In Progress
Products
Plastic Beam Production Results using multi plastic types
Plastic alloys and mixed film plastic usage in making plastic beams aka eco lumber. To date we have produced in excess of 10 tons of plastic beams.PPHDPELDPE
More Information
lessons learned
Created about 1 year ago
Lessons learned:
1 molds have to be filled as fast as possible. We found that going from a 5hp extrusion machine running the pro style extrusion screw would make a 25x50mm board 1250mm long would take about 5 min. However upgrading to 10hp and a 50mm diameter extrusion screw resulted in the same board filling in under 1 min. The plastic has to fill the mold before it cools. Cooling results in back pressure, resulting in slower filling and rupturing of the molds.
2 We found that the ideal mix of HDPE and PP is 8 parts PP to 5 parts HDPE. Too much PE plastic results in a beam that is very slow to fill the mold. The consistency is akin to chewing gum. PP plastic on the other hand is thin and flows well, has a stiff board. However it results in a board that will melt rather than cut or drill, and prone to breaking.
3 However you can vary your ratio depending on the plastic available. Just keep in mind the limitations in section 2
flex plastics in the beams
Created about 1 year ago
Multi layer plastics will work, as well as aluminum film plastics and plastic labels from soda bottles. However, keep in mind that SOME plastic packaging emits toxic fumes when being processed. We have found that the packaging from local produced vinegar sachet emit bad fumes.
We found that some film plastics like from powdered milk and Tang powder, have a PET layer. PET will not mix well with the lumber, but it can be added in small amounts, It will increase the strength of the beam.
Plastic envelopes with shipping labels will also extrude. However the plastic will be quite thick like the base HDPE and LDPE it is made from and needs thinning down with PP plastic to extrude well.
If you mix flex plastics together you will find you will get a light green as the average color. You will need to add in a colorant to make it durable for outdoors.
We use iron oxide pigment powder for cement, and or powdered charcoal if we are not using recycled plastic pellet with coloring
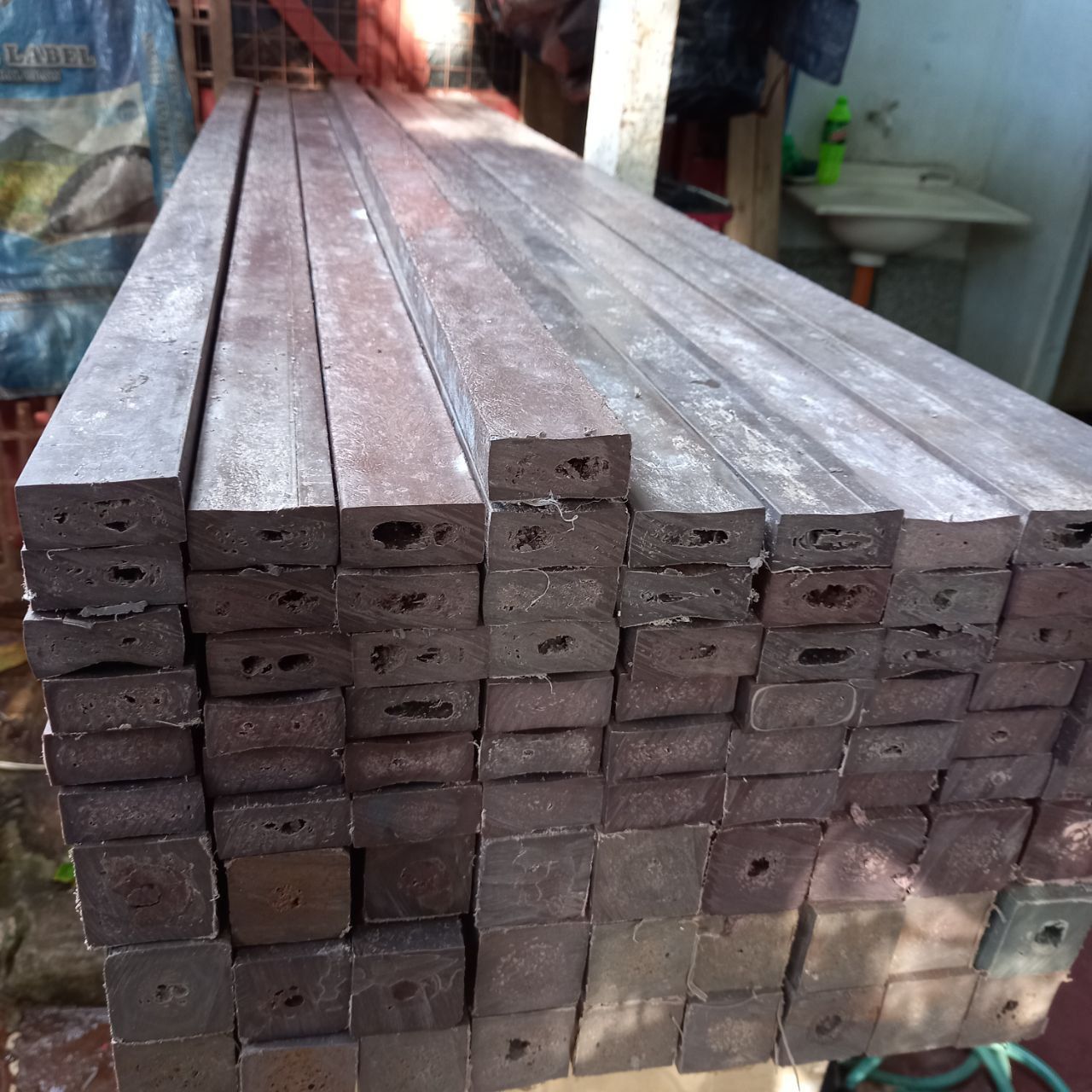
Flex plastic agglomeration
Created about 1 year ago
We have found that film plastics are difficult to process without some method of forcing the plastic into the extrusion machine.
To date we are experimenting with both a crammer hopper to force the plastic into the extrusion screw and by using a feed pellet mill to pelletize the flax plastics.
We are also experimenting with a multi stage shredder system. Where we start out with the 5hp dual shaft machine to break down the big plastics with large 10mm wide teeth, and then a second stage to the v3 shredder.
We are observing that under use with the dual shaft machine, it will somewhat fuse the film plastic into chunks.
We are looking at trying 2 different experiments.
today we will experiment with a cascade of the two shredders. Where the dual shaft shredder directly feeds into the v3 shredder. We hypostasize that the heat added durning the first shred, and then immediately falling into the second shredder while hot will generate enough heat to agglomerate/densify plasti
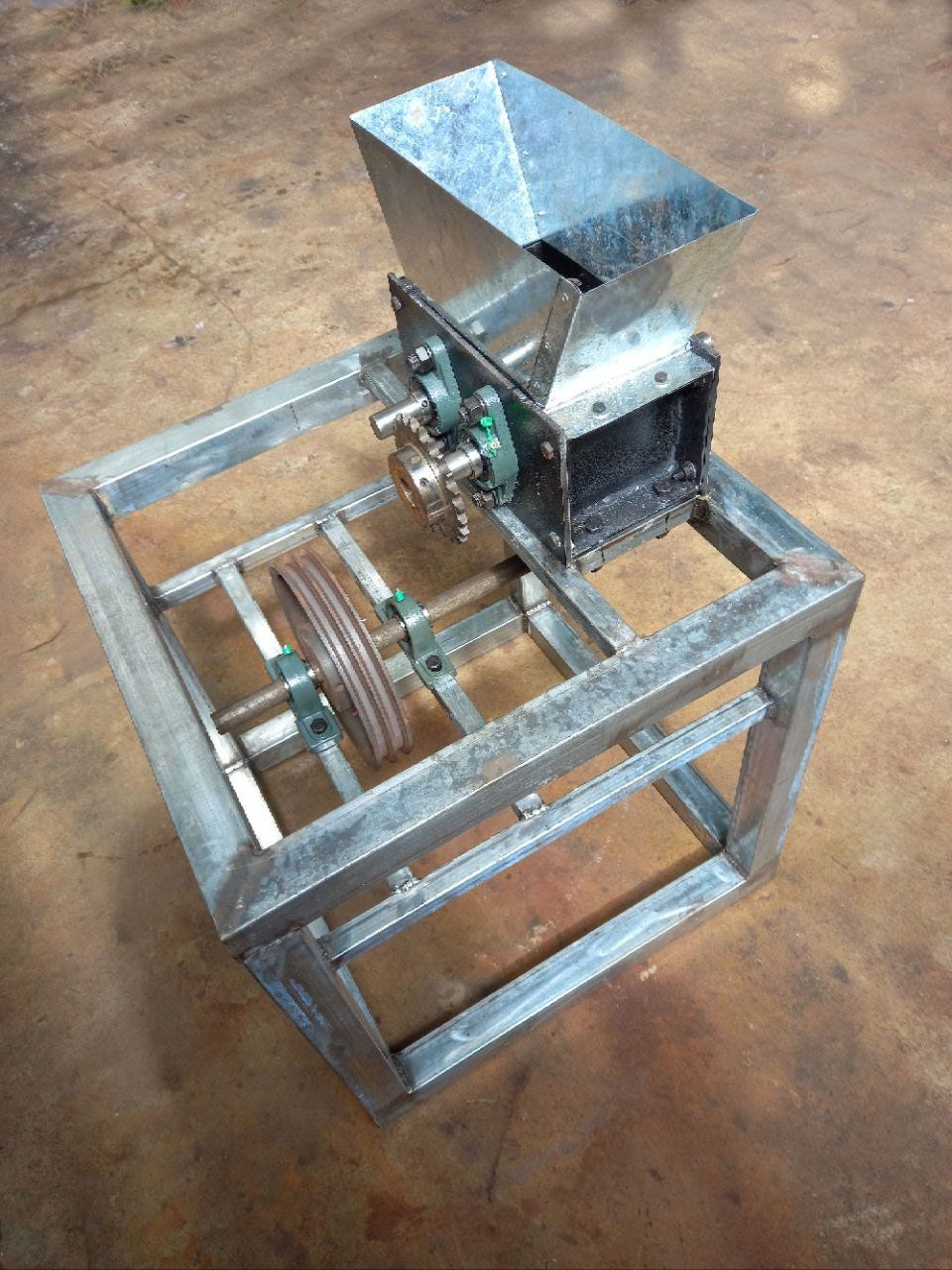
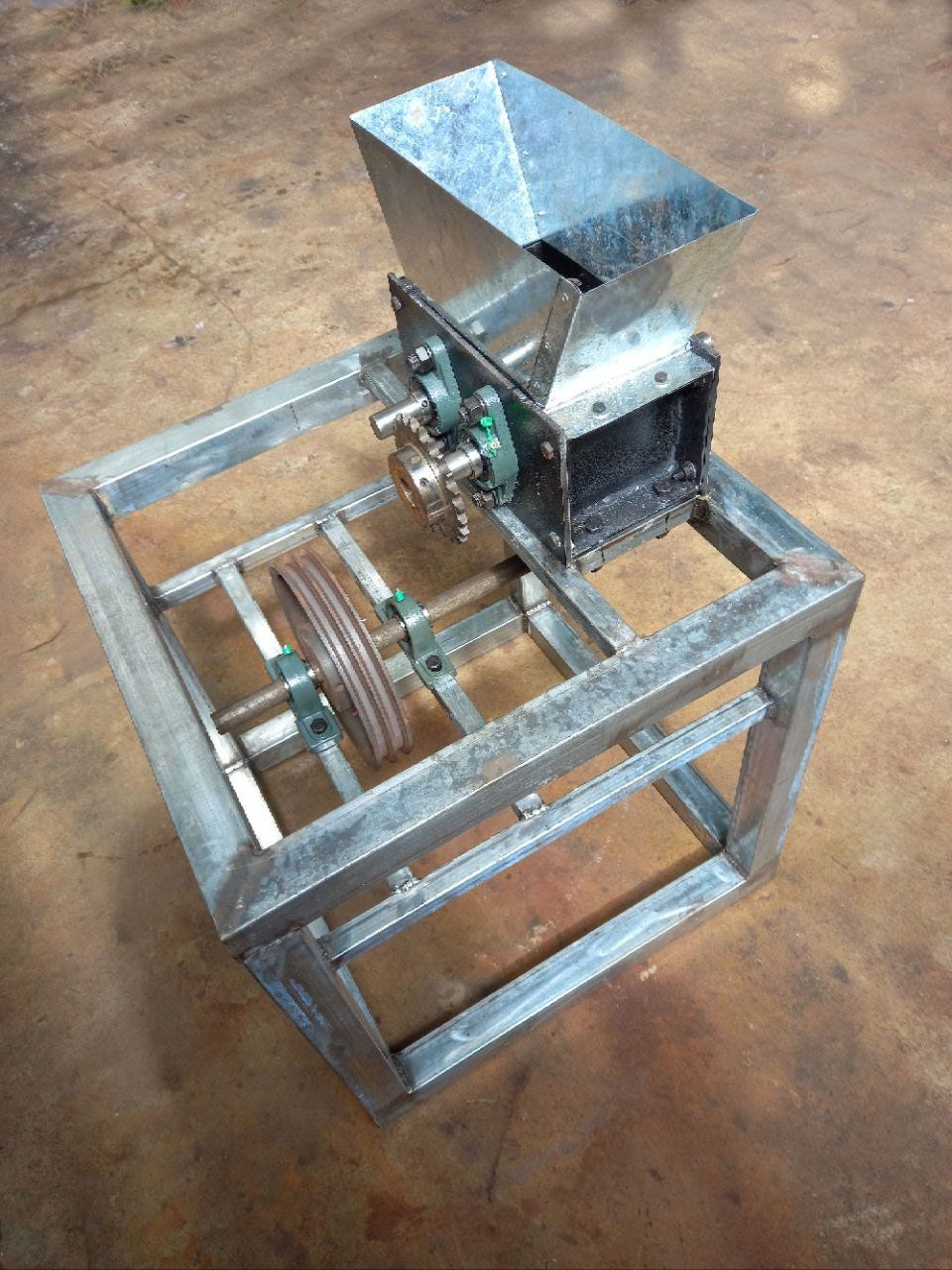
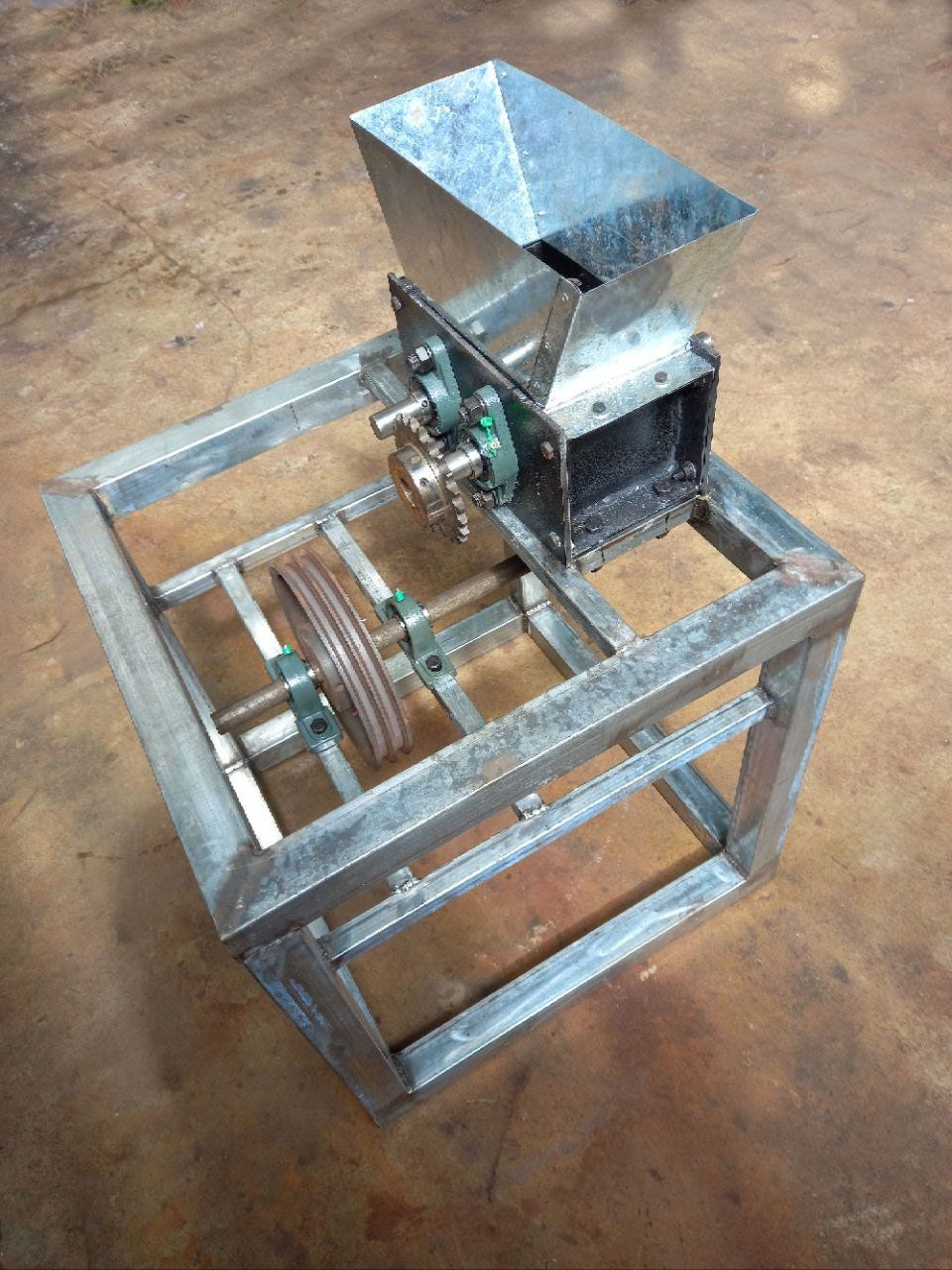
Made by
precious-plastic-philippines