In Progress
Other
Compression Moulding
We research about the process parameters and mould design guidelines for compression moulding. Where many other processes were researched widely within v4 the area of compression moulding stayed behind a bit. While other community members already using these processes for a variety of products such as chair elements or speakers, there is little public information about it. The advantage of compression moulding is in the area of mid-size productions where the processing of sheet material is too time and labour intensive. We will research into the necessary equipment and accessories to conduct compression moulding for production.researchcompressionmould
More Information
Project Phases
Created about 1 year agoUpdated 8 months ago
Research Phase
In the first part basic reasearch about compression moulding is conducted:
- Basic research about machine types
- Verification of heating and cooling time to the calculations
- Granule densities g/cm³ as it influences the mould design
For this initial phase a basic sample mould was designed to be used in a standard workshop press. The mould is equipped with two elements for heating and for cooling to verify initial calculations.
Testing Phase
Here the mould design is refined to test:
- mould design features
- iterate cooling and heating
- (comparison between electric and liquid heating - if possible)
- Granule shapes and design influences
- Design a showcase product that exceeds the standard injection volumes largely
- Verify the researched paremeters with it
- Defects that occur and sources of these
For the tests a larger press will be sourced either as a standard press to modify to make it work or as second hand machine
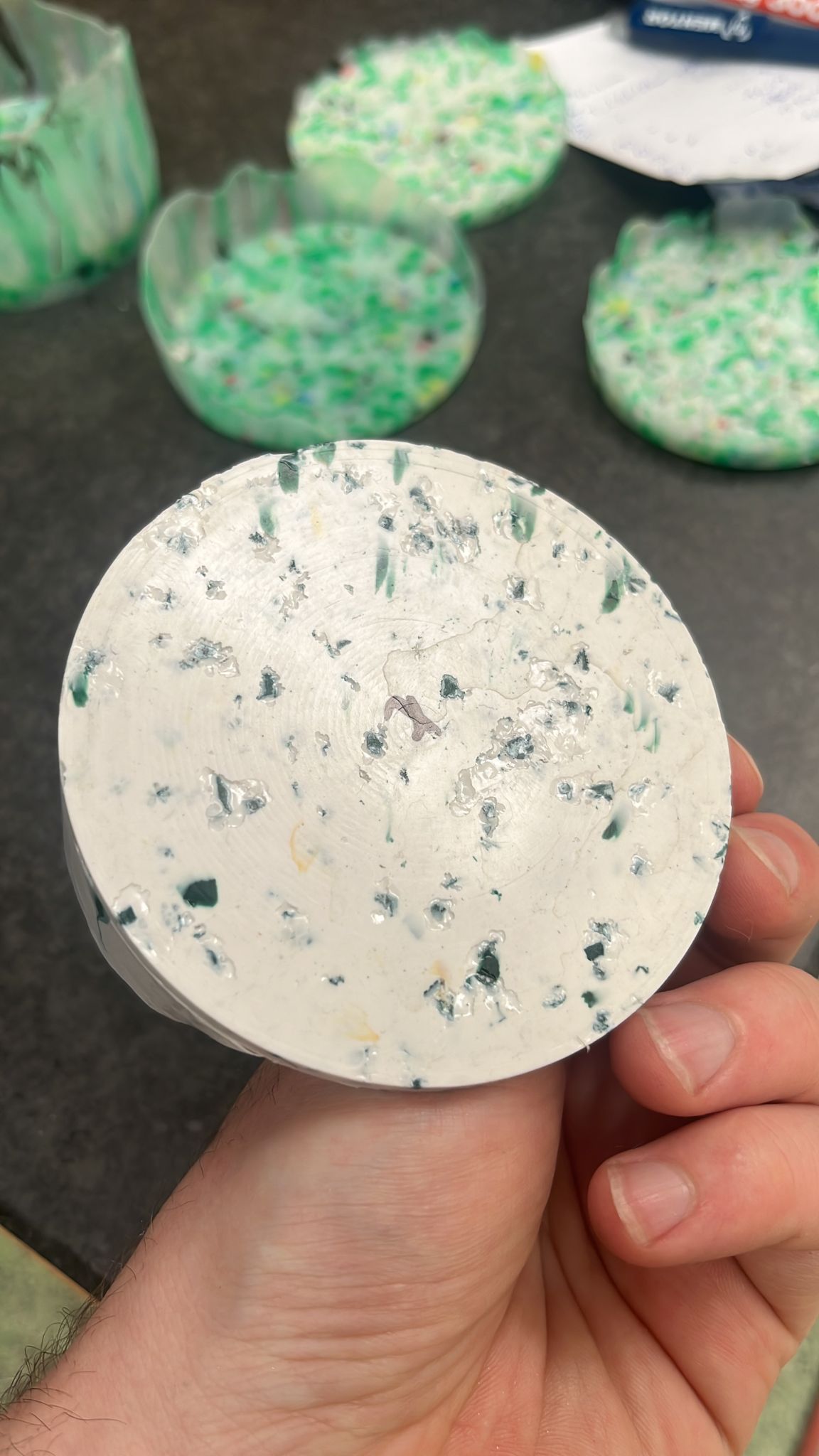
Compression Molding as a process
Created about 1 year ago
One main advantage of compression molding over other processes is the tolerance of the process regarding material impurities. While impurities in injection molding can destroy a machine, compression molding can still tolerate that.
A differentiation to injection molding from an aesthetic perspective is the (often) more static pattern in the product. While with plunger style injection molding machines the patterns of different colors are still visible, they always shape "flowing patterns" that follow the mold design. With compression molding these patterns can be reduced and are more dependent of the level of variation in height.
Another advantage is the possible reduced temperature range of the process.
The material is mostly not "molten" together, meaning to exceed the melt temperature and plastification the material in a liquid state.
More likely the material is "sintered" together, meaning to stay just below the melt temperature and only melt the outside zones of the granules.
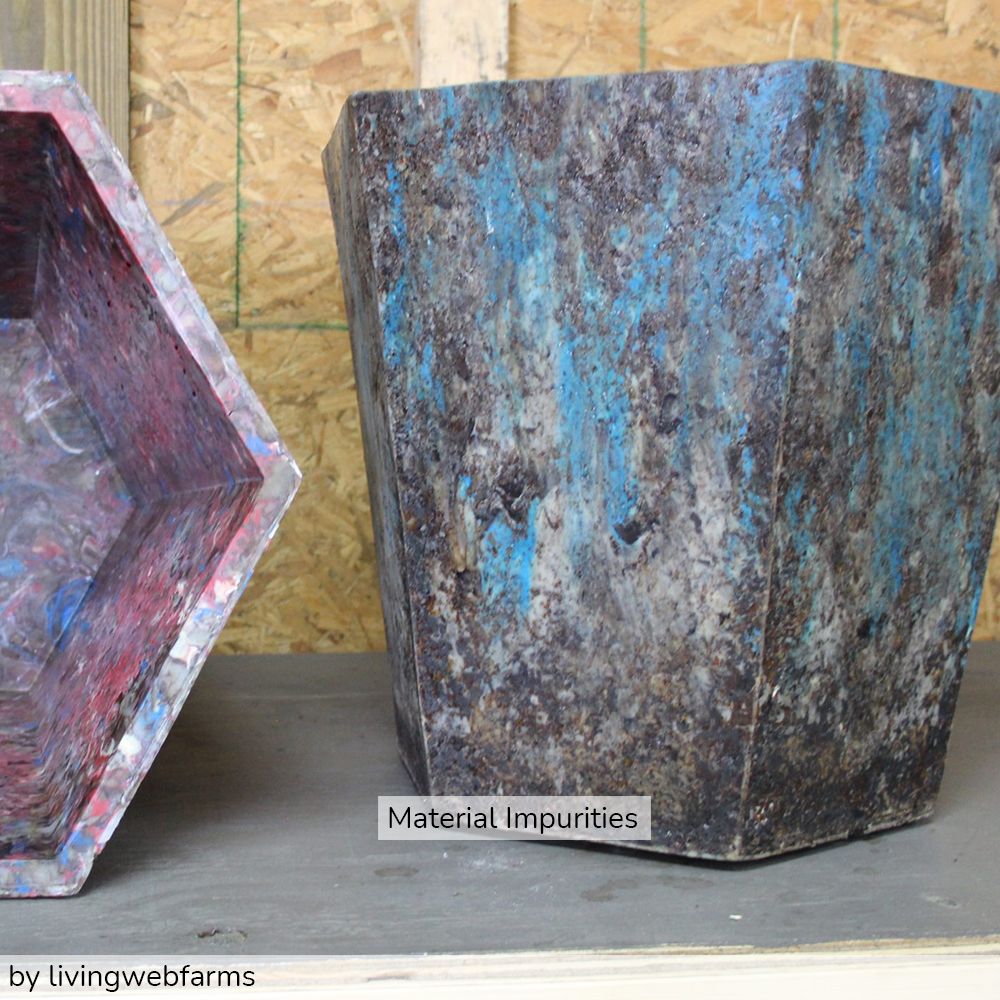
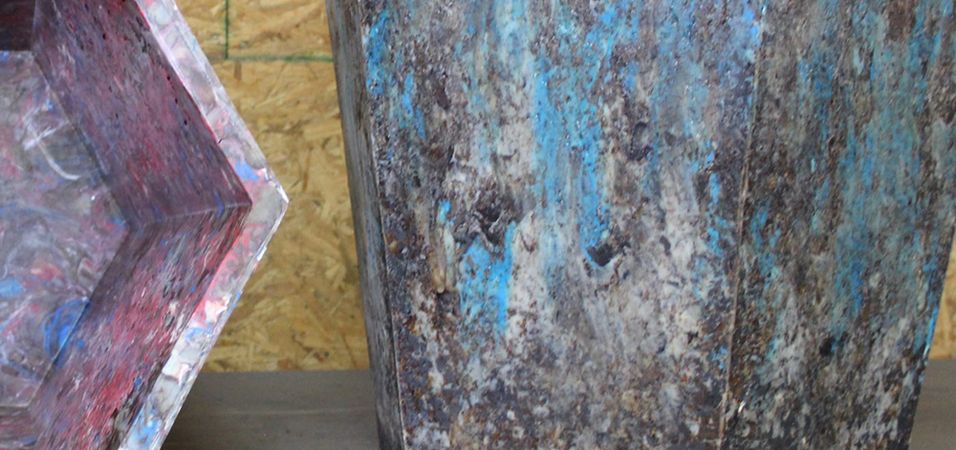
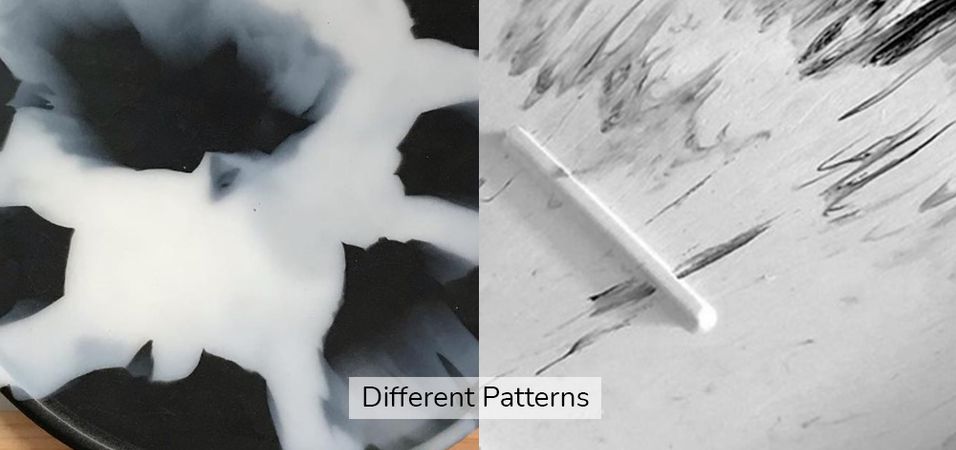
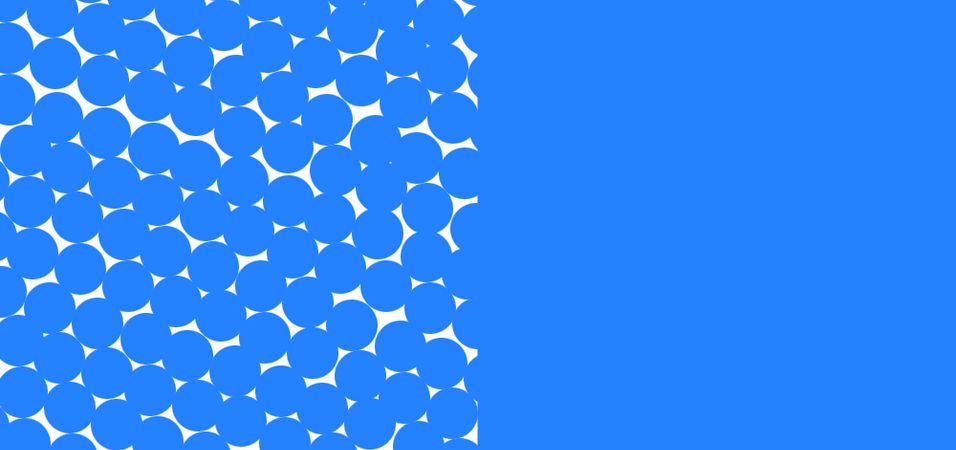
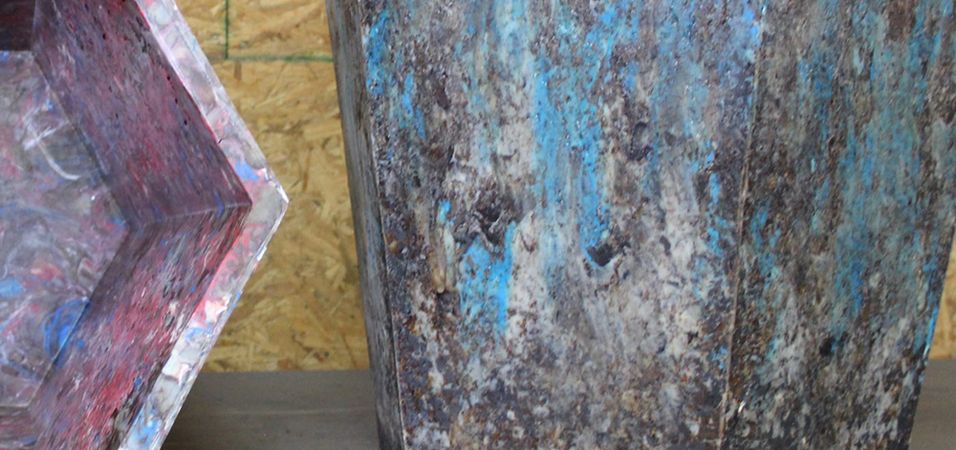
Production Applications / 1. Polymers and Bio Materials
Created about 1 year agoUpdated about 1 year ago
The area of compression molding with heat covers various fields.
We are looking at it from a machine perspective to give an idea of the versatility of the process and which applications it enables.
Here to name a few of them:
- Thermoforming of thermoplastic and thermoset materials
- Veneer pressing of wood laminate
- Vulcanization of rubber
- Processing of bio materials
- Composite materials
- Lamination of textiles
The following video demonstrates the compression molding of chairs at Mater
2. Wood Veneer Forming
Created about 1 year agoUpdated about 1 year ago
The video below demonstrates the lamination of wood veneer in a compression mould
3. Carbon Fiber Pressing
Created about 1 year agoUpdated about 1 year ago
In the video below a car wheel is manufactured out of carbon fiber
4. Textile
Created about 1 year agoUpdated about 1 year ago
The video below shows the production of luggage parts from PET fiber sheets
Machine Types
Created 12 months agoUpdated 9 months ago
As shown above there is a large variety of presses for specific applications.
Something to point out is that there are a lot of naming missmatches within the product range of presses. Mainly some name their products based on the target application e.g. veneer press (application) but it could be a column press (guide design) at the same time.
Below there are charts about different presses and how they fit our research goal to shape larger 3D objects.
Ideal Options:
- Lab presses
- Other, small heated presses like vulcanizing presses
- 2/4 Column presses
- Workshop presses (lightweight and easy available, but less rigid, no heating)
- Spotting presses (heavy but rigid, no heating)
Options with limited usability:
- C-Frame presses should only be considerered as option if they are already available (heavy for the application, design not suited for precise mold use)
- Exccentric presses mostly do not reach the required pressures and run too fast
- Veneer presses are not suited for smaller applications. There are smaller furniture presses tough that can be considered!
- Frame presses are usually very heavy, even in smaller sizes and hard to transport
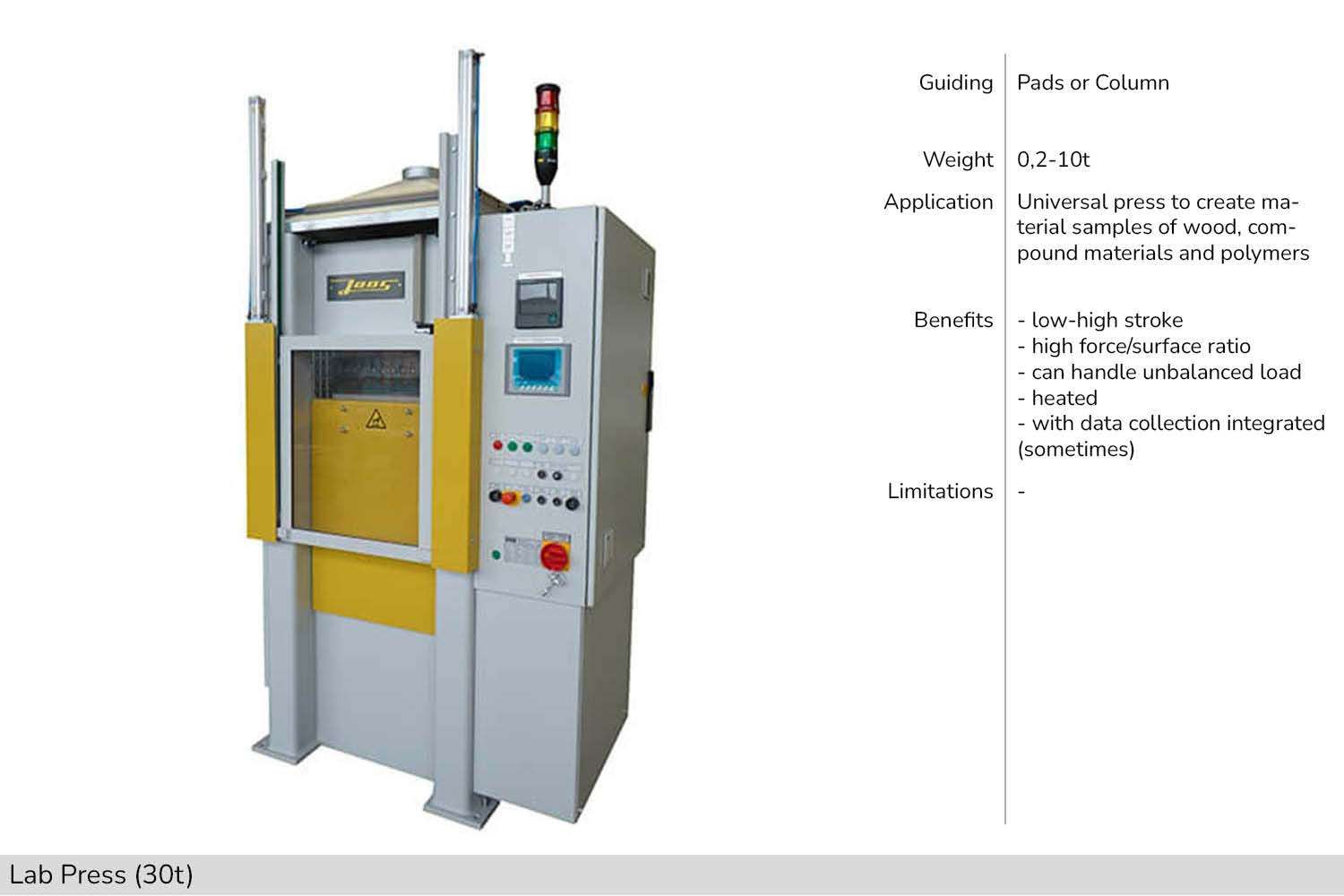
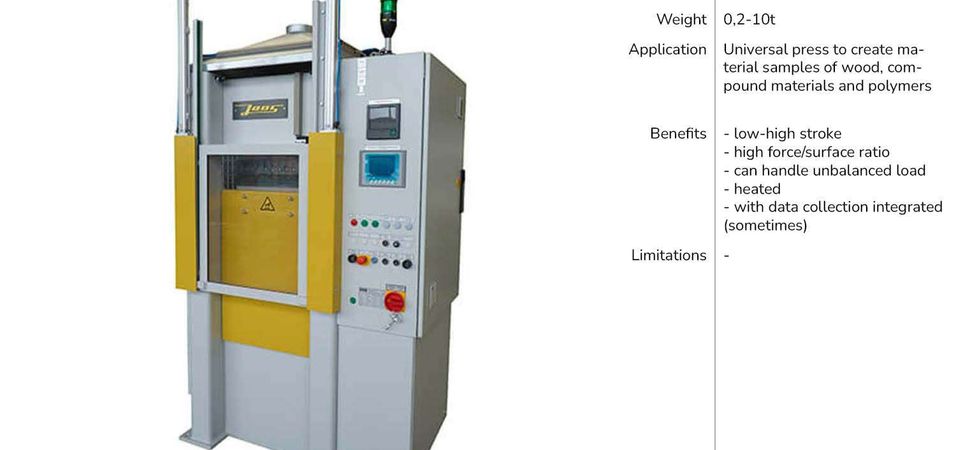
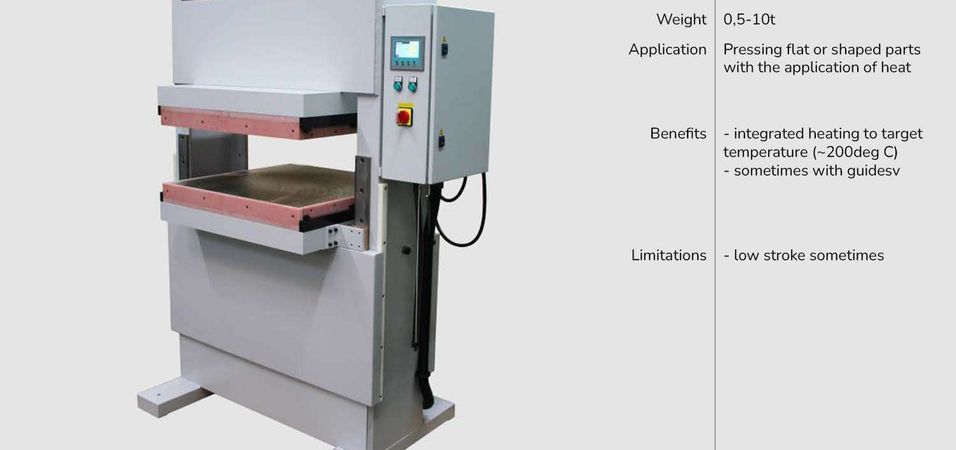
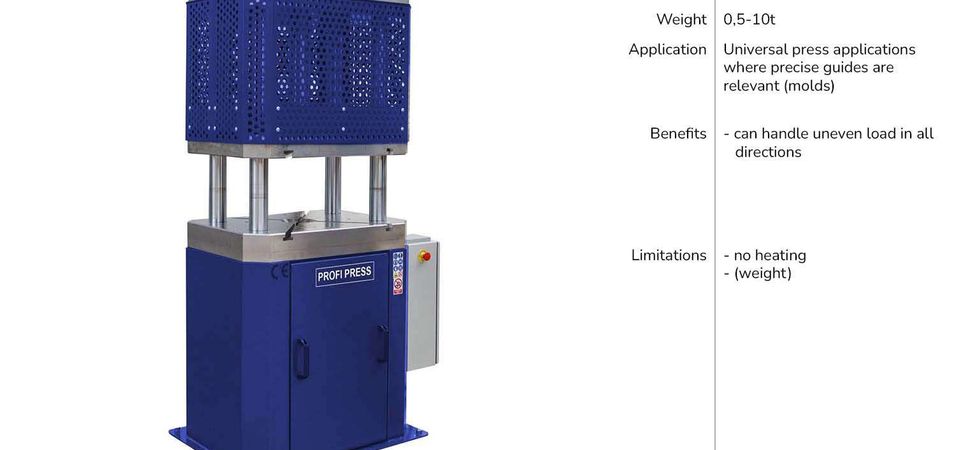
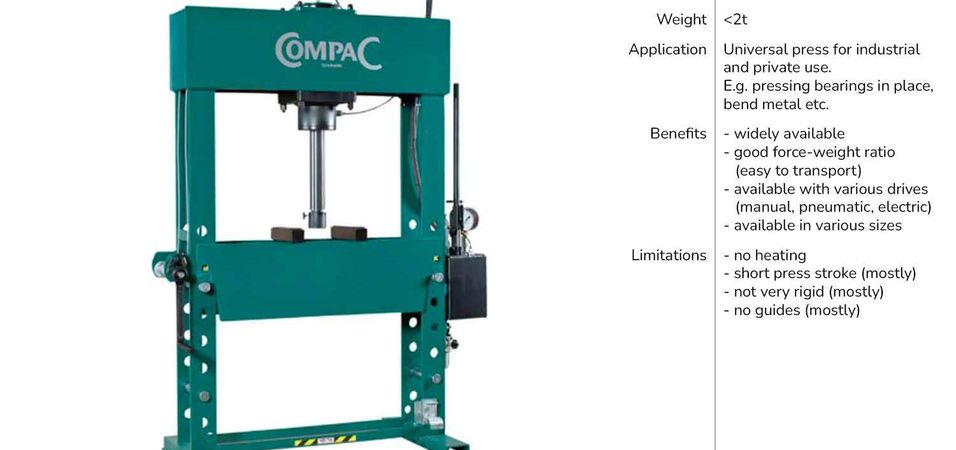
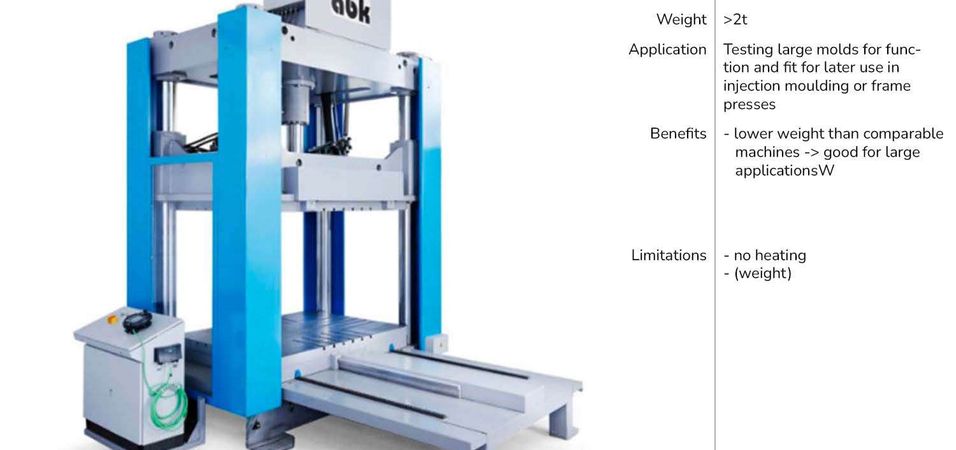
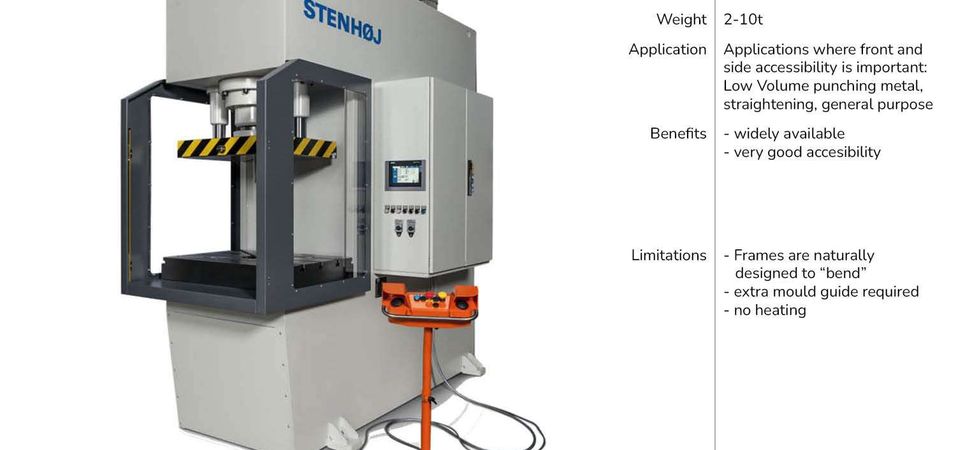
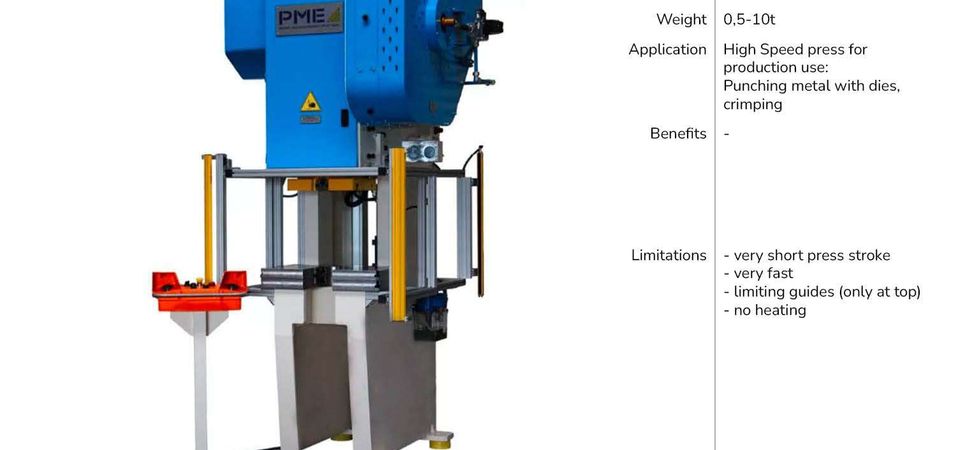
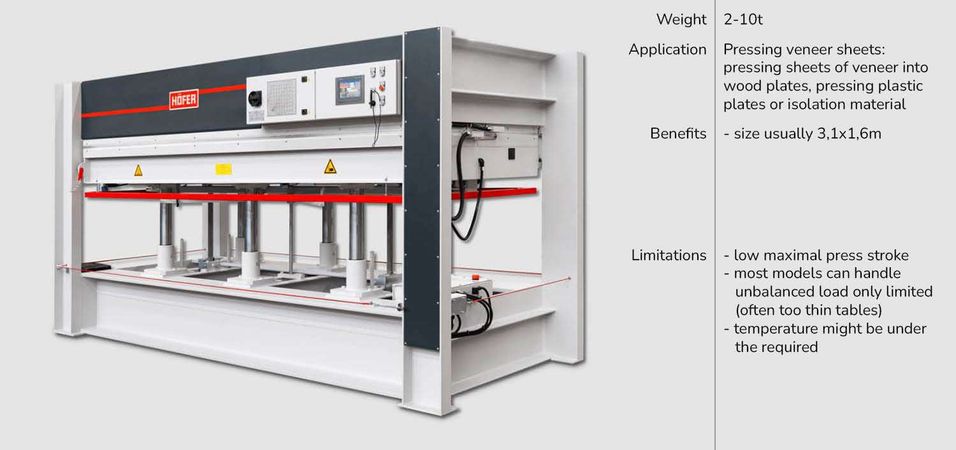
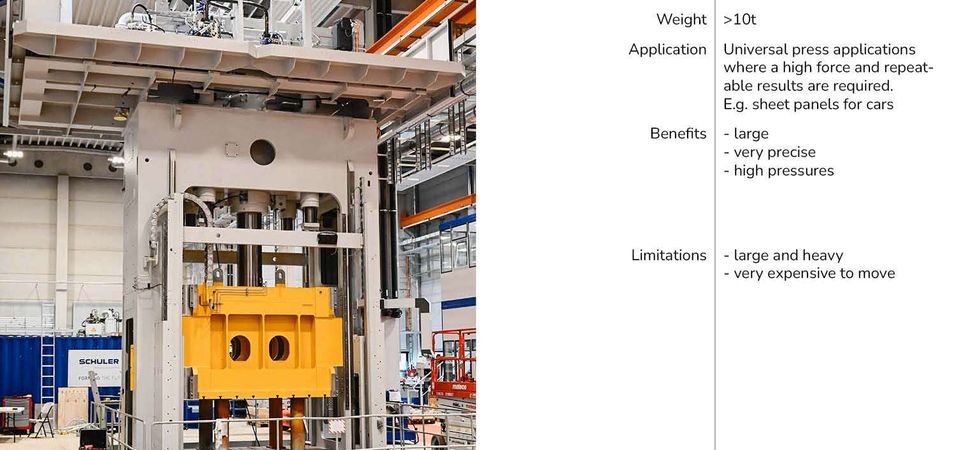
Review of a compression press build
Created 9 months agoUpdated 9 months ago
Last year I designed a compression press for one of my clients based on a standard workshop press on a limited budget.
The main design idea was based around:
- adding a heating system to a conventional workshop press
- converting the hydraulic piston into a single precision guide
The piston bushing was individually re-manufactured with a precision bushing from out of brass
I give a review to myself here and talk about the difficulties of this design:
Advantages:
- Cheap to get started with an available press
- Guide system works well (if the moulds are filled evenly)
- Heat decoupling with PTFE plates and wood worked very good
Learnings:
- Component quality of the standard import workshop presses are poor
- Stroke length is very relevant to have enough clearance to fill the moulds easily and switch between moulds. That enables to manually handling of hot / heavy moulds. This is a strong point against these readymade presses.
- The machine lower base where the moulds are placed are not fixed to the frame which makes guide and general usability difficult
The images show the process of the conversion below. A set of moulds was produced inhouse as well to go along with the machine.
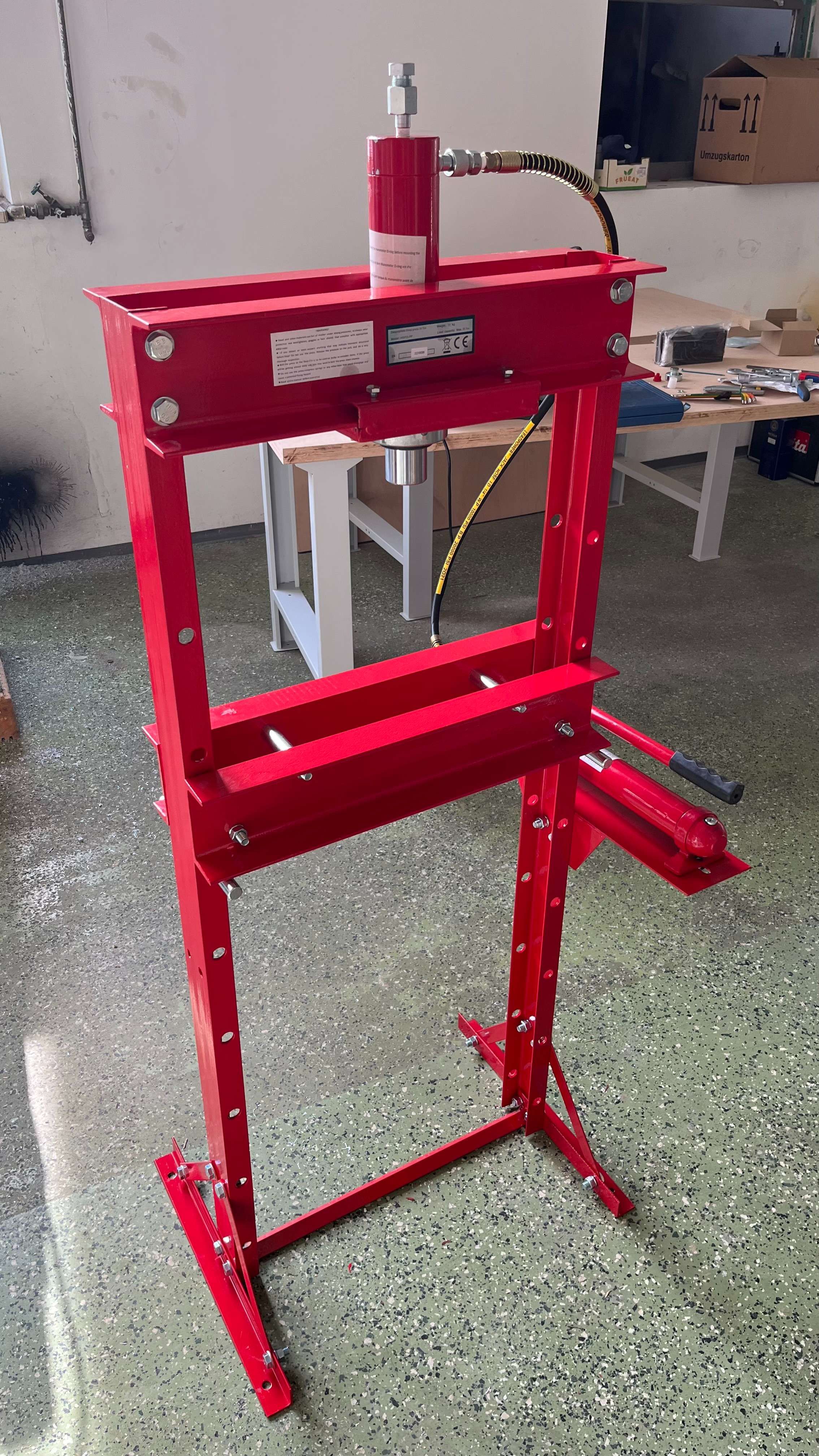
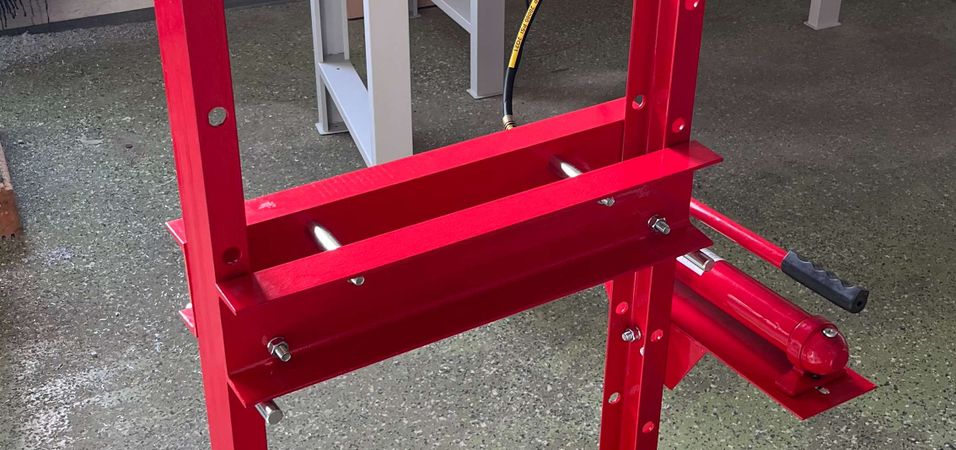
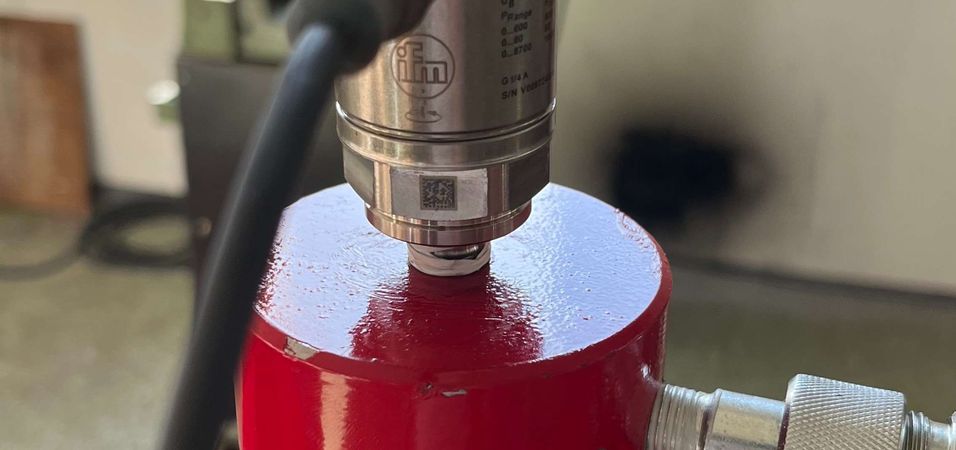
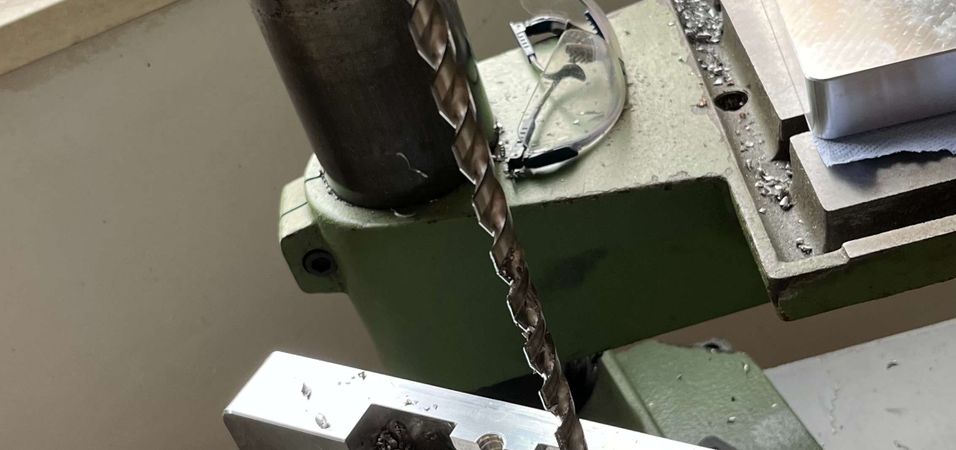
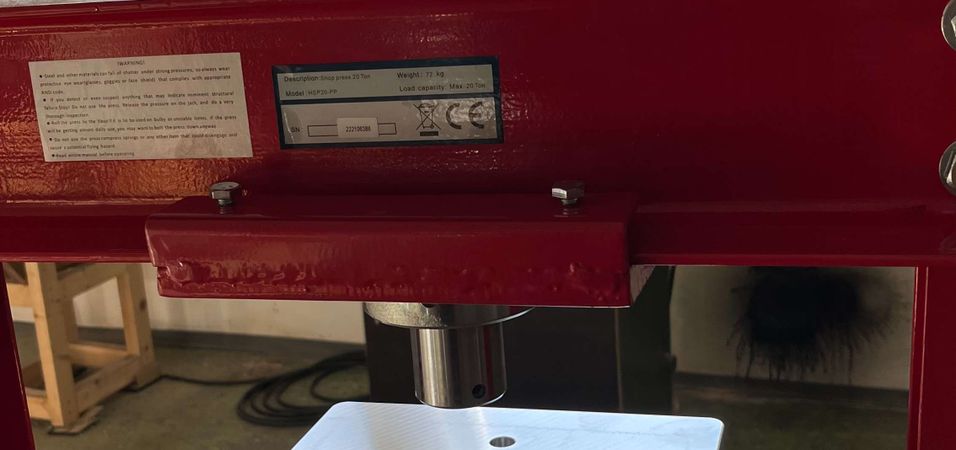
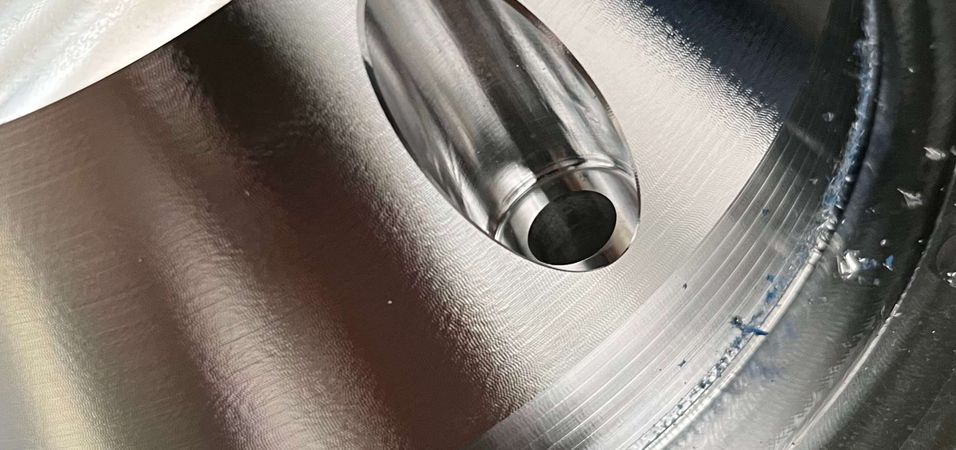
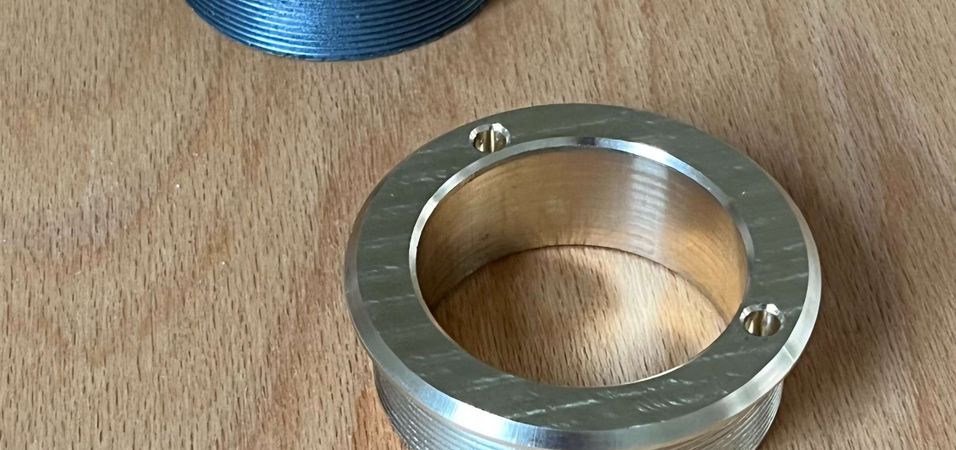
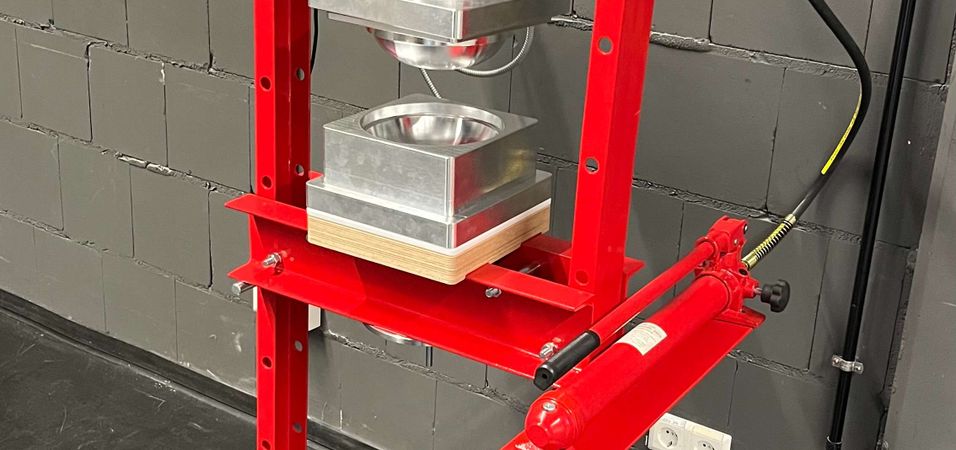
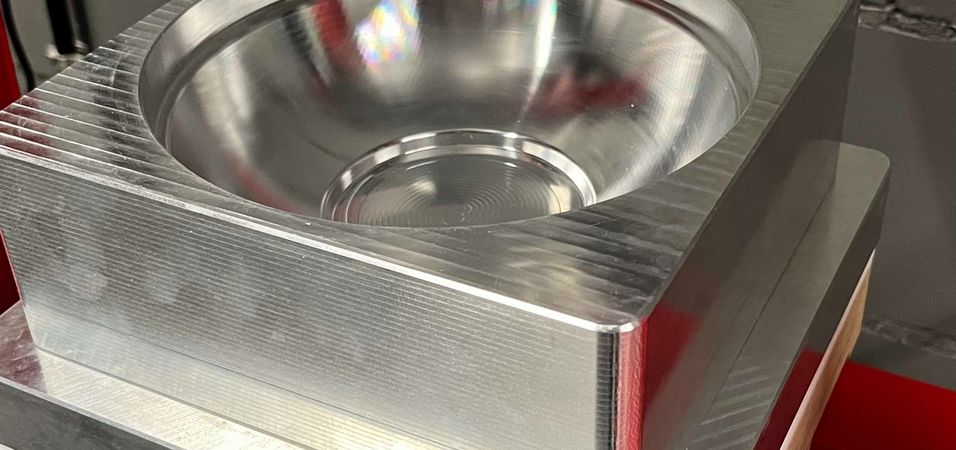
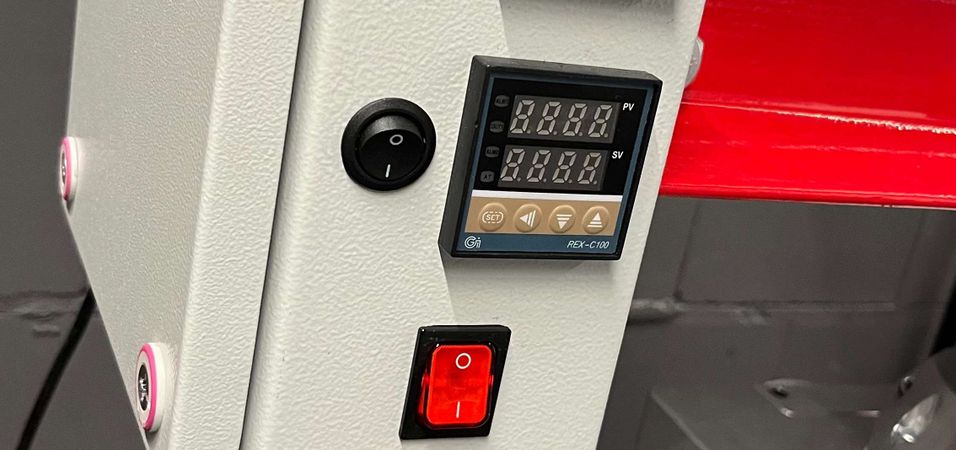
Review of the BioPress during the v4 development
Created 9 months ago
During the development of the Precious Plastic v4 machines Jannis Kempkens designed the initial Bio Press in the Beyond Plastic project https://community.preciousplastic.com/academy/research/beyondplastic
To keep the overview complete with past designs in the community here a review about it
Advantages:
- Very User friendly, so the moulds can slide out to the side and be filled/ parts extracted outside the machine. This is similar to some spotting presses on the market
- Product like look of the machine due to the paneling
Learnings:
- Missing guides and instable piston can lead to jams of the moulds
- Large number of parts for the structural parts of the press ( time consuming manufacturing)
DIY or Buy (Used) ?
Created 8 months ago
During our research it became clear quickly that hydraulic components above the basic 30t hand driven hydraulic workshop presses are very costly if you want to go for parts with reliable properties and datasheets.
Here is an overview of the main components that set the price for a 50t heat press with 12kW heating power
- Hydraulic Piston ~550€ ( https://www.ez-tools.de/products/doppeltwirkender-hydraulikzylinder-50-ton-300-mm-mit-kragengewinde_yg-50300sct )
- Hydraulic Pump ~1100€ ( https://www.ez-tools.de/products/doppeltwirkende-hydraulikpumpe-mit-magnetventil-70?_pos=5&_sid=d9382381c&_ss=r )
- Steel and welding ~2500€
- Other electronics ~500€
- Heat Inserts ~300€
Total ~5000€, without the labour of assembly and engineering
These were fairly inexpensive suppliers, with more “regular” suppliers its easy to 4x these prices.
Together with my previous experience that you have to build three prototypes for an average machine to have something practical I decided against the plan to build a machine from the ground up.
Instead I will reverse engineer an existing system, look at its features and issues and create a buying/ building guildeline for a press that can be adjusted to the need of the production.
For that I found a press from a known press building company with less than 200h operating time at a Siemens plant from the year 1985 for a less then the estimated steel+welding. Getting it transported tough was a bit of a fun undertaking. Lets say always check the weight before buying a press.
Specifications:
Max Pressure 60t
Pressure/mm² 6,66N/mm²
Plate Size 300x300mm
Levels 2
Clearance vertical 2x150 or 1x330mm
Max Temperature 190°
Heating 12,5kW
Piston Dia 150mm
Weight 1,25t
While everything was operating from the first second, there are some things to check and replace to make a safe operation possible. That will be the next update which parts were replaced and checked for safety.
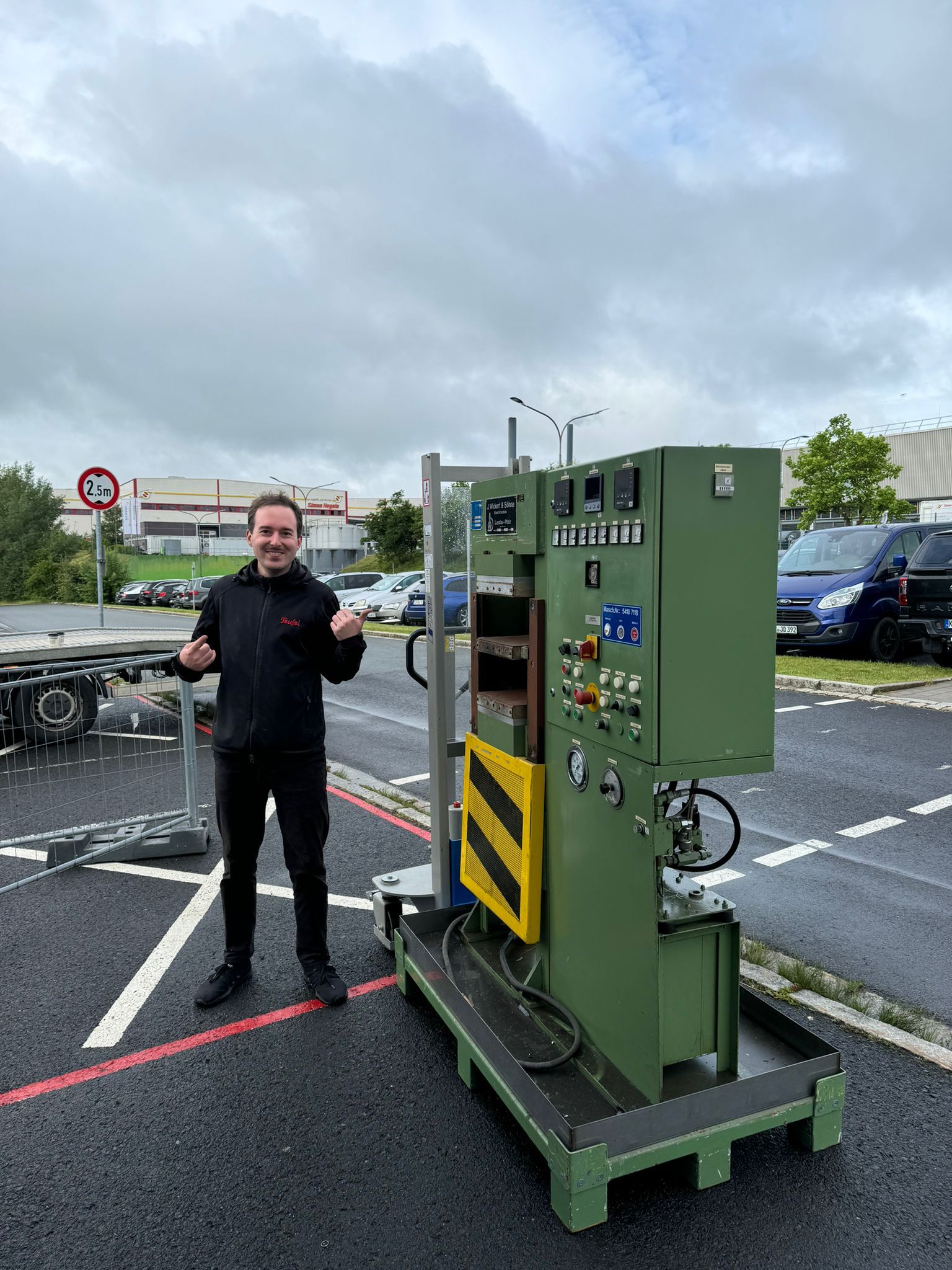
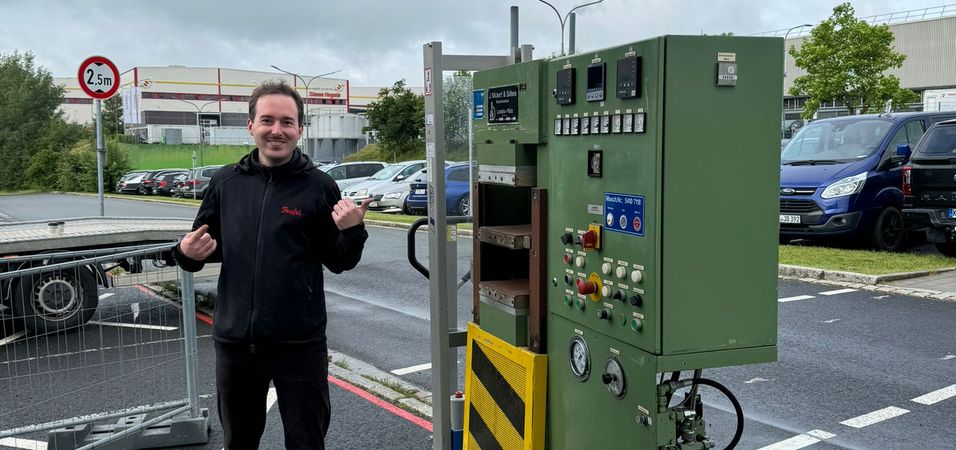
Machine renovation
Created 8 months agoUpdated about 2 months ago
As mentioned in the last post the machine needed some things checked in order to perform the upcoming tests reliable and save.
My main concern was that the electrical connections may have corroded, and while still intact they might break loose during operation. The hydraulic pipes looked all very good and likelywise have been replaced since the machine has been built in 1985.
In the pictures attached there is the process documented of what it looked like and what it beacme.
Changes:
- general cleaning
- replaced all the wiring at the heat plates
- added Teflon insulation to the ceramic cartridge heaters
- removed the main rust from the press area
- measured the resistance of the PE contact to all the heatplates <1Ohm
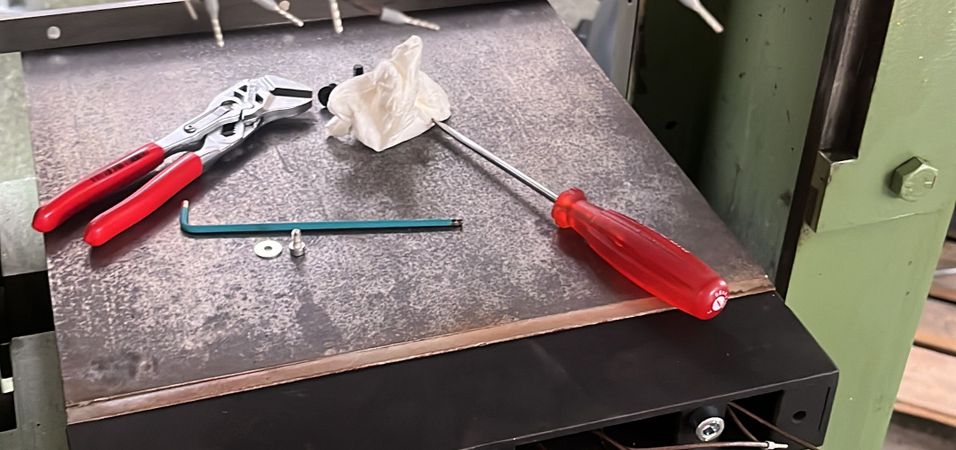
3D Rework of the machine frame
Created about 2 months agoUpdated about 2 months ago
In order to make it replicable for people here is a quick 3D model of the machine itself. This is not supposed to be a manual how to build this machine, but I assume that anyone who approaches a project like this has the skillset to puzzle together the bits and pieces.
It is supposed to be a reference that you don't need to do all the force simulation and machine layout by yourself or that you have a reference to look out for if you get one.
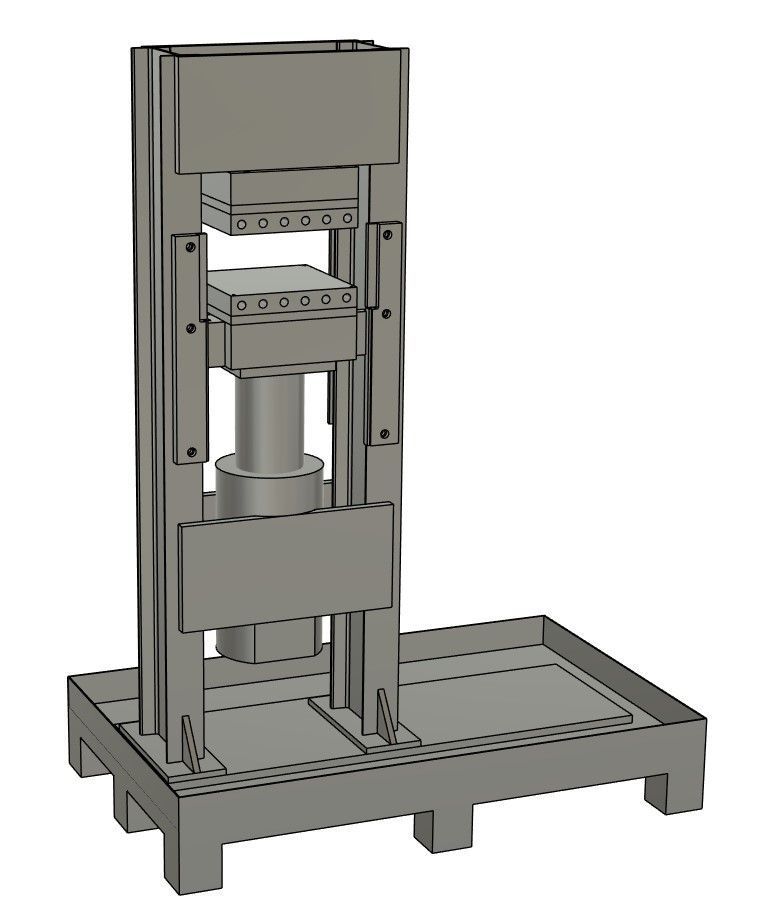
Material Bulk Density
Created 27 days agoUpdated 27 days ago
The material desnity (g/cm³) defines the pre-compression zone of the mould and is a very important consideration already in the design process of the part. This means that you need to know your material density before you start the mould design. However most materials are in a certain range and there are granule types that are just not useful for the process.
Usually you cannot influence the material density (specifc weight of a material) itself, but you can influence the size of the granules in the pre-process - so called “bulk density”. E.g. a solid rock has 100% bulk density vs. gravels of the same volume might just have 50% bulk density vs. sand of the same volume that might have 95% bulk density.
Depending on the material there are various raw states with different bulk densities e.g.: PET can come as a solid block (heavy, usually not a state for direct processing), granules (relatively heavy), regrind (depending on the shred size medium-light weight), as granule (ligther than granules usually), as farbric regrinds (very light).
Example: A less dense material (e.g. Nr. 10 - 100% fishing nets) would need a way larger mould to fill in the material before the compression process than a high dense material (e.g. Nr. 1 Pelletized Granulate)
The tests were conducted by filling a 1L container with various recycled plastic.
The general result here is that as more dense a material is the better as it results in:
- needs less pre-compression zone in the mould
- better heat transfer between the granules
Try to avoid following materials as they have usually a very high Matieral Density to Granule Ratio
- fabrics
- CNC chips
- 3d print waste
However mixing these materials with higher density materials such as granulate or shredded solids or flakes is possible.
Also it can be possible to pre-process (e.g. heating in oven or extruding) these materials, either for visual modifications or enhancing its density.
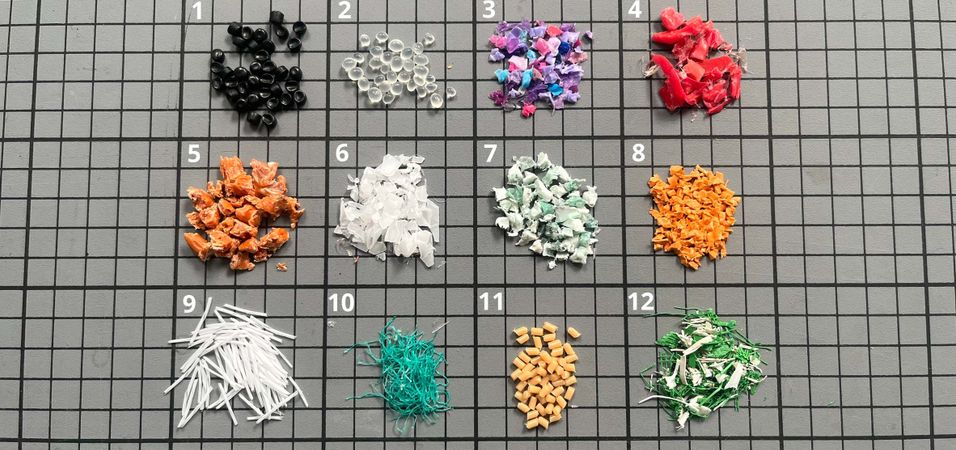
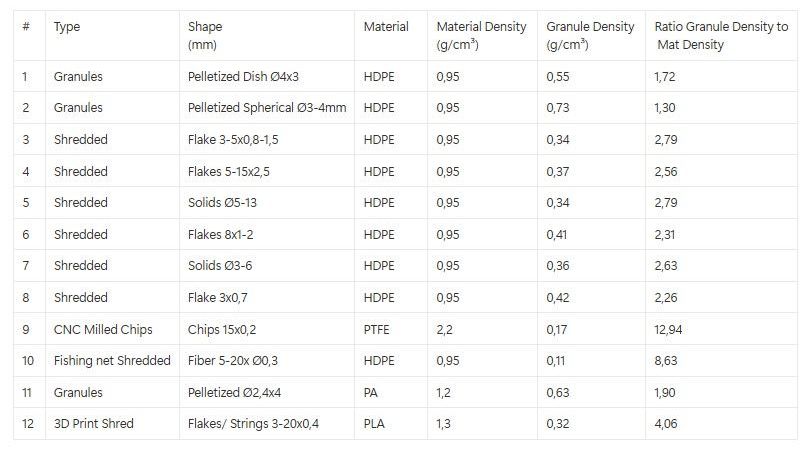
Made by
easymoulds