In Progress
Machines
Using the Shredder V2.1 to Recycle 3D prints into Filament
Hi All Jonathan here from The Next Layer. Over the last year, I've been adapting the Shredder 2.1to recycle 3d Prints into new filament. It's been a long and difficult journey, which I documented all of the ups and downs of in my 6 part (and counting) YouTube series (http://jle.vi/frs), but I wanted to share just the top learnings and conclusions for my build here, for others to benefit - as well as the issues I'm having. First, the final setup: -Precious Plastic Shredder 2.1 from PP Capi Spain -30:1 Worm Gear -90L ~3HP Motor -Lovejoy flexible couplers + adapter shank for worm gear. (This proved necessary after bending the driveshaft the first time due to sub-mm differences in height between the shredder and the gear box) Now, the modifications I've made to enable this to work: -5mm sieve. I've found that 4.5mm is too small, and 8mm is much too large. 5mm is the sweet spot for the extruder I'm using, the ArtMe, though I do still have to sieve the material. -High Powered Turbine fan at the top of the hopper to push hot air though. This might not be necessary once I resolve the rubbing/friction issues The Process: After a LOT of trial and error, I've happened upon a process that works: -Shred the material -Sieve the material in a 4.5 or 4mm 3D printed mesh pan. -DO NOT WASH THE MATERIAL IN WATER TO REMOVE DUST, OR YOU'LL INTRODUCE MOULD. -Run a powerful magnet through the material, extensively, the remove metal shredding etc. -Dry the filament in the MICROWAVE (only non-CF materials). Ideally 30 seconds on (high power), 5 minutes off. Transfer containers if the container gets hot. (The Microwave is the only thing I've found that can remove enough of the moisture. A normal oven doesn't do it, but I haven't tried a vacuum oven. Obviously anything that blows hot air around like a filament dryer or food dehydrator is a non-starter). -Extrude the filament in the ArtMe Extruder. Settings seem to depend on color and percentage of fresh filament. I usually extrude 85% recycled material, and for that, the ideal settings are 17.6-18RPM, 25 fan, 176 Degrees celsius. This results in filament that is MOSTLY consistent - 1.72 to 1.76, generally, which is enough for my uses. However, I've spoken to experts, and they've told me that an additional step of pelletizing and re-extruding would yield much more consistent results. Now, the issues I'm facing: I used the shredder for months, but it always generated heat from friction, the driveshaft finally snapped. I thought the friction (and the metal powder in my regrind) was from the knives against the shredder wall, but clearly, it was slowly eating away at the driveshaft. I have NO IDEA how this happened, and would love insights. I think that the driveshaft was mounted at an angle, in the way that the bearings couldn't compensate for, but I don't understand how that would damage. In the interim, I've ordered at 4140 Steel Shaft replacement. Thanks!extrusionshredder
More Information
Project as it stands
Created about 1 month ago
Here is a full cost breakdown of the parts I used - it's not 100% up-to-date, as I haven't added the new driveshaft and new sieve, because I assume others won't break them, if my research is successful 😅
https://jonathanalevi.com/fcb
Here I the video series, if you'd like to follow along:
https://jle.vi/frs
Here are images of the broken driveshaft for your analysis:
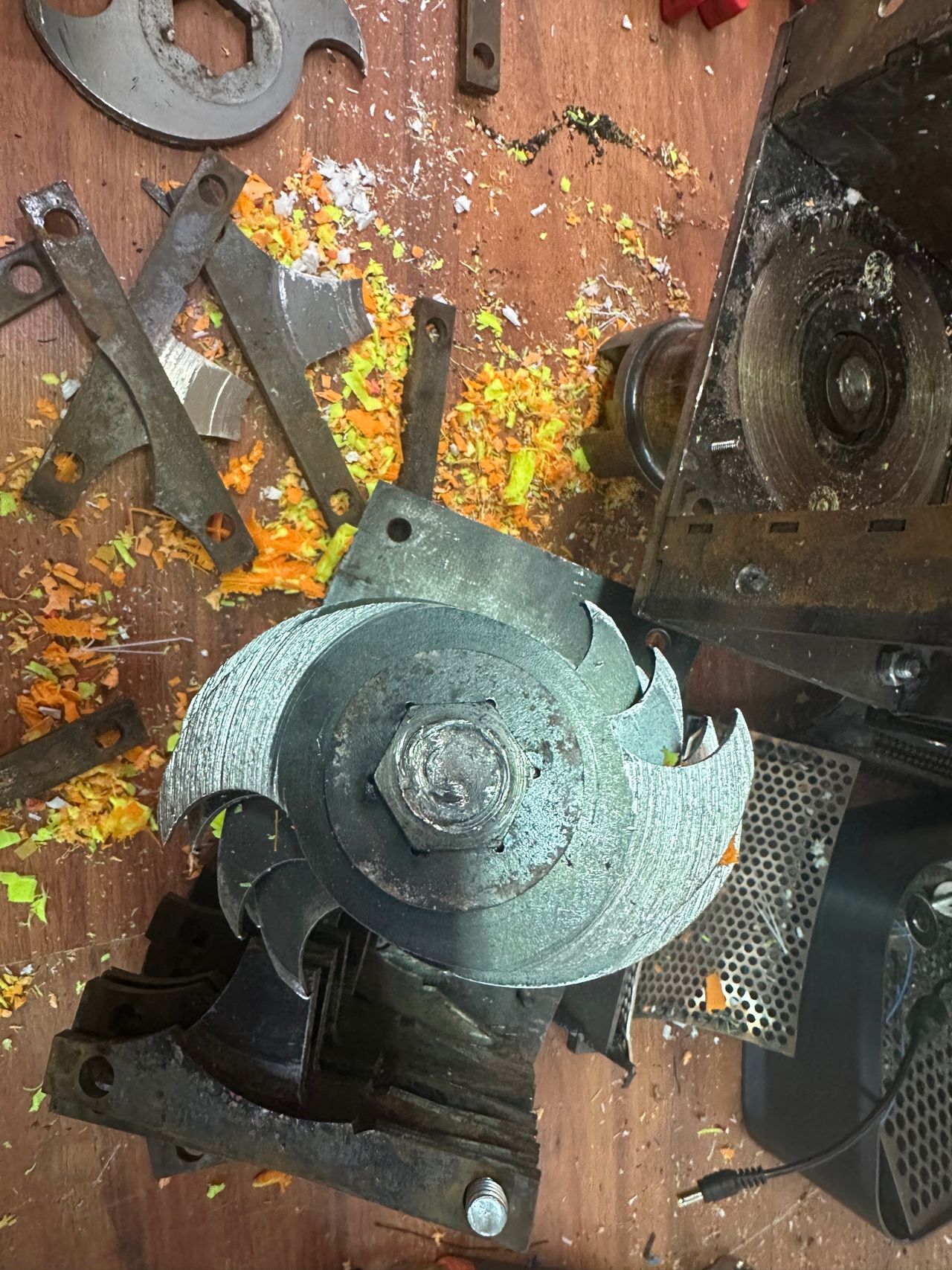
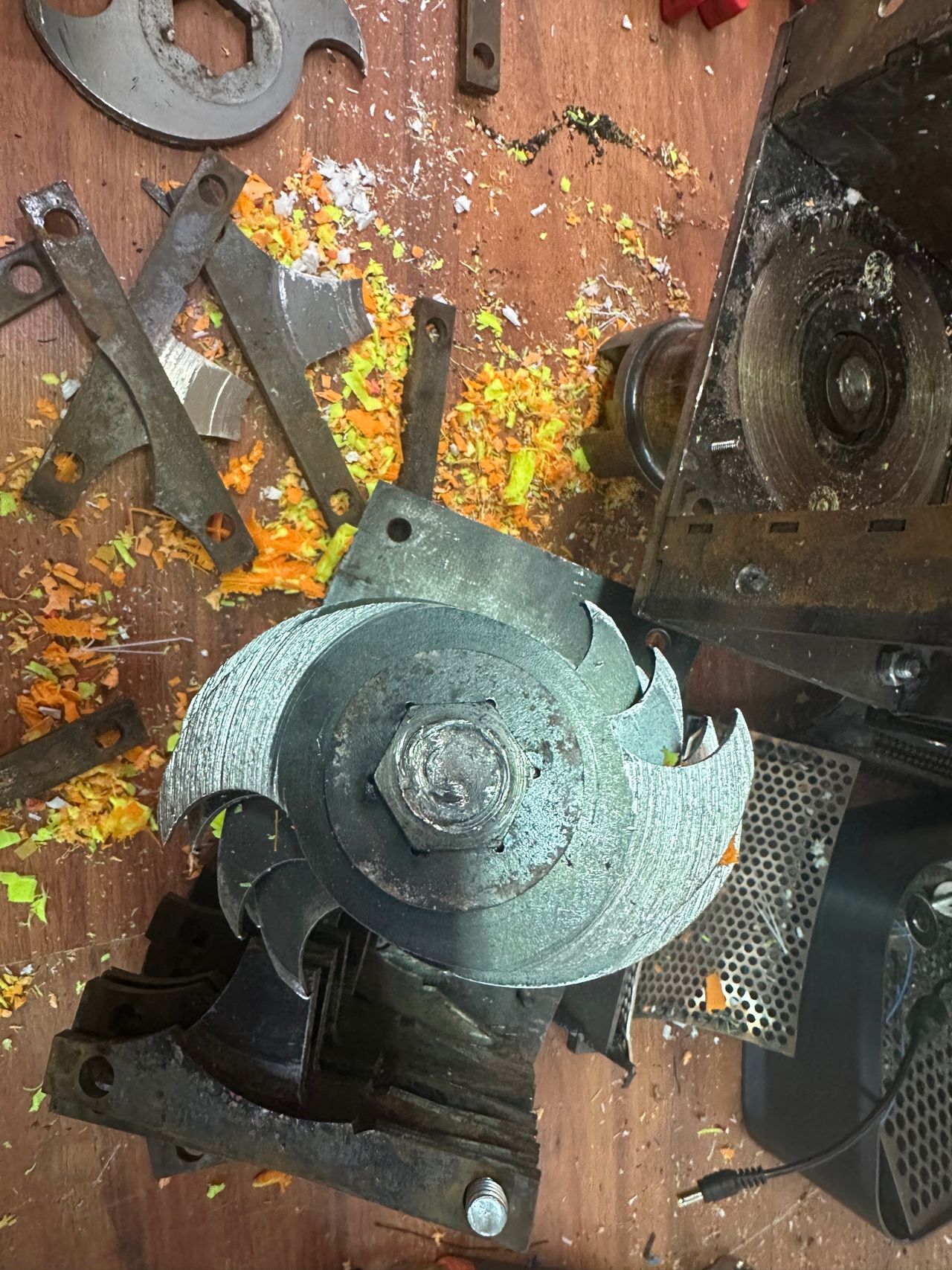
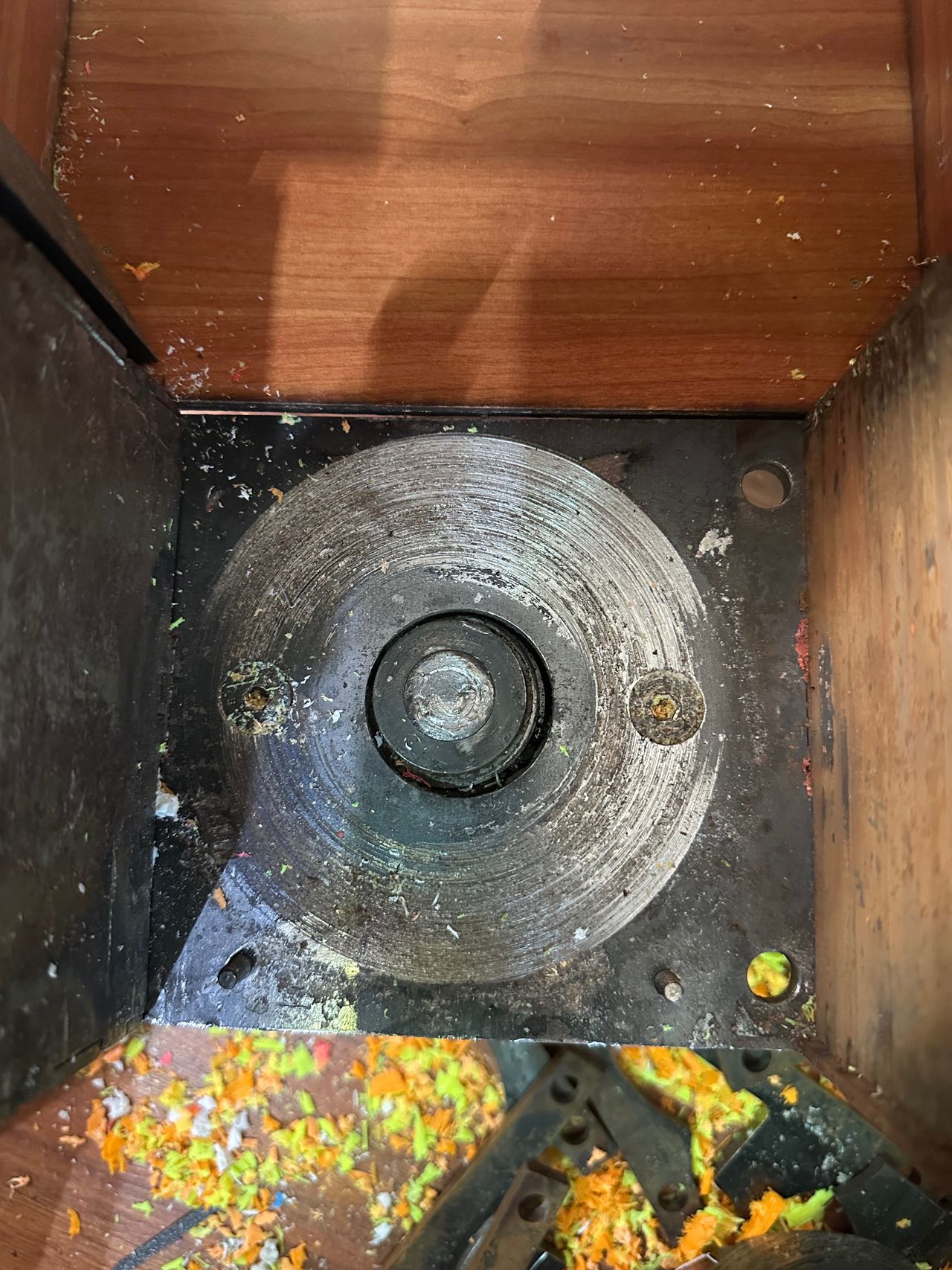