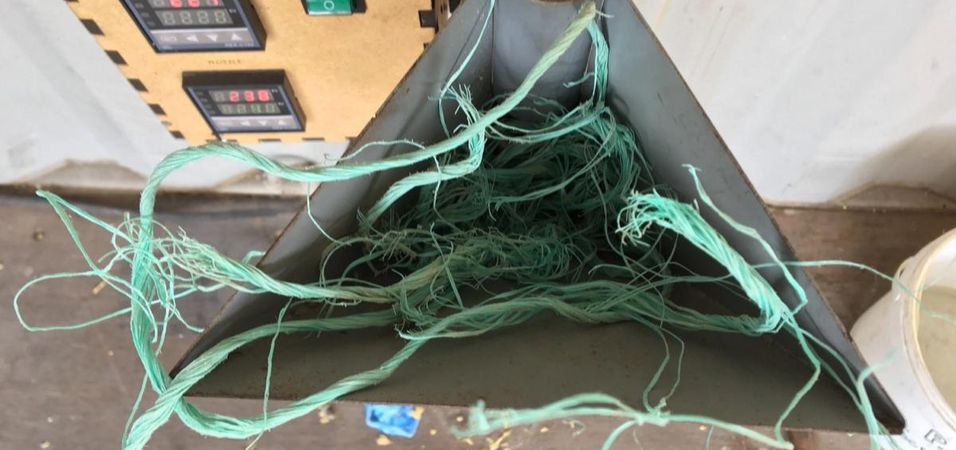
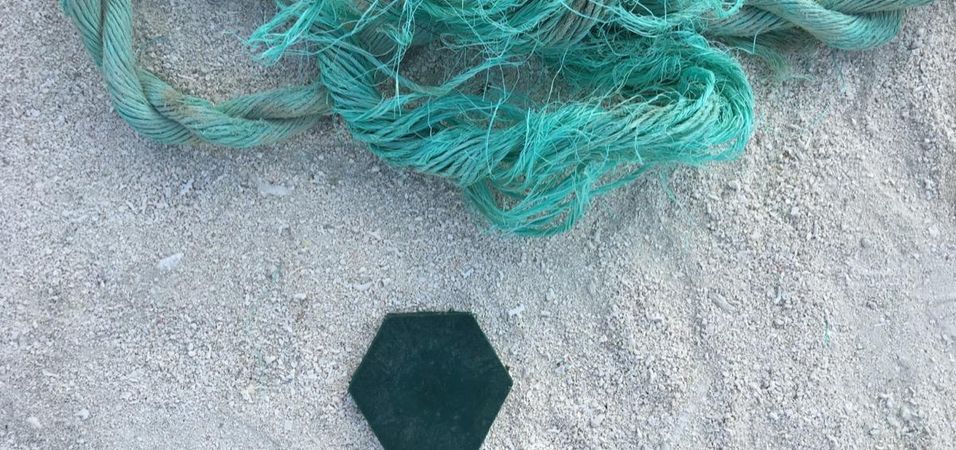
Experiment 02 – Tarp
Created about 4 years ago
I ran the same experiment with the plastic tarp I’ve been finding all over the place which also tends to break down.
I washed it the same way as the rope and then loaded it into the injector.
The heat needed to be increased to 240 and 250 to get the material to melt properly, and once molten, it began rising in the barrel towards the hopper – not sure what caused this.
Injecting worked pretty well, it didn’t seem to flow as smoothly as the rope. An increase in temperature might help this.
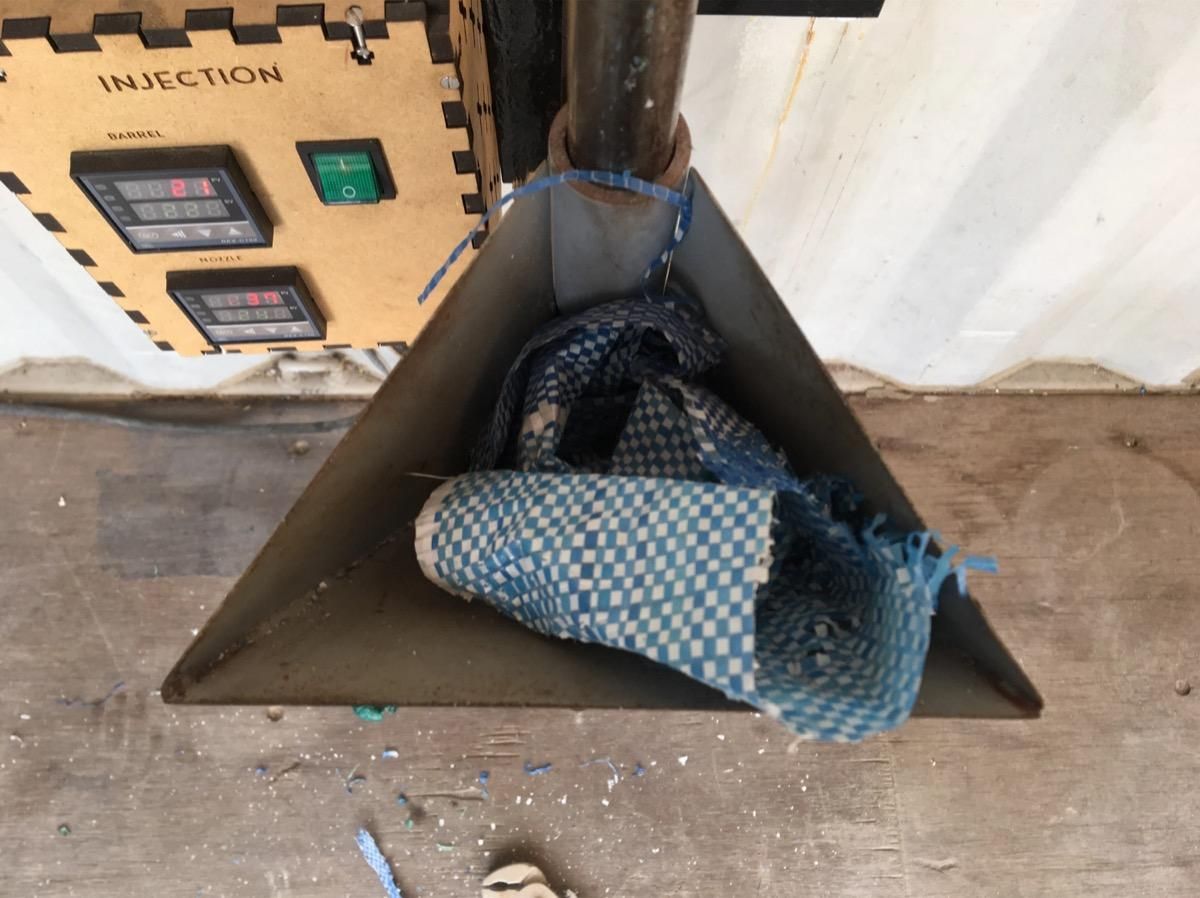
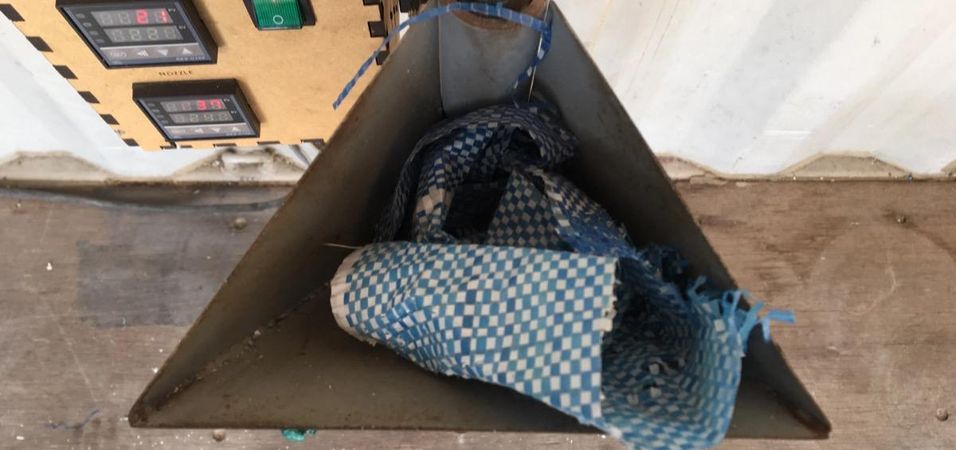
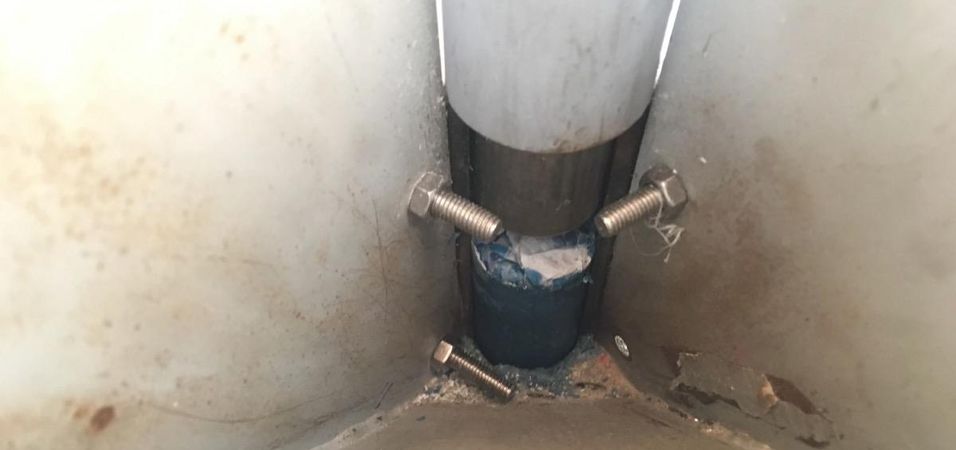
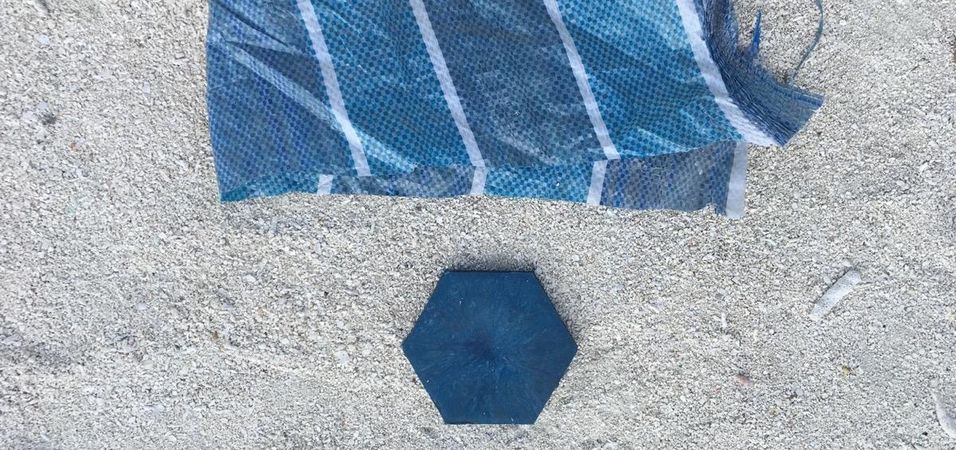
Experiment 03 – Sunshade
Created about 4 years ago
This material is used a lot on boats/beaches as a sunshade. Like the others, once it weakens, it’s often discarded and breaks down into micro plastics.
I washed this using the same method.
The temperature was raised to 240 and 250 to melt the material. Once molten, it flowed quite well and seems to be a pretty sturdy (as do the others).
Like the tarp, this material also began to rise in the barrel once heated – if anyone has any insight as to what’s causing that, it’d be greatly appreciated
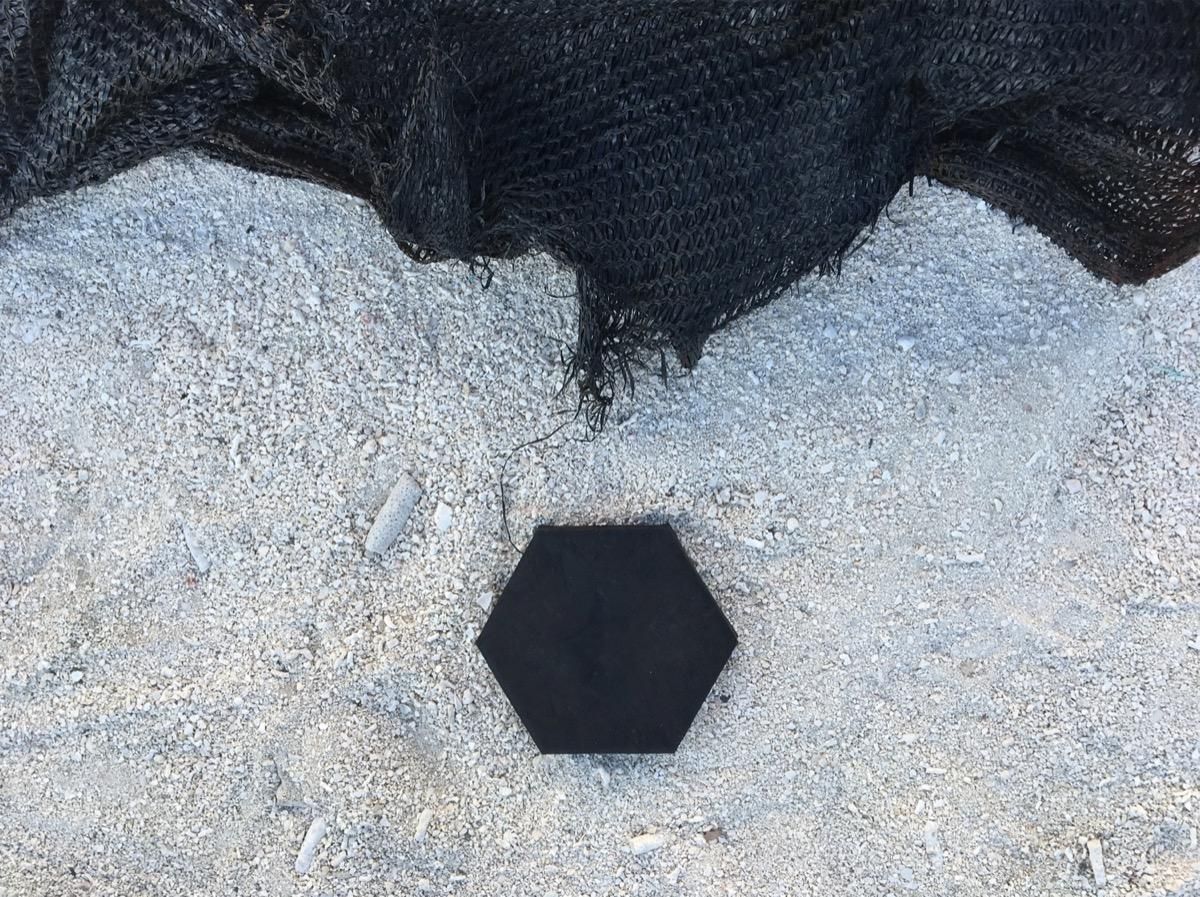
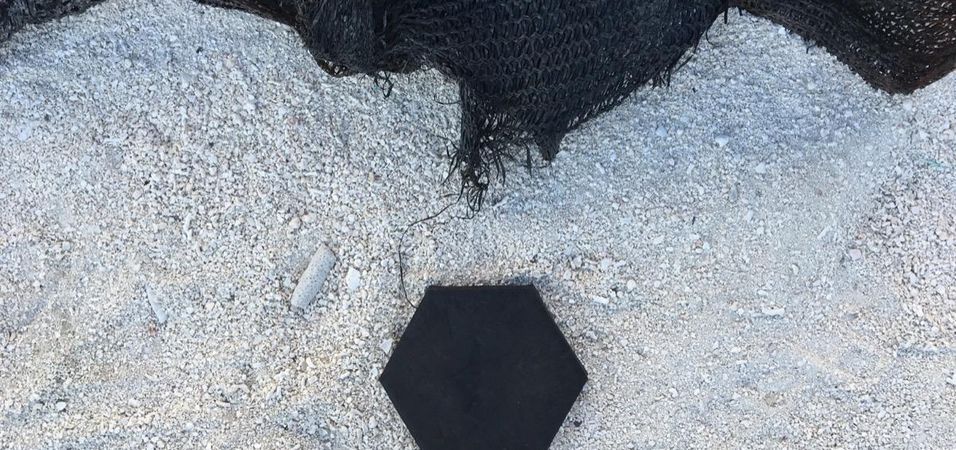
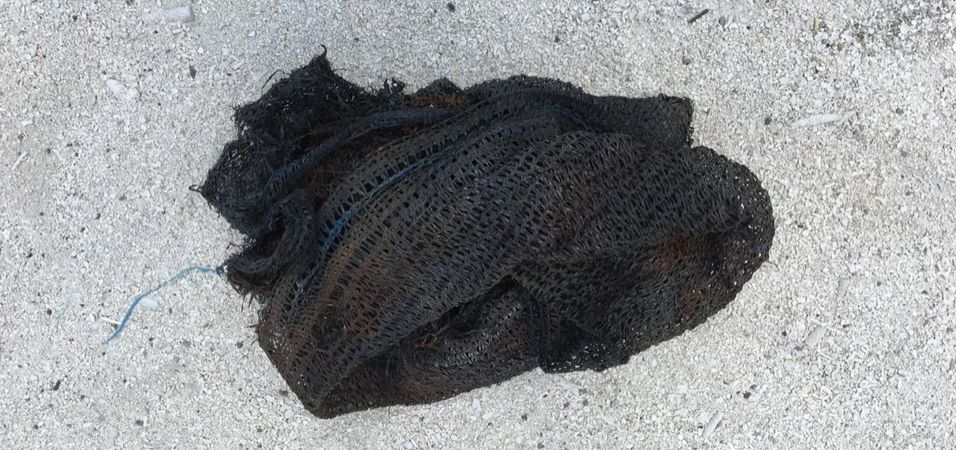
Experiment 04 – Transport bag
Created about 4 years ago
Another item that’s commonly found degrading are these transport bags.
I ran the same experiment as the others and found that this material can also be recycled using the injection machine.
These bags are made up of a few different components (bag, straps, threading) so I’m curious to see if they can all be recycled together or if they need to be separated.
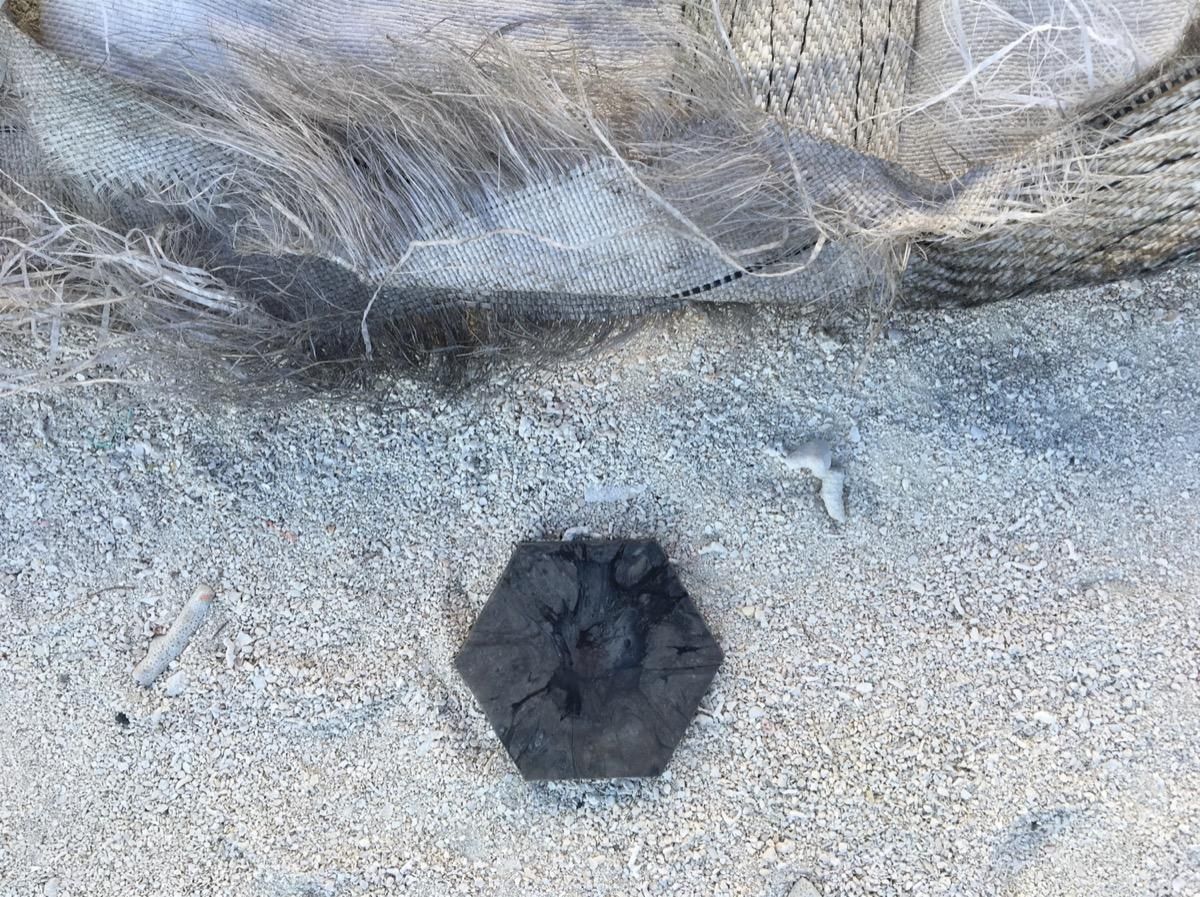
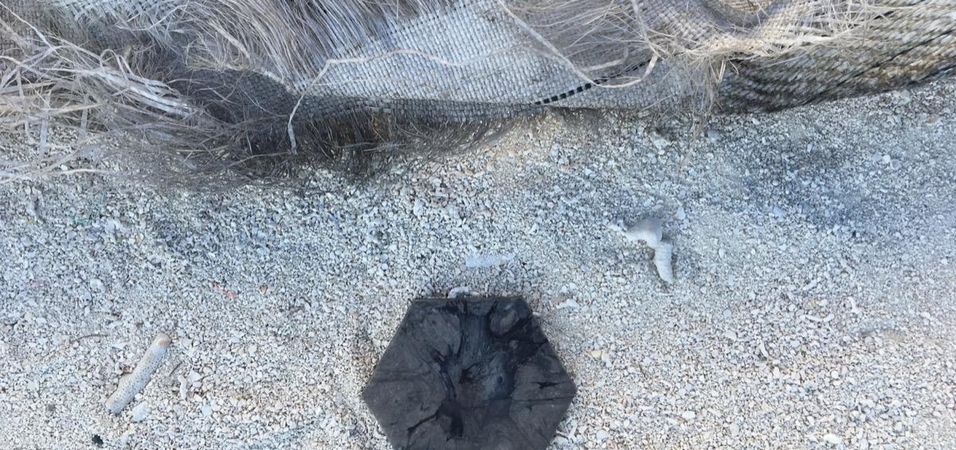
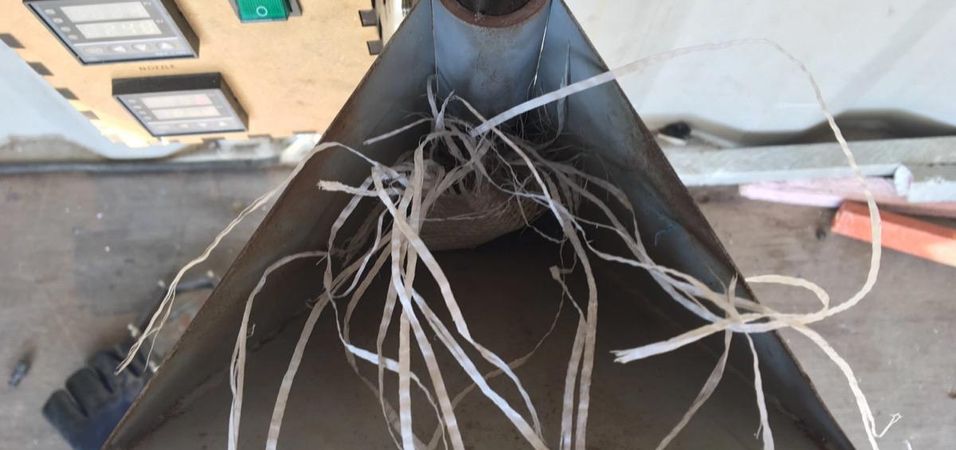
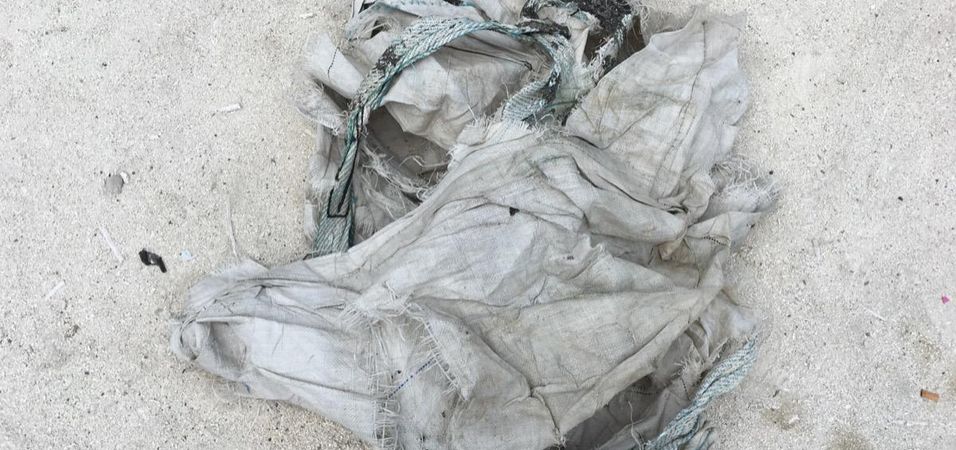
Experiment 05 – Extruding ocean rope
Created about 4 years ago
Seeing the success of the ocean rope with the injection machine, I wanted to see if we could manage to feed it into the extruder for easier processing.
First I experimented with cut, but unshredded rope. It worked, but it was hard to feed it into the machine at a consistent rate – sometimes the extrusion screw took the material without trouble, but other times it had to be coaxed by hand.
It did work though, so now it’s a matter of figuring out the best way to feed it into the machine.
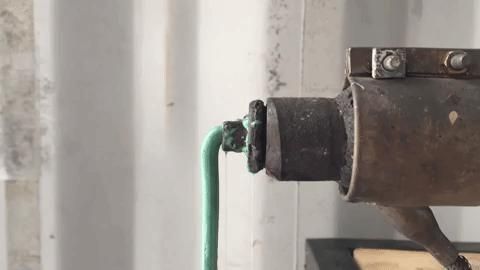
Experiment 05.1 – Shredding ocean rope
Created about 4 years ago
To see if it’d be easier to feed into the extruder, I shredded the rope before extruding.
Shredding the rope worked pretty well, but since the rope fibers are so thin, they began to heat up and clump together a bit as the machine warmed up.
Feeding the shredded rope into the extruder was better, but still not great. The material is very light, so when it’s clumped together it sometimes sits above the screw gaps instead of falling in, meaning it still needed to sometimes be coaxed in by hand.
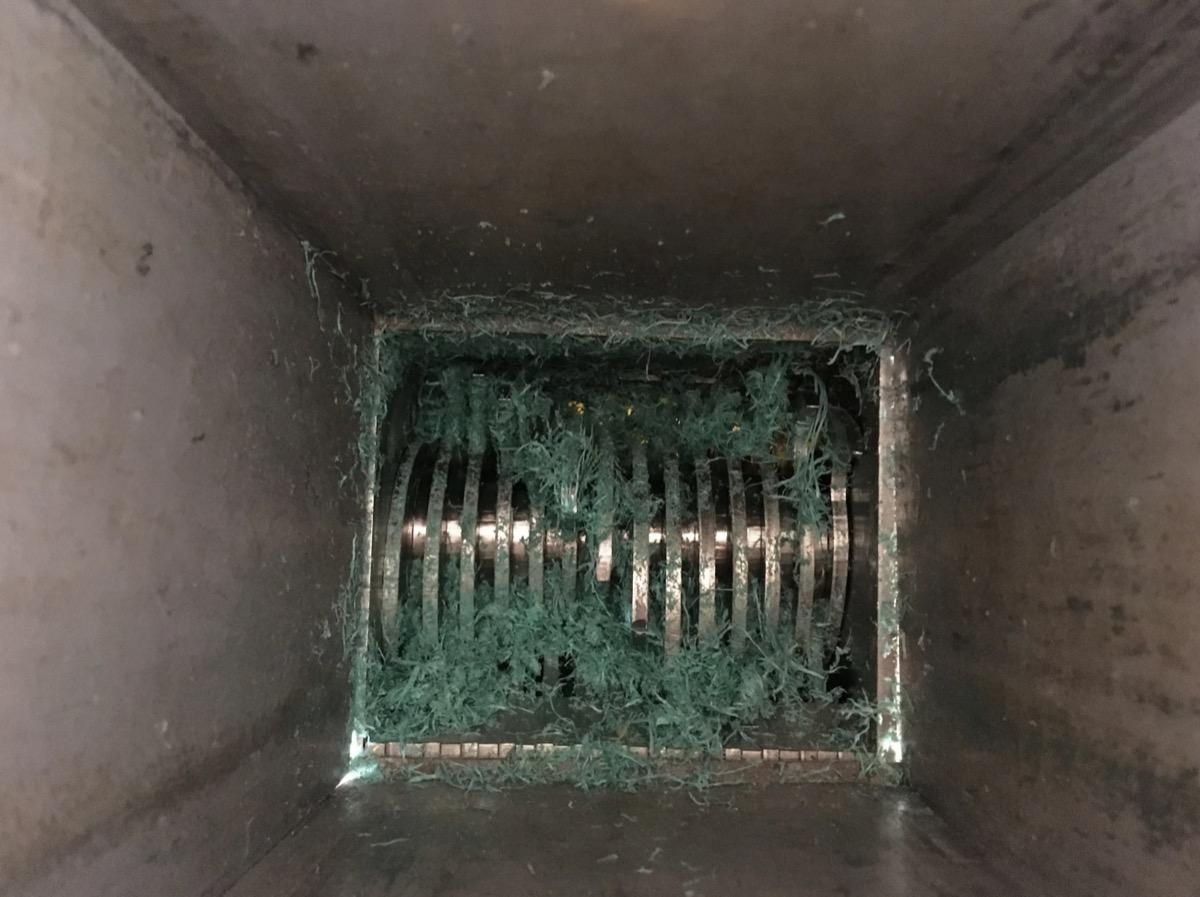
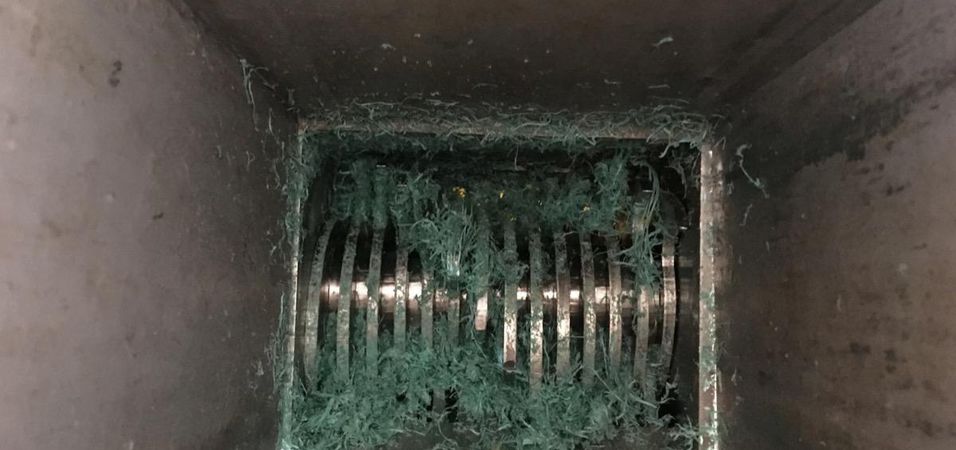
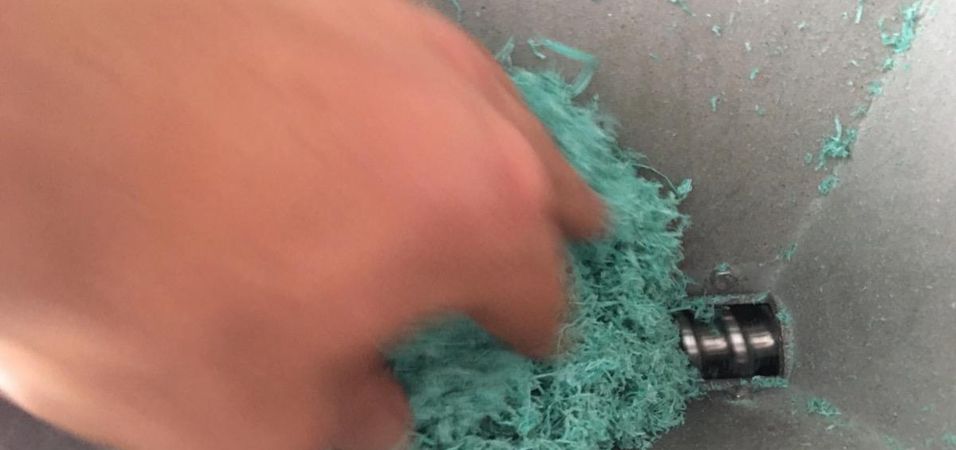
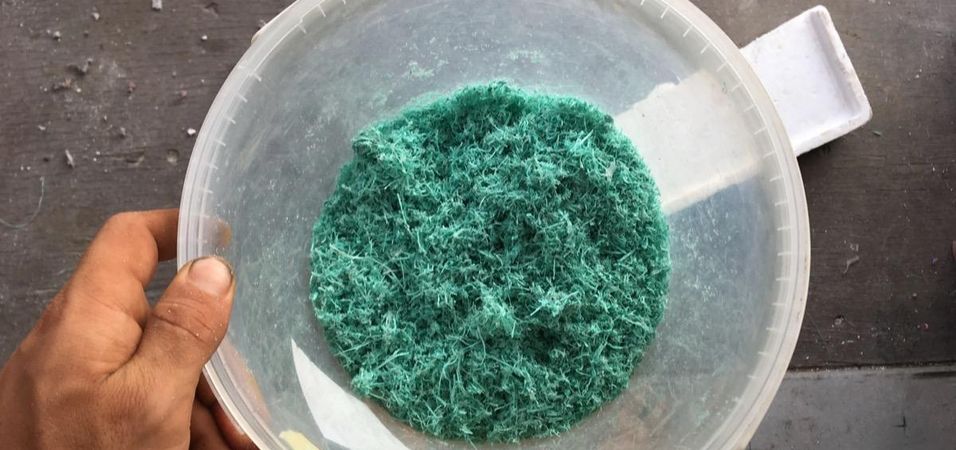
Experiment 05.2 – Swapping the extrusion
Created about 4 years ago
The spacing in the extrusion screw is considerably smaller than that of the old auger we used previously, so I decided to reinstall the auger to see if the larger spacing would make it easier for the rope to load into the machine.
Our shredder broke down (extra strong motor sheared shaft, not during rope shredding) so I’ve only been able to experiment with hand-cut, unshredded rope so far. The results have been promising though – the larger gaps in the auger help considerably and I was able to make a second beam.
The screw was spinning at a low RPM in the beginning, so the beam didn’t fully form, but once I bumped it up to full speed it worked quite well.
I was curious about how big of a difference cleaning the rope actually made, so I used dirty rope for this experiment. As you can see, a simple clean with a quick rinse in a tub helps quite a bit with removing the sand, dirt, etc.
Once our shredder is working again, I’ll test the auger with shredded rope.
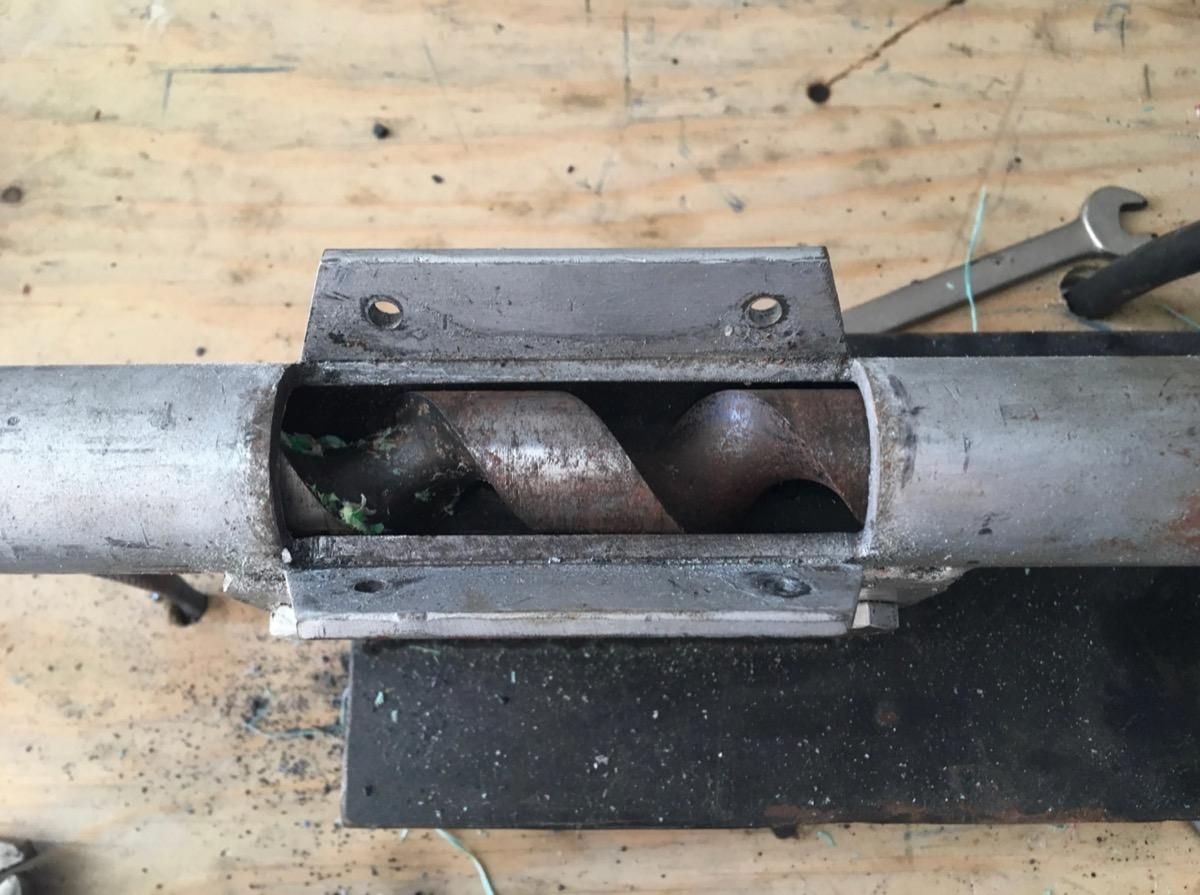
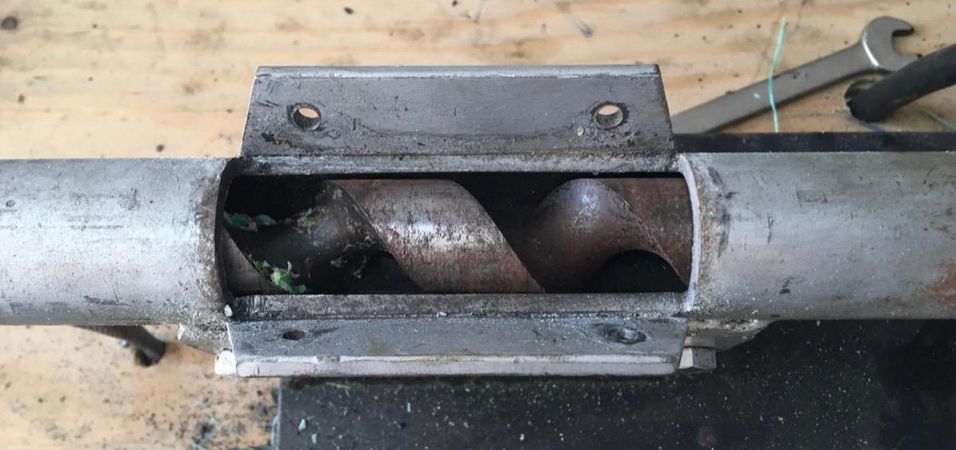
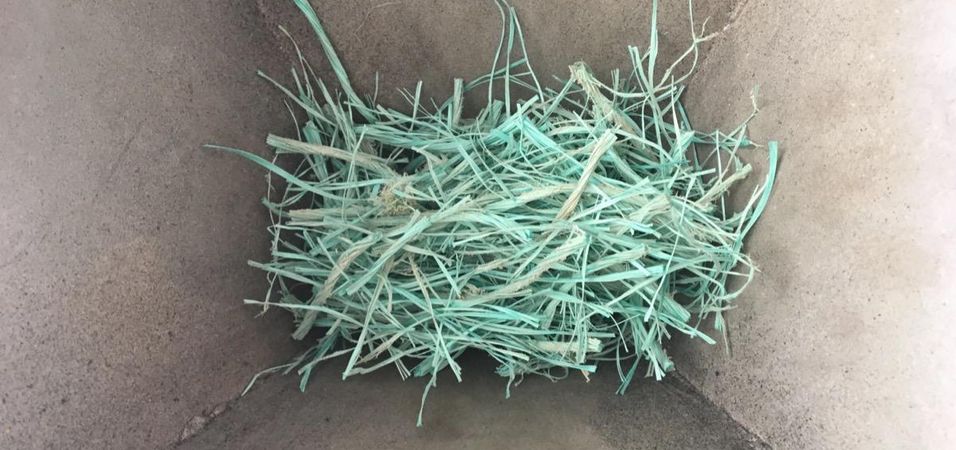
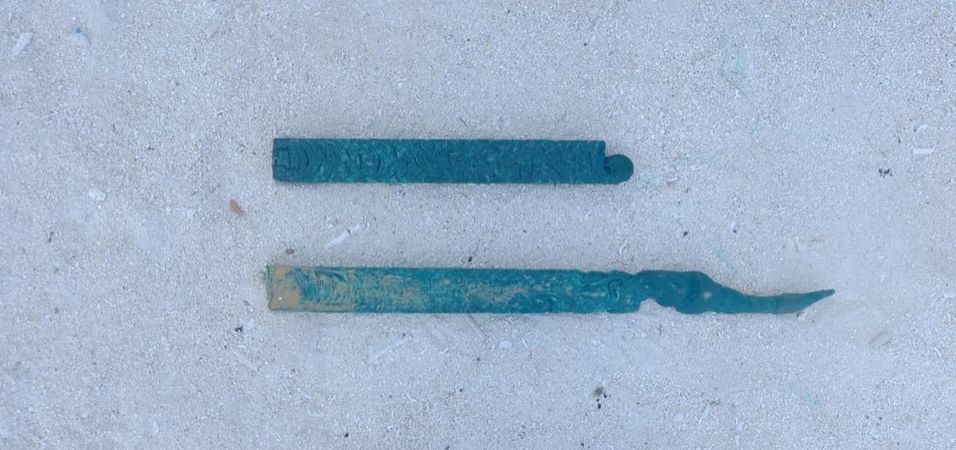
Shredded Rope
Created about 4 years ago
Shredding rope with the sieve installed works pretty well. A certain amount of rope builds up in the machine, but once it reaches a certain threshold, rope falls through the sieve rather than continually builds up. The only drawback is that some rope remains in the blades after shredding is finished, so you have to remove that by hand before shredding other types of plastic. It only takes a few minutes to do this so it’s not that bad.
Shredded rope feeds into the barrel more easily than long rope.
One issue with extruding the rope is that it’s much lighter than typical shredded plastic, so the screw pushes it forward in the hopper and then it builds up on the slope of the hopper instead of falling into the barrel. To prevent this, I prototyped a new hopper with vertical walls so that when the rope is pushed up against the wall, it tumbles backwards instead of building up.
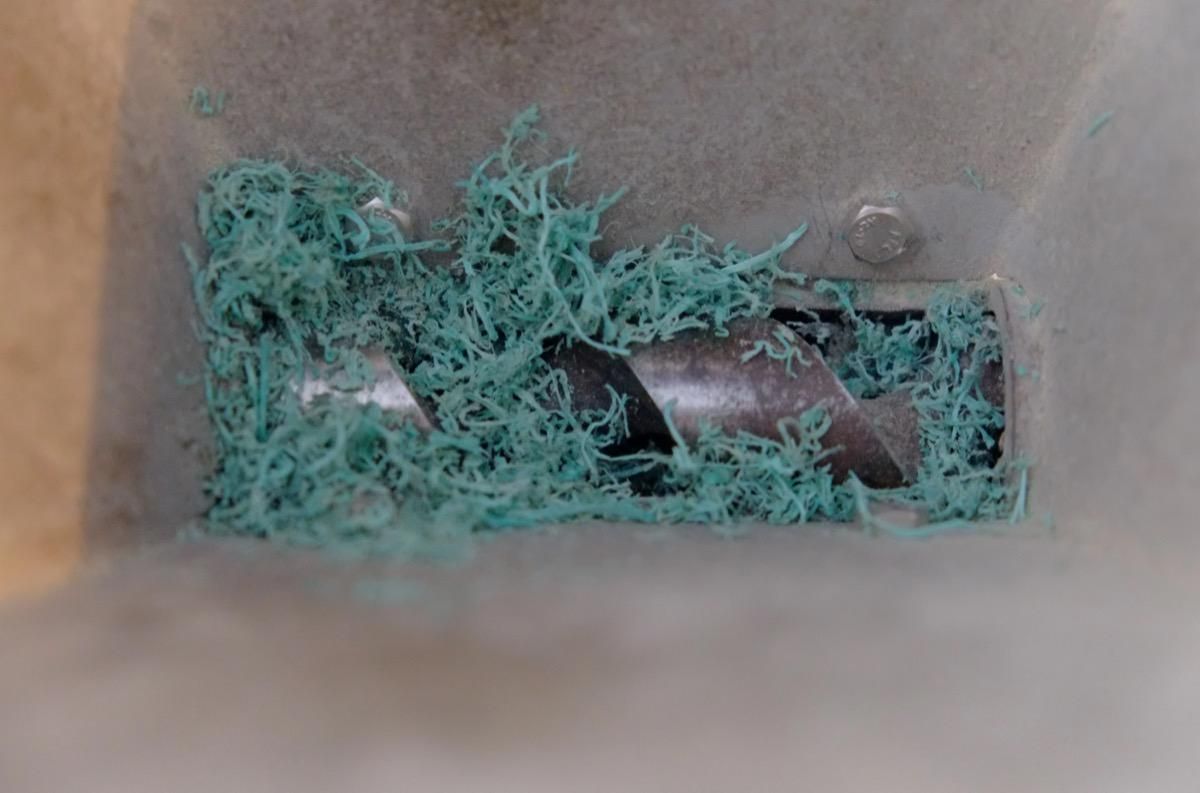
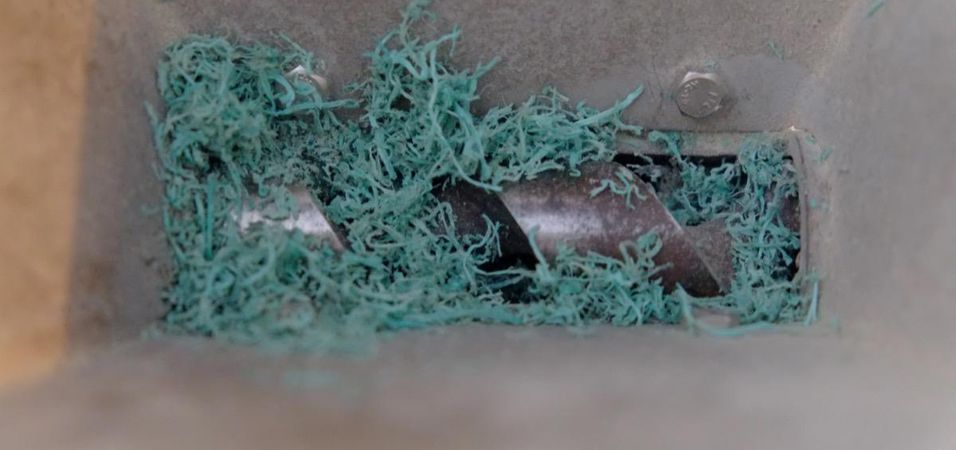
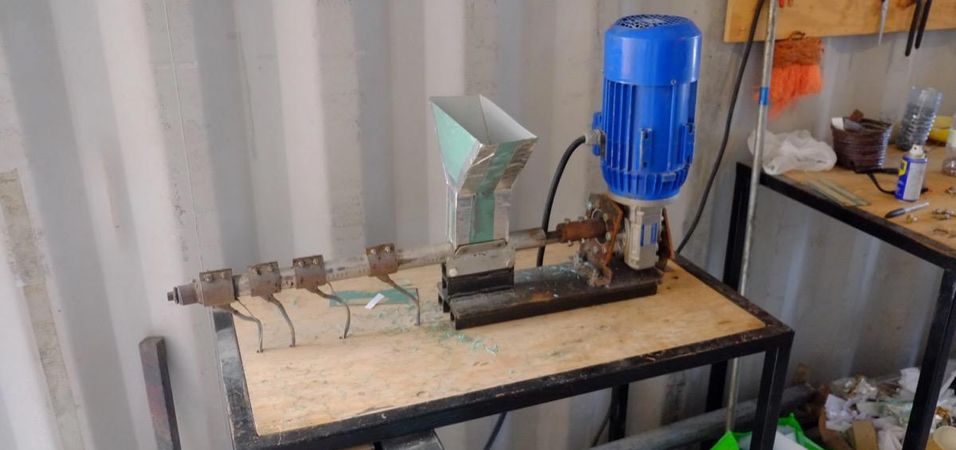
Real Life Testing
Created about 4 years ago
Before leaving I wanted to make something useful out of the recycled ocean rope to show that it can have practical applications.
We built this side table (and sometimes foot rest) to put next to the Jolly (sp?) chairs in the hangout space.
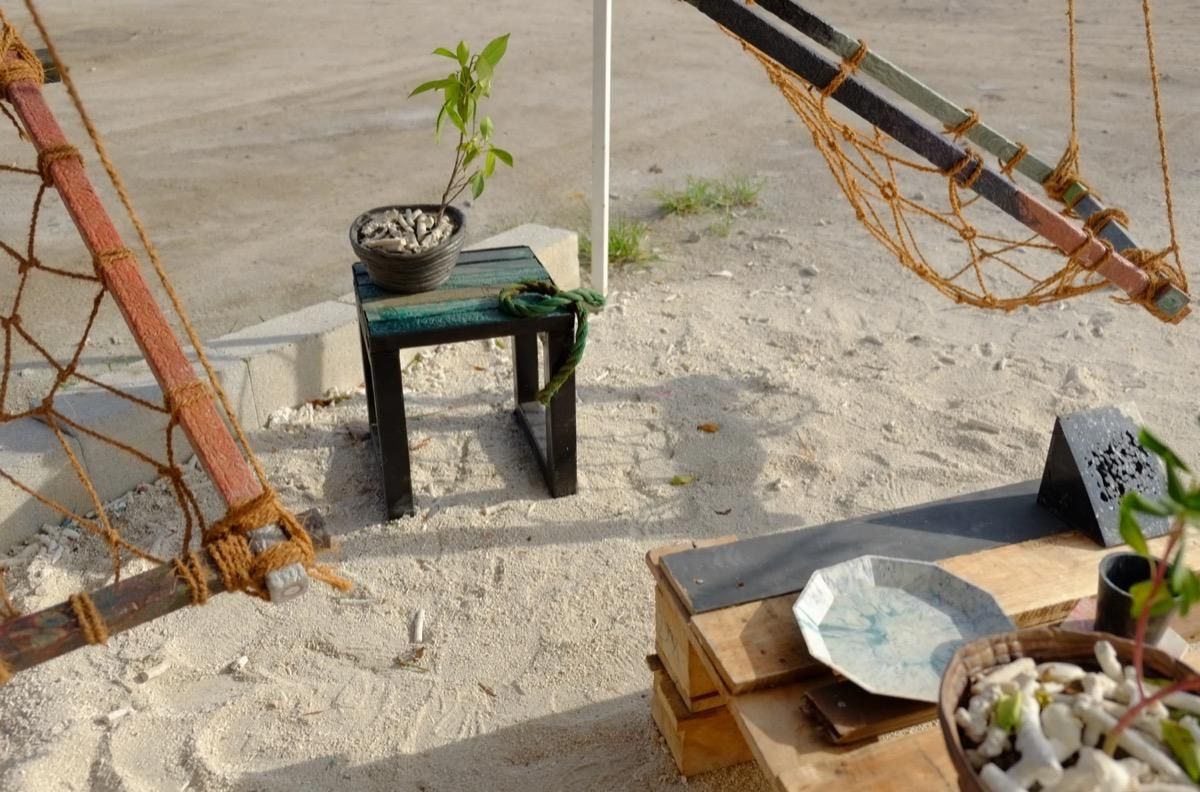
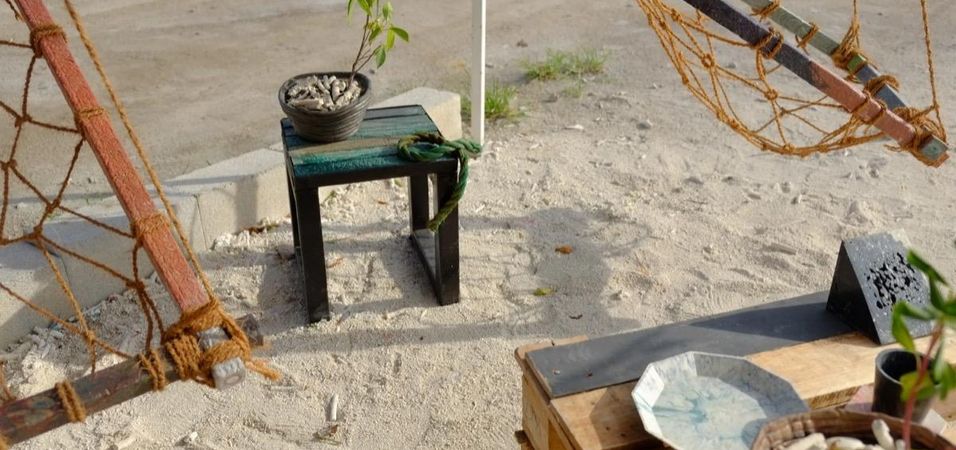
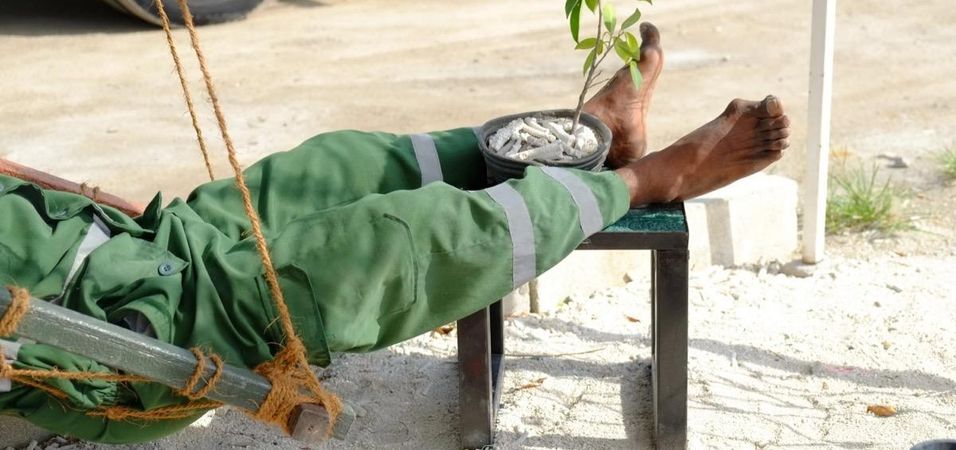
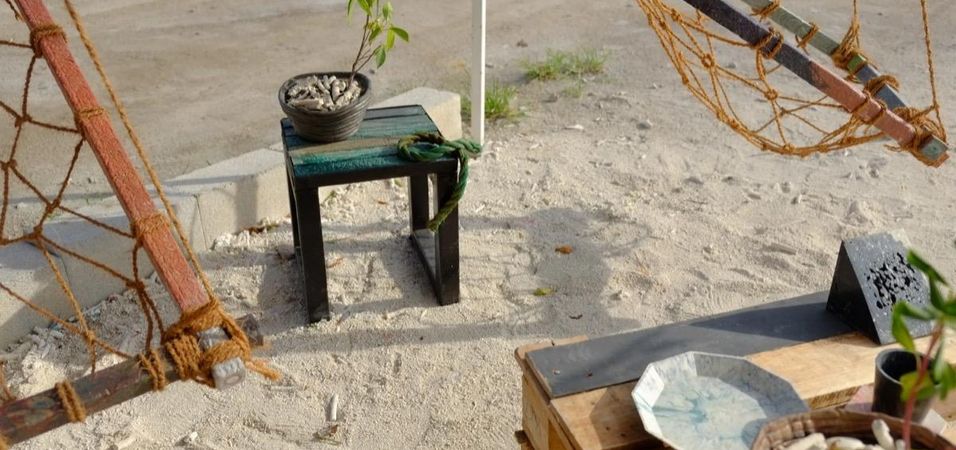
Experiment 06 – Testing Effects of Ultra
Created about 4 years ago
In addition to experimenting with marine textiles, I wanted to get a better understanding of how ultraviolet degradation (common in ocean plastics) affected the material properties of plastic after it’s recycled.
All over the island there were loads of these yellow bottles in varying degrees of degradation, so I used them as a control for the experiment.
To start, we shredded a good-as-new bottle and the most degraded bottle I could find to compare properties of the most extreme types. The degraded bottle was considerably weaker than the new one – you could tear it apart by hand without much effort.
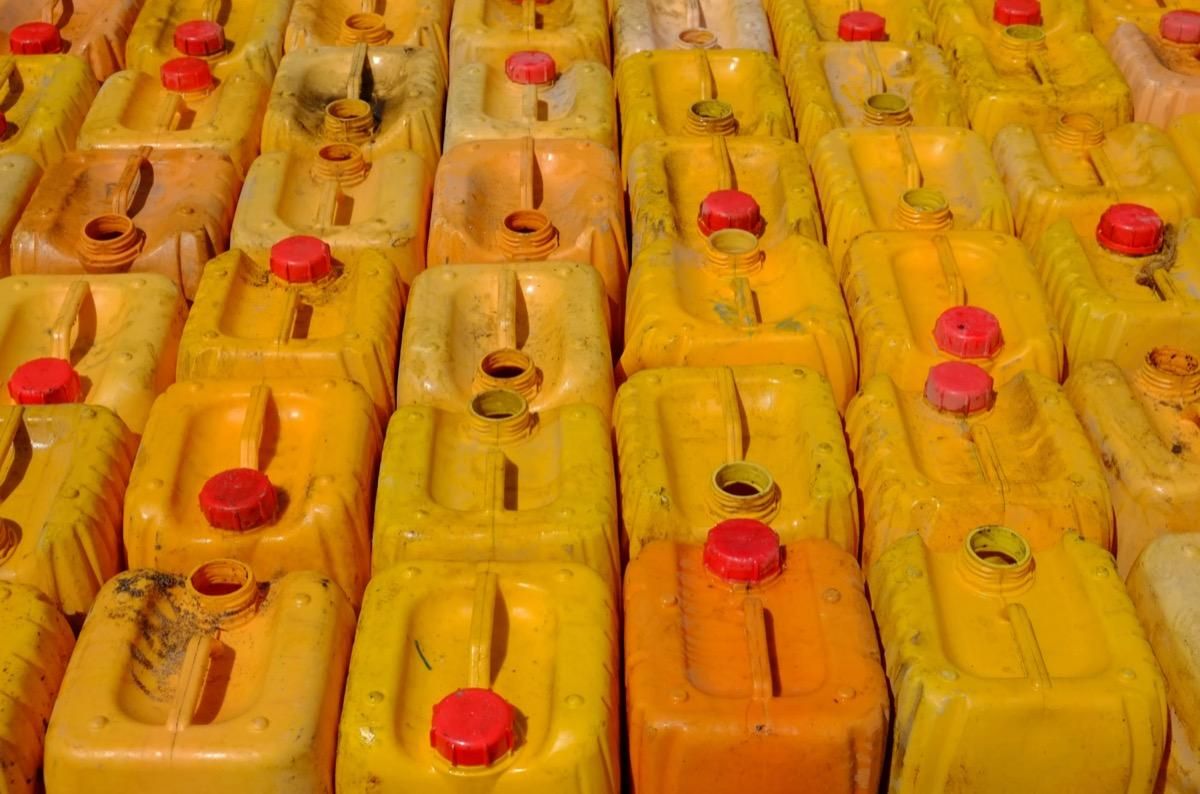
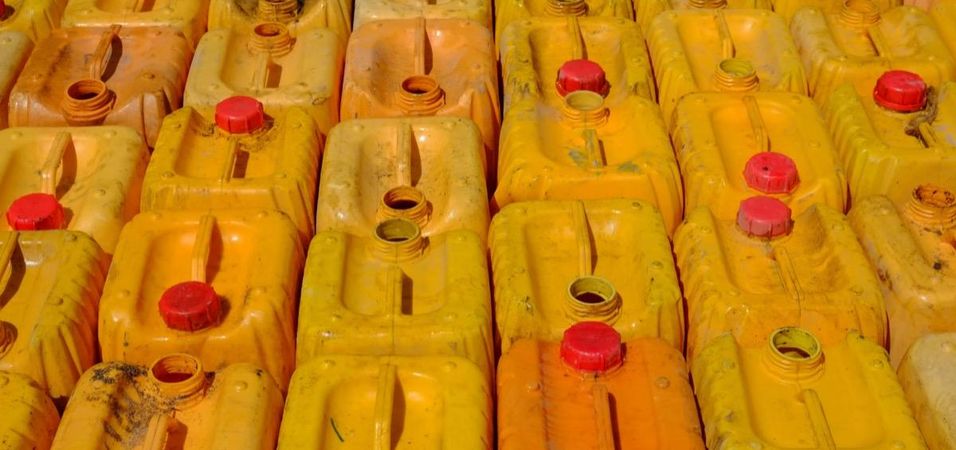
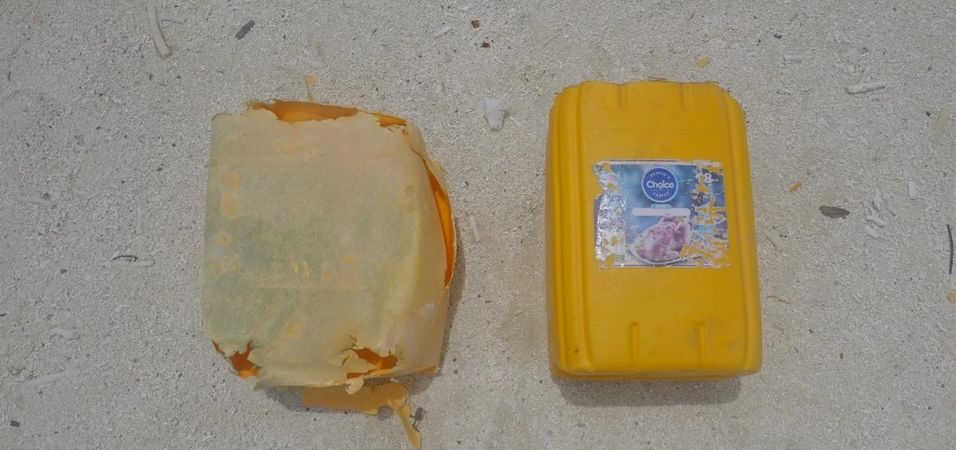
Strength tests
Created about 4 years ago
We used a hydraulic press to test the beams’ flexibility and compression strength.
We applied 12,000 metric tons of force and there didn’t seem to be a substantial difference between the behavior of the beams. Perhaps I was wrong in my previous research
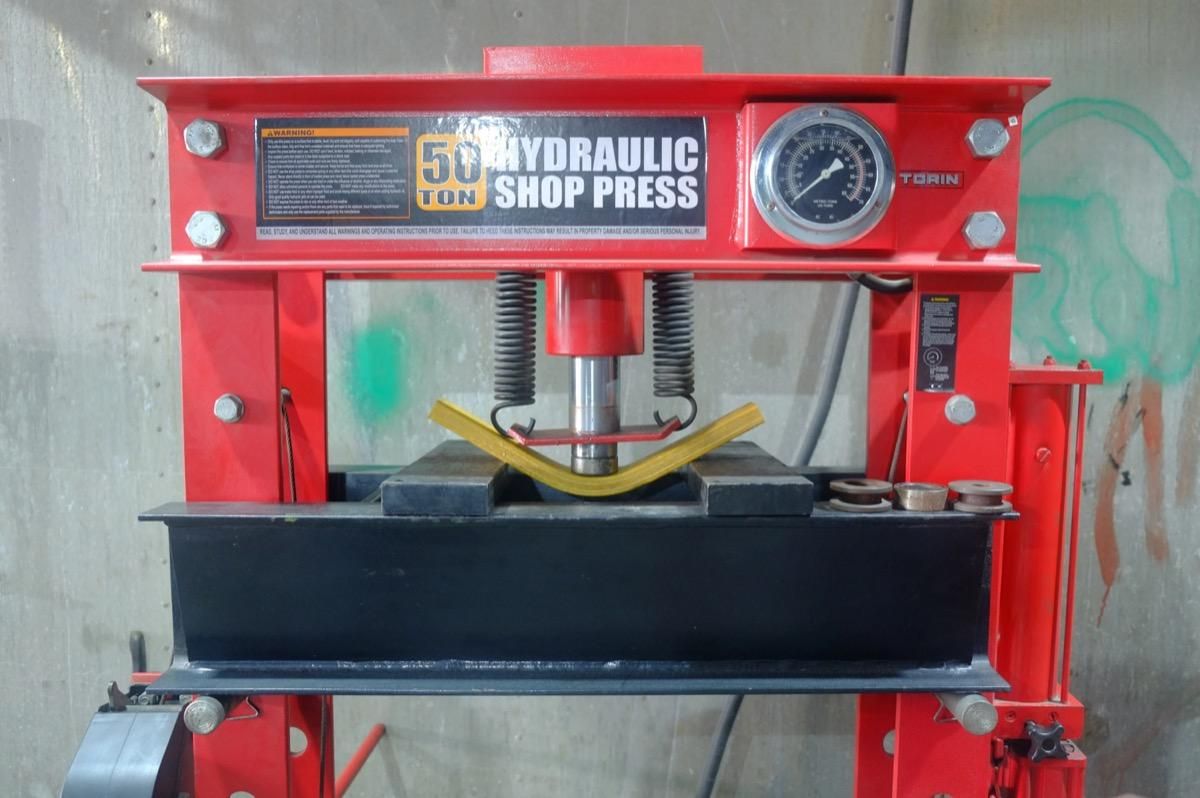
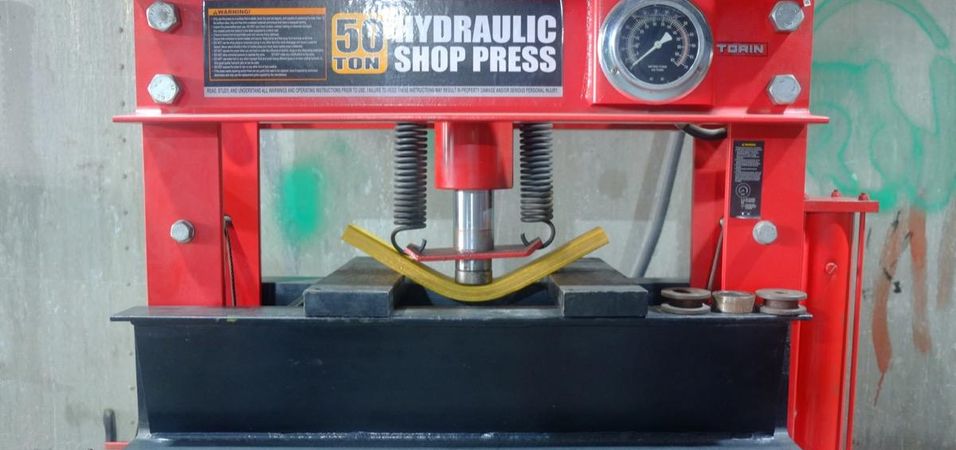
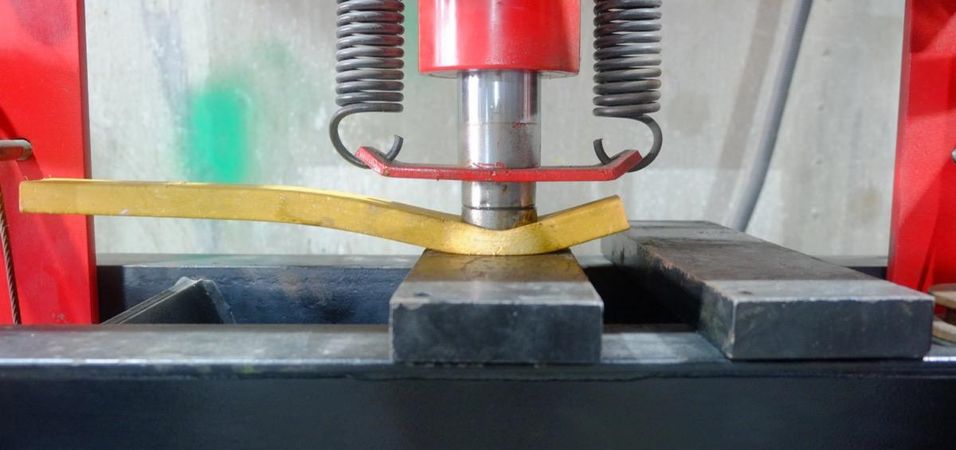
degraded VS non-degraded
Created about 4 years ago
More extensive testing should be done to get a better understanding of how UV degradation affects the properties of plastic, but from this initial test it seems that degraded plastic, once recycled, is still quite strong.
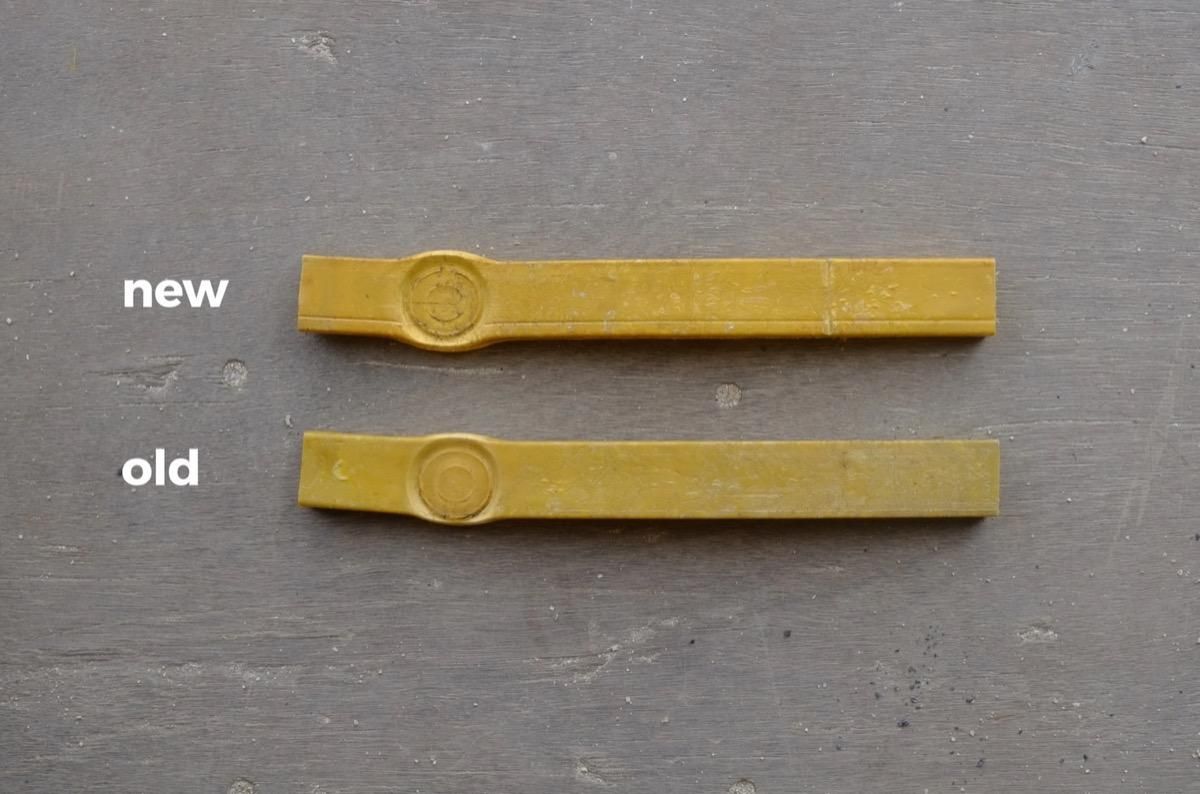
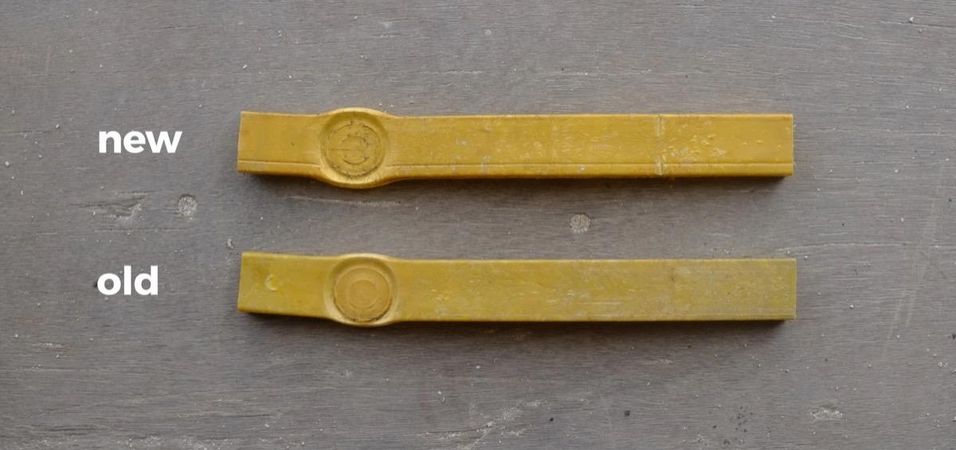
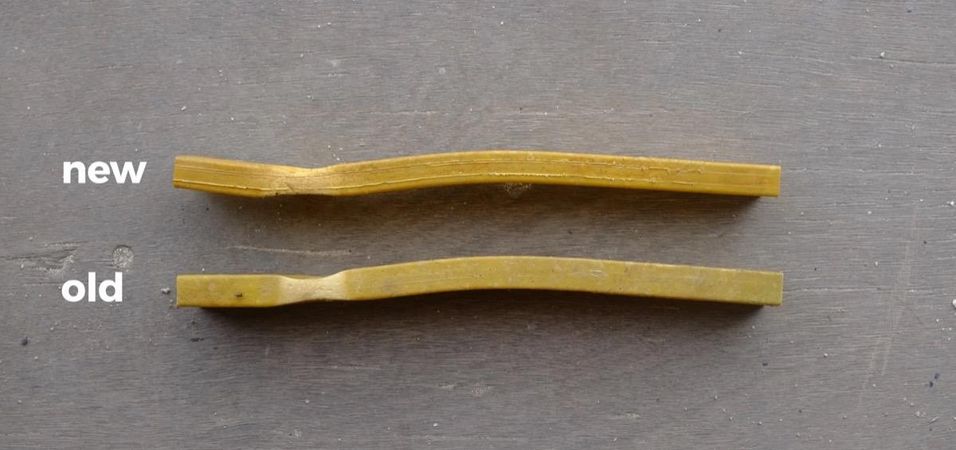
Display board to share our learnings
Created about 4 years agoUpdated over 1 year ago
To share what we learned, I made this display board showing the results of recycling plastic waste that people might not typically think of as a “recyclable”. It’s hanging in the workspace next to the injector.
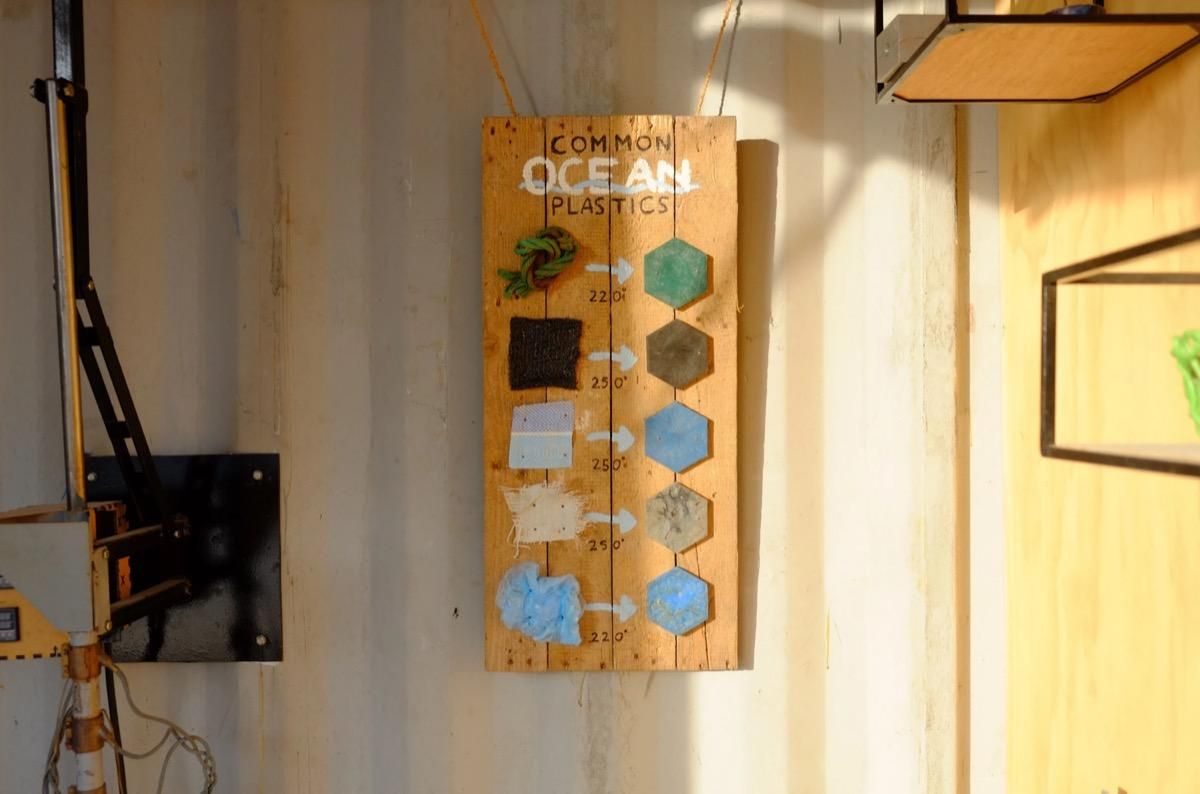
Implementation
Created over 1 year agoUpdated over 1 year ago
Here are some ways this material can be implemented in building products:
1) Make buttons from Ocean Rope
https://community.preciousplastic.com/how-to/make-buttons-from-ocean-rope
2) Boards made from marine litter
https://community.preciousplastic.com/how-to/boards-made-from-marine-litter
3) Products made from marine litter
https://community.preciousplastic.com/how-to/products-made-from-marine-litter
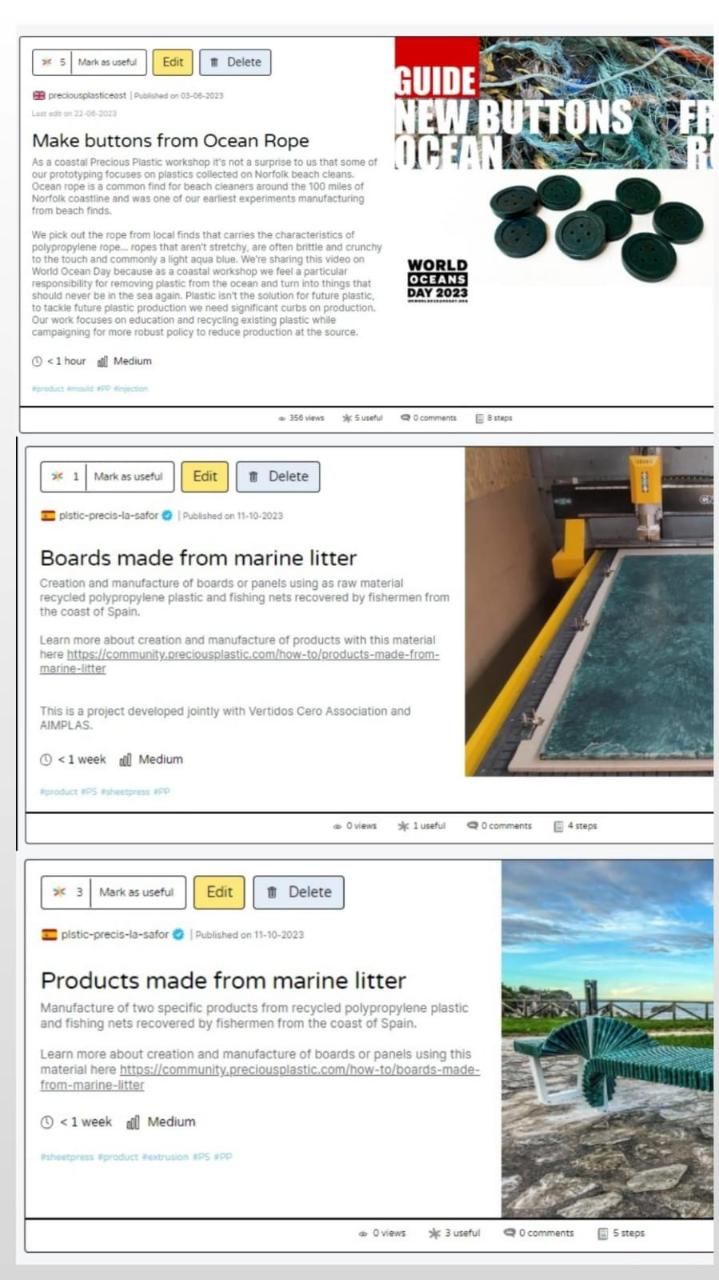