Completed
Make open-source Arbor Press injection machine
Research, design, build and document an Arbor press injection machine: - Follow the Precious Plastic design guidelines and CE safety requirements. - Research best practices of design, engineering, material/part sourcing, etc from community members, particularly from those with experience building and using different Arbor Press designs. - Document a final design for this machine following the Precious Plastic documentation structure.injection
More Information
Research findings
Created about 3 years ago
Usability evaluation
- Problems:
+ strenght needed to operate the machine
+ dangerous way of attachin the mould to the machine
+ nozzle clogs and leaks
+ exposed band heaters is dangerous and burn plastic flakes that fall on them.
Buildability evaluation
- Results:
+ tolerance between the plunger and injection barrel is hard to achieve
+ bolting preference over welding
+ welding onto the barrel causes warpage
After several interviews we discover that the different users (builders and operators) have different goals with the injection machine, objectives ranging from educational purposes to semi-industrial production. So we think that probably is best to go for a midpoint option.
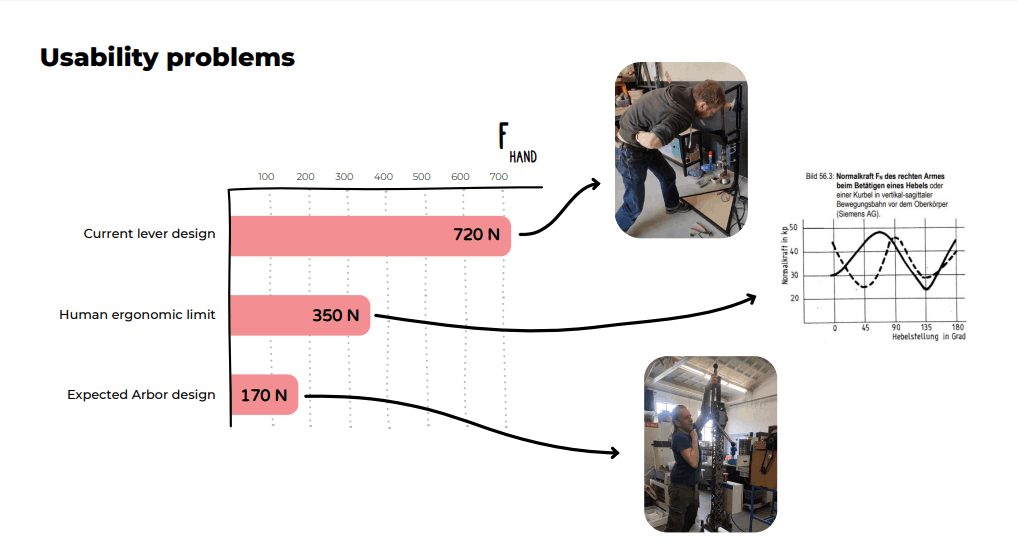
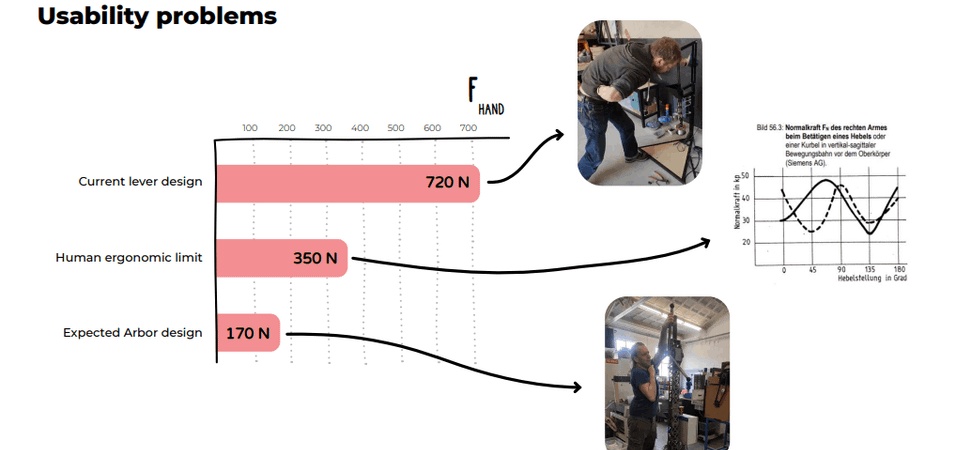
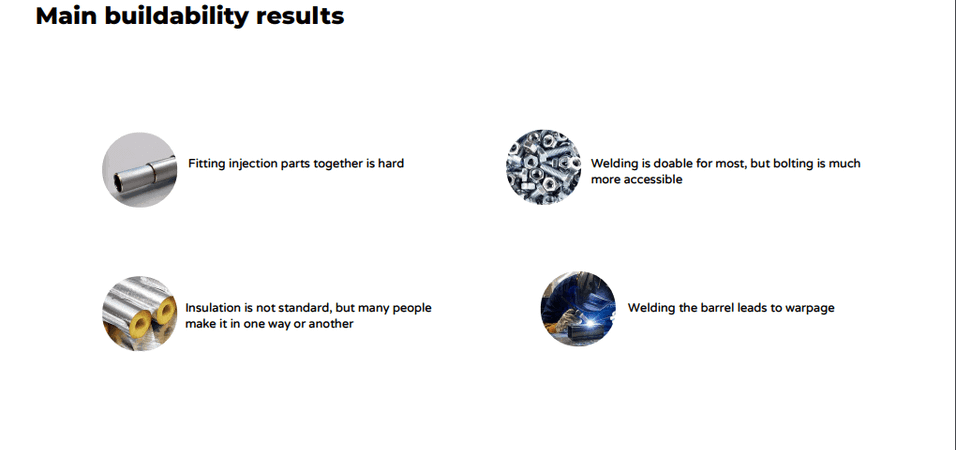
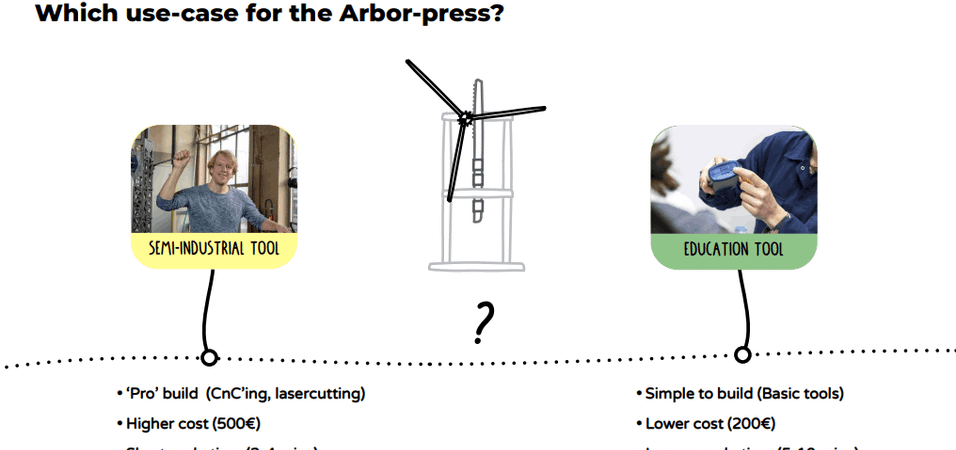
Best practices
Created about 3 years ago
After several discussion on discord and looking at people's experiences designing and building different injection machines all over the world we grouped what we consider the "best practices"
- Arbor mechanism
+ Human dorce around 350N
+ Should minimally produce ยฑ2300 N on melt
+ Different gear type for different productions goals.
- Nozzle
Comparing the screwing system with the auto-engaging nozzle, we realized that the auto-egaging nozzle can reduce significantly the cycle time as well as making the operation of this machine safer and with less waste of plastic during the process, since the threaded nozzle has a much bigger opening (1/2'') compare to the other option (ยฑ 5mm).
- Clamping system
There are several ways of clamping the mould to the machine using the auto-engaging nozzle:
+ Clamping table with hydraulic press
+ Springloaded barrel
+ Spring-toggled table
+ Car jack
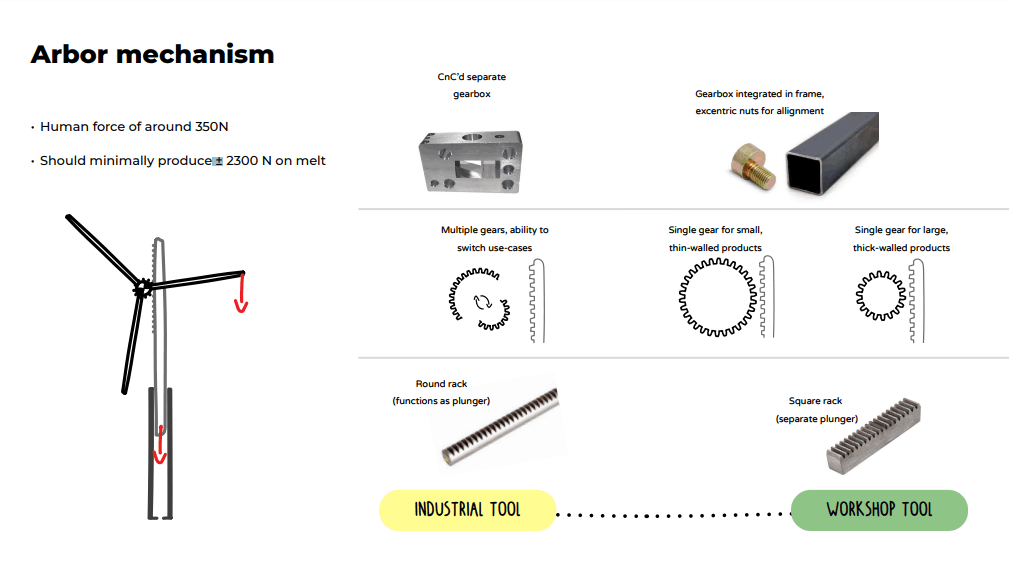
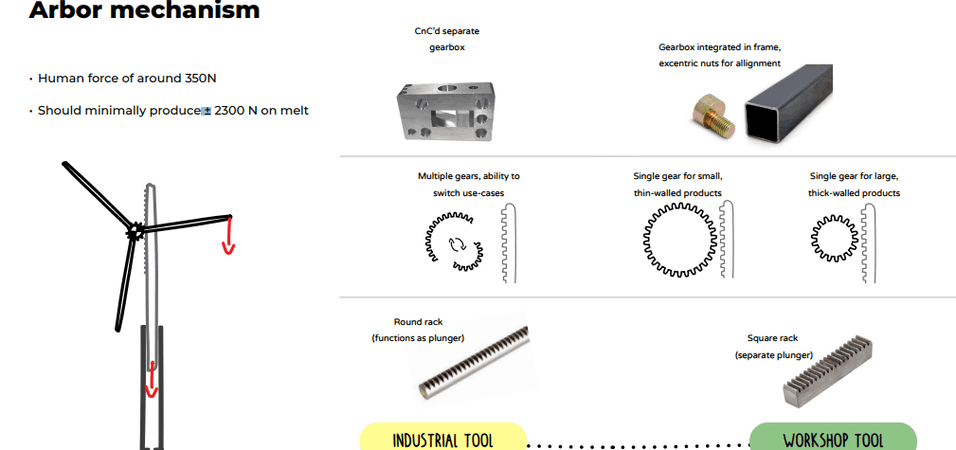
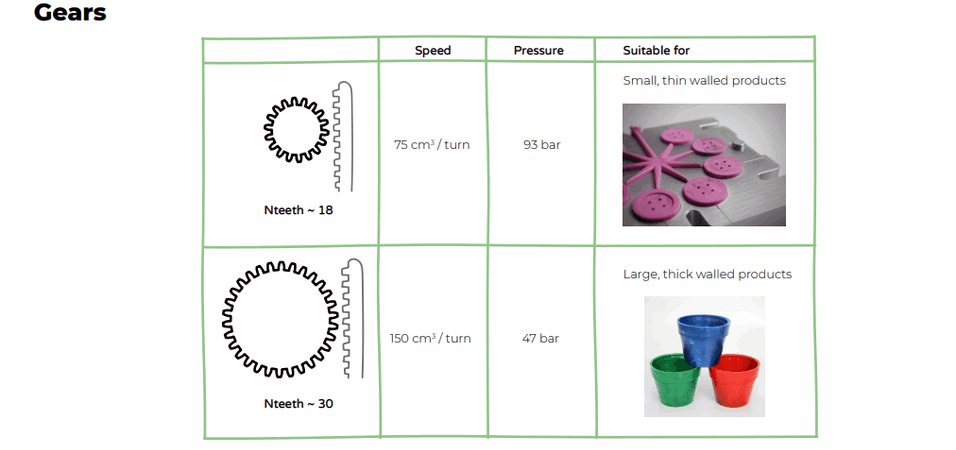
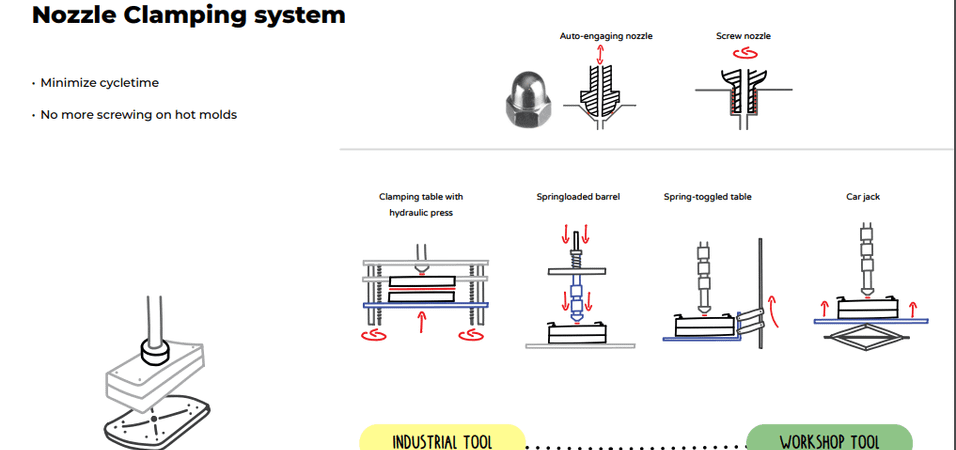
Design direction
Created about 3 years agoUpdated about 3 years ago
As a first phase of this project, after all the research and interviews, we came up with a list of requirements , to then move on to the prototyping and testing phase, which will lead to the second iteration of this Arbor press design.
These are the requirements that we will follow for the first prototype:
- Arbor-system with square rack
- Interchangeable gear system
- Integrated gearbox using eccentric nuts for alignment
- Auto engaging nozzle with springloaded barrel clamping system
- Same barrel dimensions (26mm)
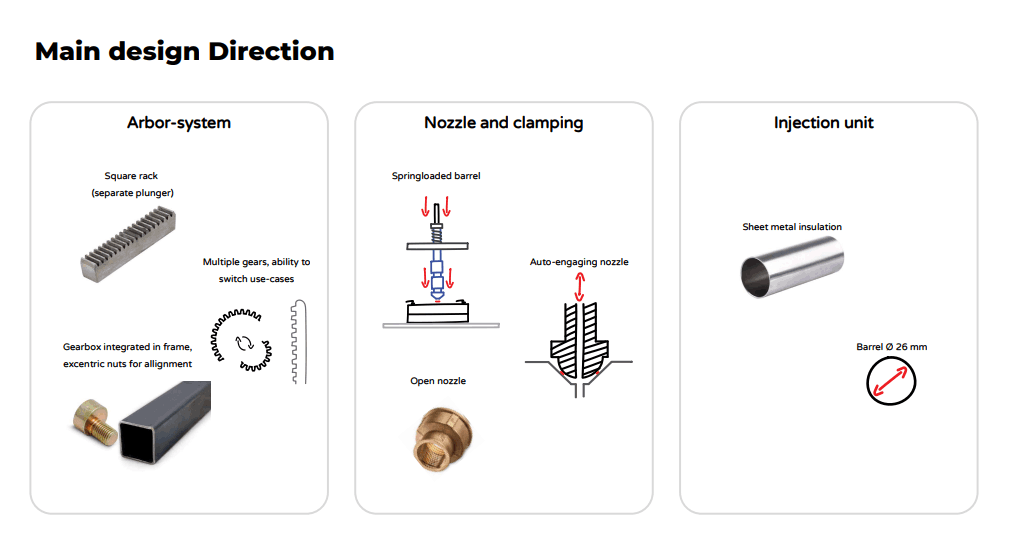
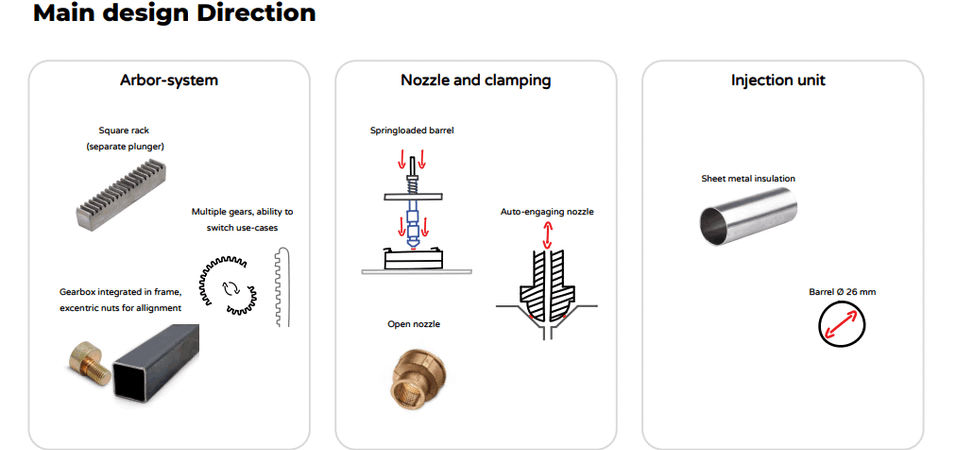
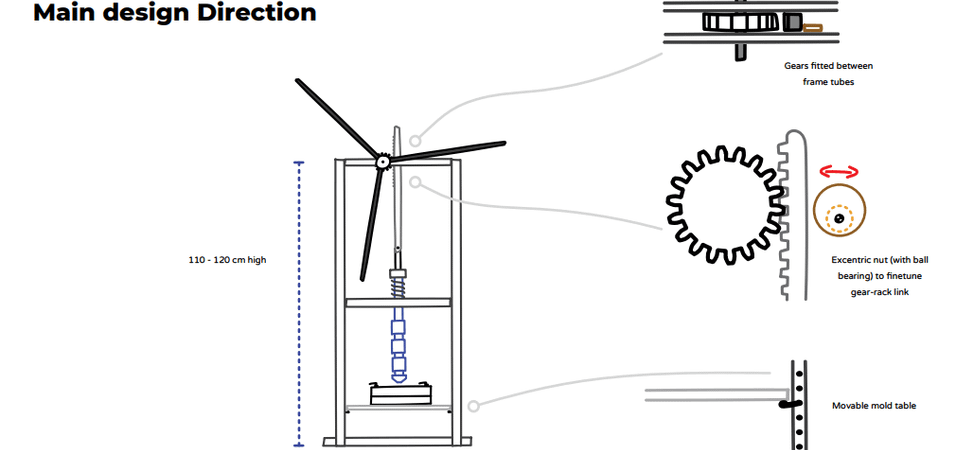
First CAD
Created almost 3 years agoUpdated almost 3 years ago
For this first update, Joost mainly worked on the suspension of the rack and spur gear. These need to fit together just right to ensure a proper working machine. As this is pretty difficult without a CnC, the current solution is using two eccentrically round bars which the user can twist to adjust the rack position. Perpendicular to this, the rack fits between two square bars with 0.5mm of slack so it can move up and down easily.
The spur gear (mod3, 22 teeth) is attached on the main axis by a bolt and is suspended between two pillow-block bearings, which are relatively easy to get. Both this axis and the eccentric round bars are the same diameter and material as the plunger, so they can be bought as one piece.
Things he kept in mind based on the surveys and conclusions:
To make the machine as accessible and buildable as possible in all global contexts.
Practically, means the following:
- No CnC-ing
- No lathe-work
- (almost) No welding
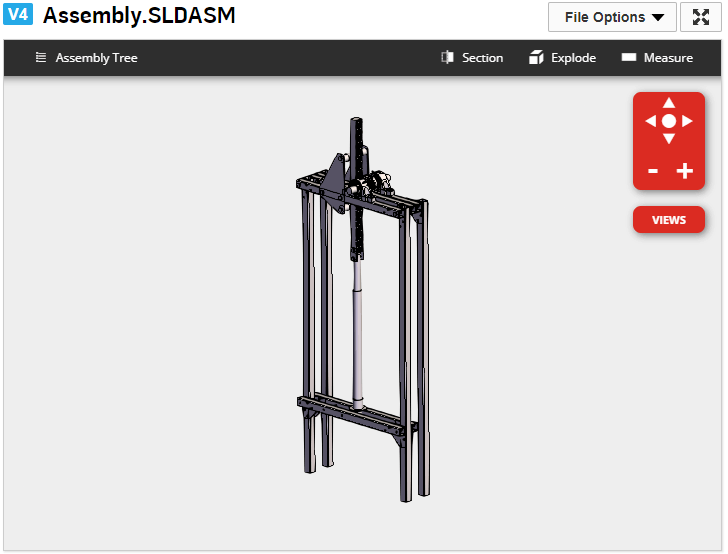
Feedback open meeting
Created almost 3 years ago
After an intense feedback round with some community members, sharing different opinions, experiences and suggestions one of the main things we conclude that welding and machining (as manufacturing method) are both crucial for simplifying the building and making a longlasting and reliable machine respectively.
Which translates on having to do significant modifications to the initial proposal. In the following pictures you can see how Joost already started working towards that approach, though still some directions need to be discussed.
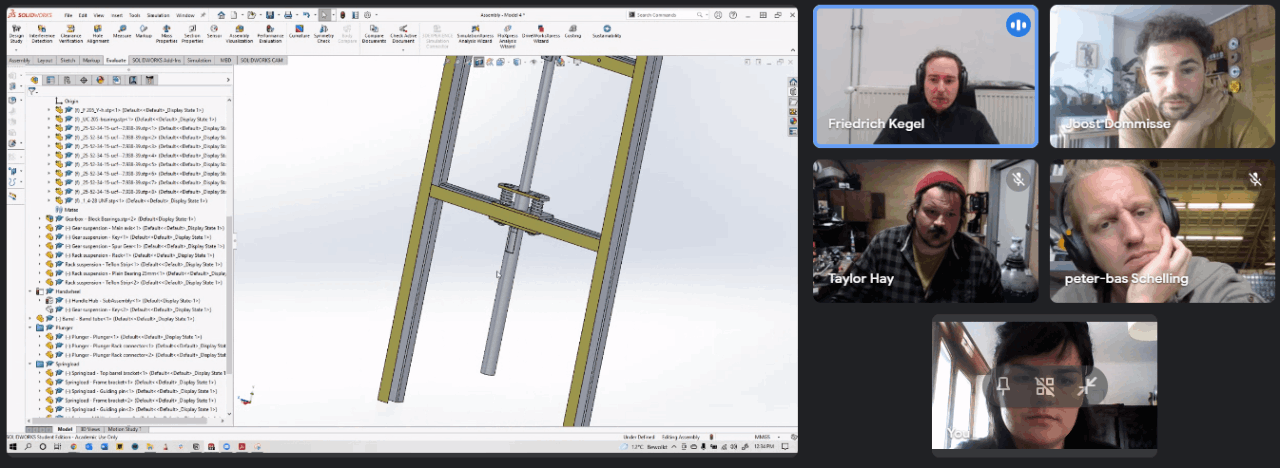
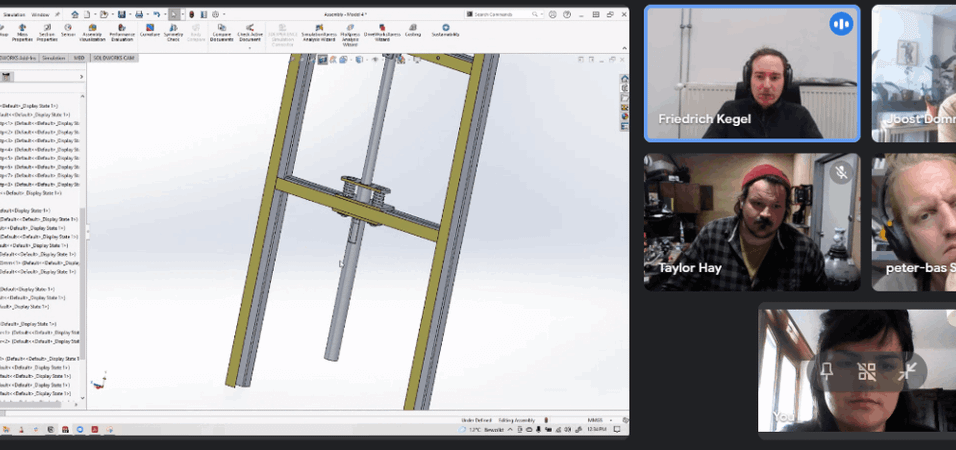
-181481fbe2a.png?width=956&height=450)
-181481fd654.png?width=956&height=450)
Conclusions
Created almost 3 years agoUpdated almost 3 years ago
So after the last feedback round, Joost put the feedback together in a very nice diagram that shows the different assemblies of the machine and all the options and ways of building the same with different techniques / manufacturing methods. We are still working on which one we will choose from each section (for the first prototype) but i invite you all to take a look at this Loom video to undestand better what im talking about ๐ https://www.loom.com/share/70397b5af9ad48ddb9e8a4ce0778e9ea and then jump into this miro board ๐ https://miro.com/welcomeonboard/TDdzQ0FqRUdka3hQSEpHdktjOW5xcDBiejVOVGR0aDBnTjc0dm5DN1Voc2t6dGRtTkFFbHpYaFBpdkdrSVdwT3wzNDU4NzY0NTI2OTg4MzE1NjM3?share_link_id=878038696431 to have a closer look to the diagram and add some more ways of bulding the same part (if you feel thereโs any missing), we already added our comments ๐ .
We feel this kind of tools will allow us and the community have a better overview of the different ways of building the same machine and at the same time will make it easier for others to contribute with designing and prototyping a specific part or assembly of a machine. What do you think?๐ค
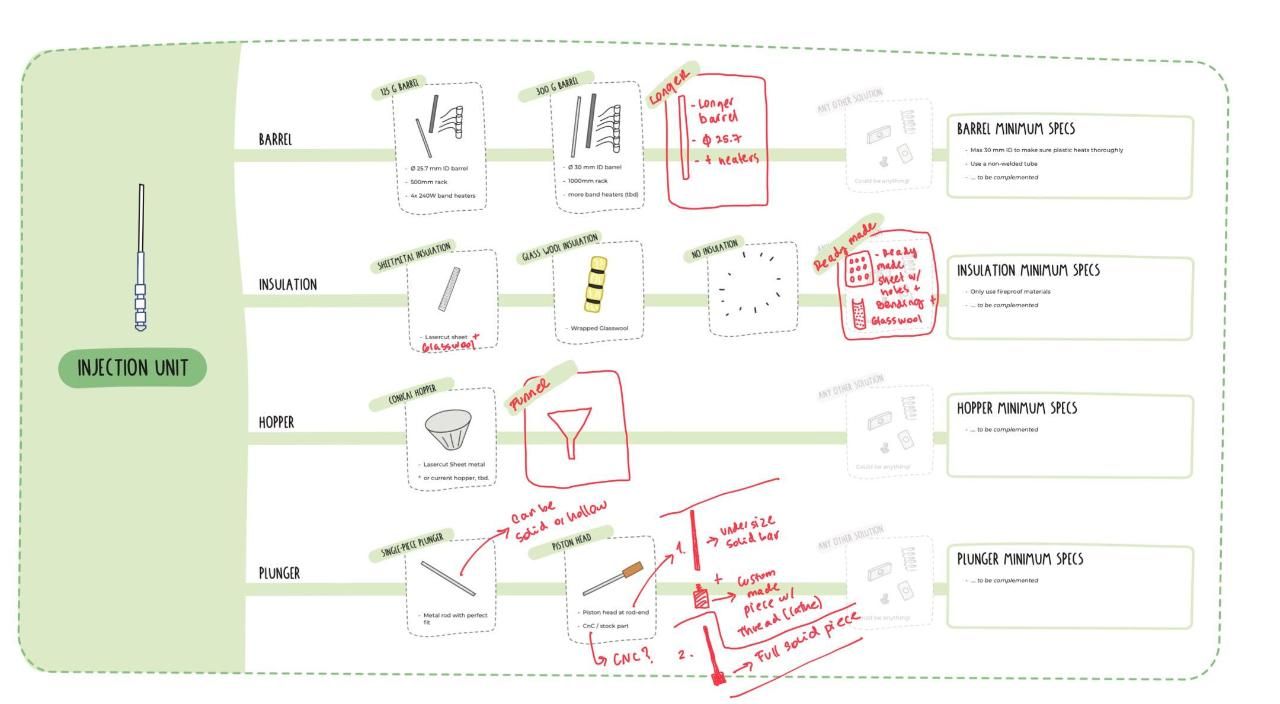
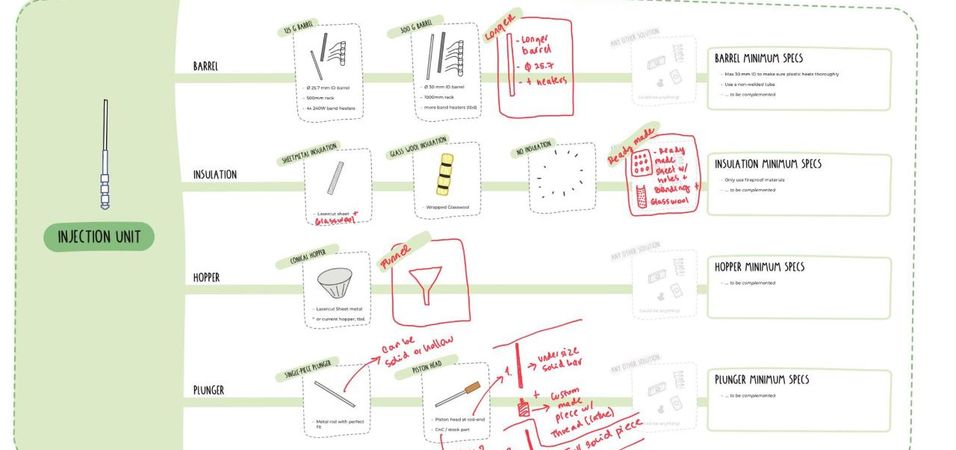
-181488fa5db.jpg?width=956&height=450)
-181488fb1af.jpg?width=956&height=450)
-181488ff129.jpg?width=956&height=450)
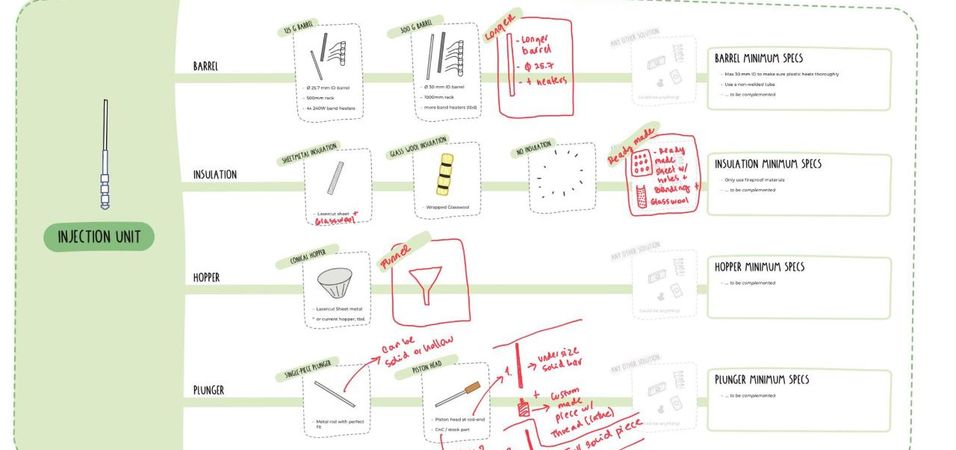