Completed
preciousplasticbeta
Clean plastic more efficiently?
Currently plastic is often washed by hand at precious plastic groups. We want to see if we can develop some machine or process that makes cleaning plastic less manual and more consistent. Make sure to also check this How-to on a Low cost Washing Machine with water filter system https://community.preciousplastic.com/how-to/low-cost-washing-machine-with-water-filter-systemMore Information
An introduction
Created about 4 years agoUpdated about 4 years ago
๐ Why?
The download kit of precious plastic currently provides solutions for sorting plastic, shredding plastic, and making new items from plastic. The input of this process needs to be clean plastic. if this is not the case, the machines can break or the items from recycled plastic do not live up to the expectations.
The plastic that enters the recycling process is often not clean (enough) to recycle. Cleaning a few shampoo bottles is no problem, but cleaning large amounts of plastic with food stains is not pleasant by hand.
๐ Current solutions
From a quick round in the community people shared their typical way of cleaning plastic:
- By hand, and letting the plastic dwell in warm or soapy water
- With a pressure washer, blastic the dirt of in a closed container
- With a washing machine, placing plastic in a bag and letting it run for a full cycle.
๐ Research in the past
During the development of v3 and v4 already quite some people researched if washing could be simpler
Topic by Matthijs: https://davehakkens.nl/community/forums/topic/washing-plastic/
Topic by Louis & Paul: https://davehakkens.nl/community/forums/topic/washing-plastic-v4/
Topic by Rory https://community.preciousplastic.com/how-to/wash-plastic-washing-machine
๐ The goal
For this research project, we settled on the goal of cleaning 150kg of plastic per week with a budget of a 1500 euro machine. We mainly want to do PE, PP, PET, and PS
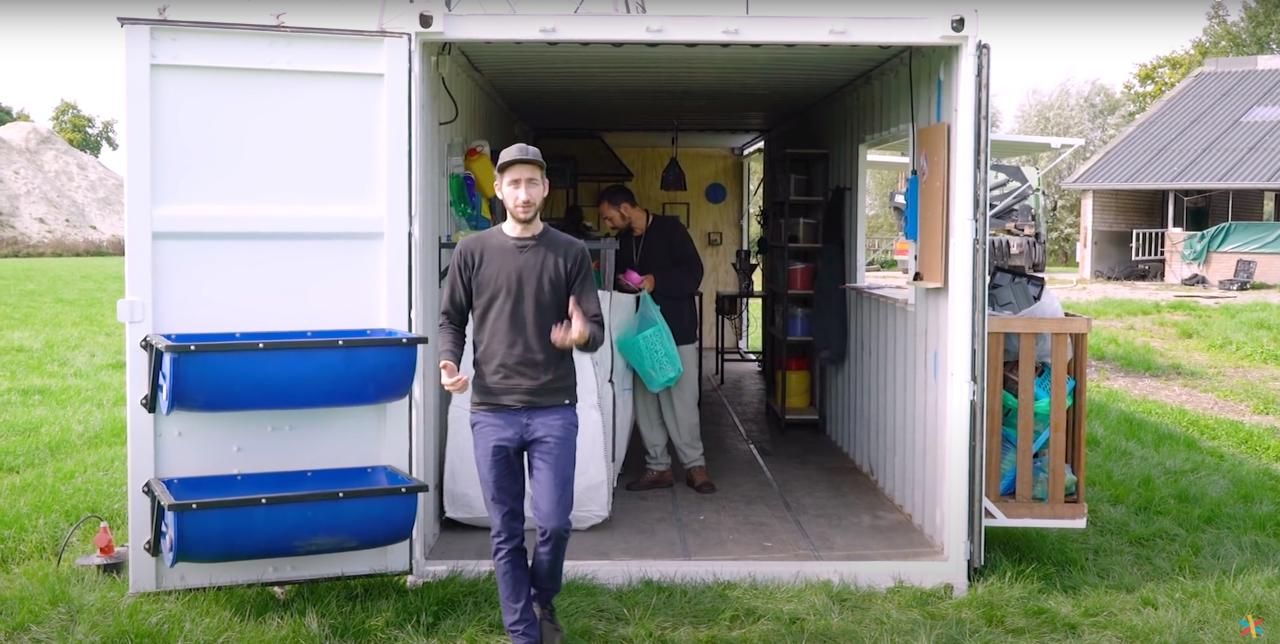
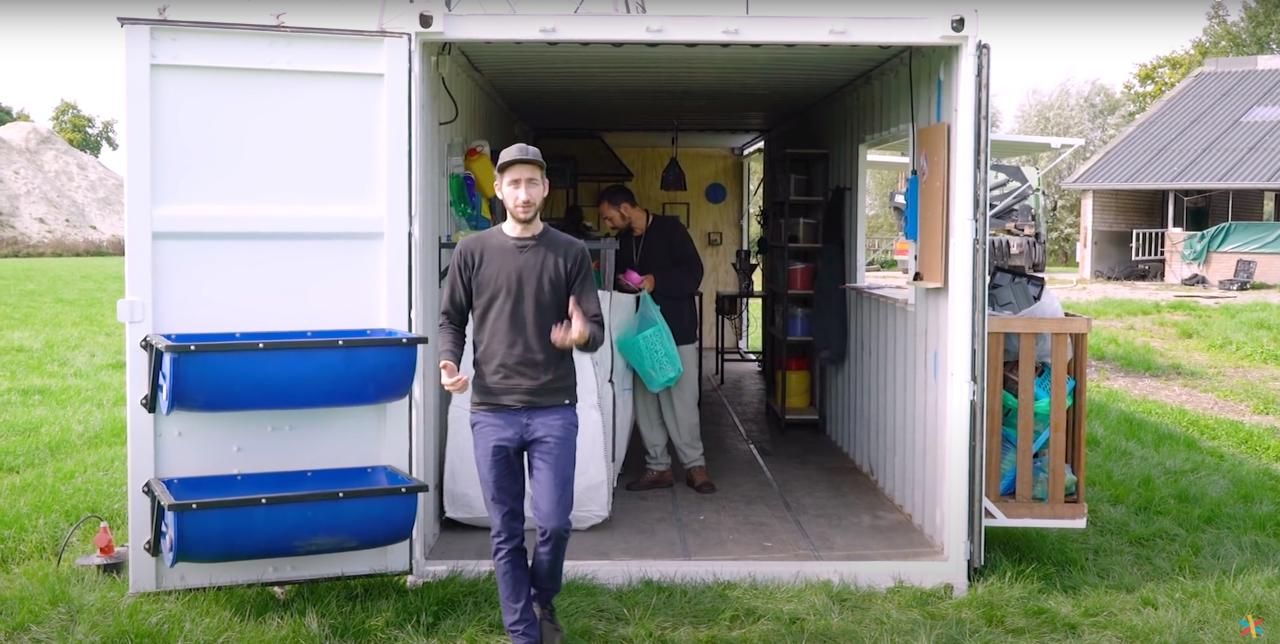
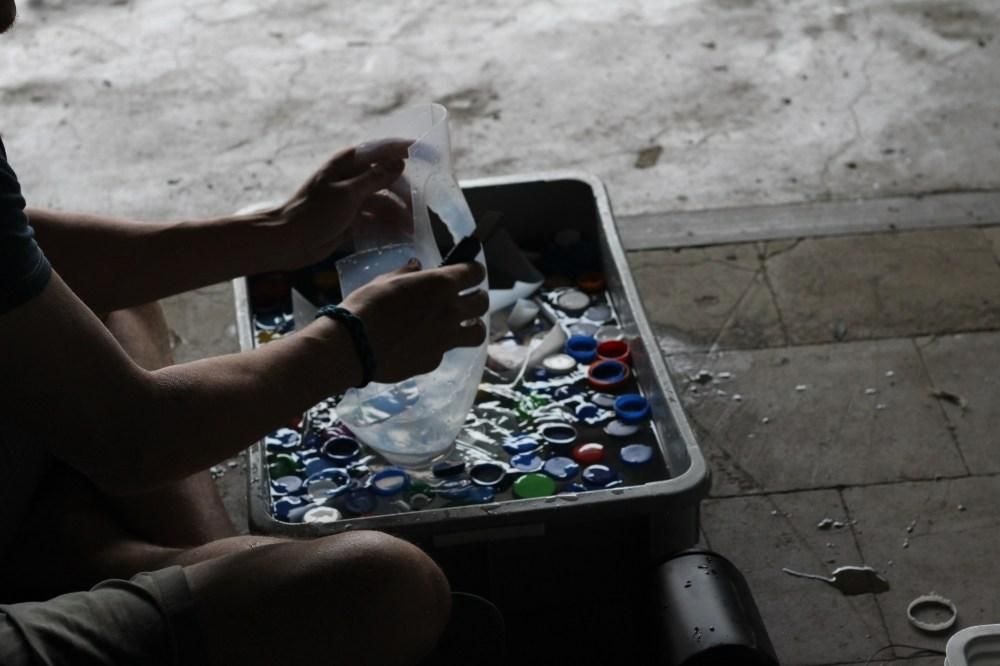
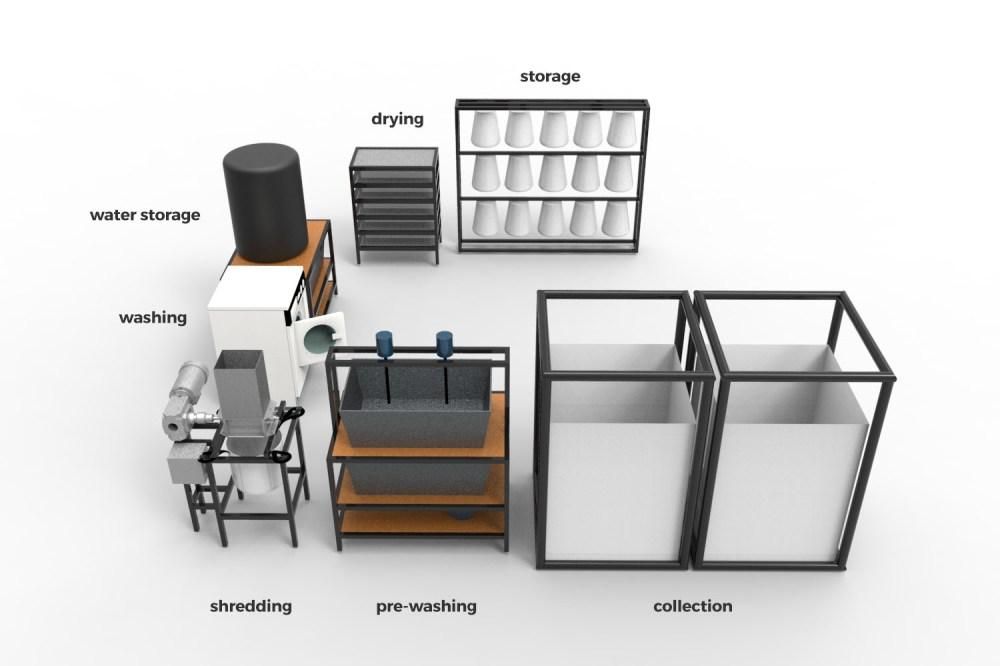
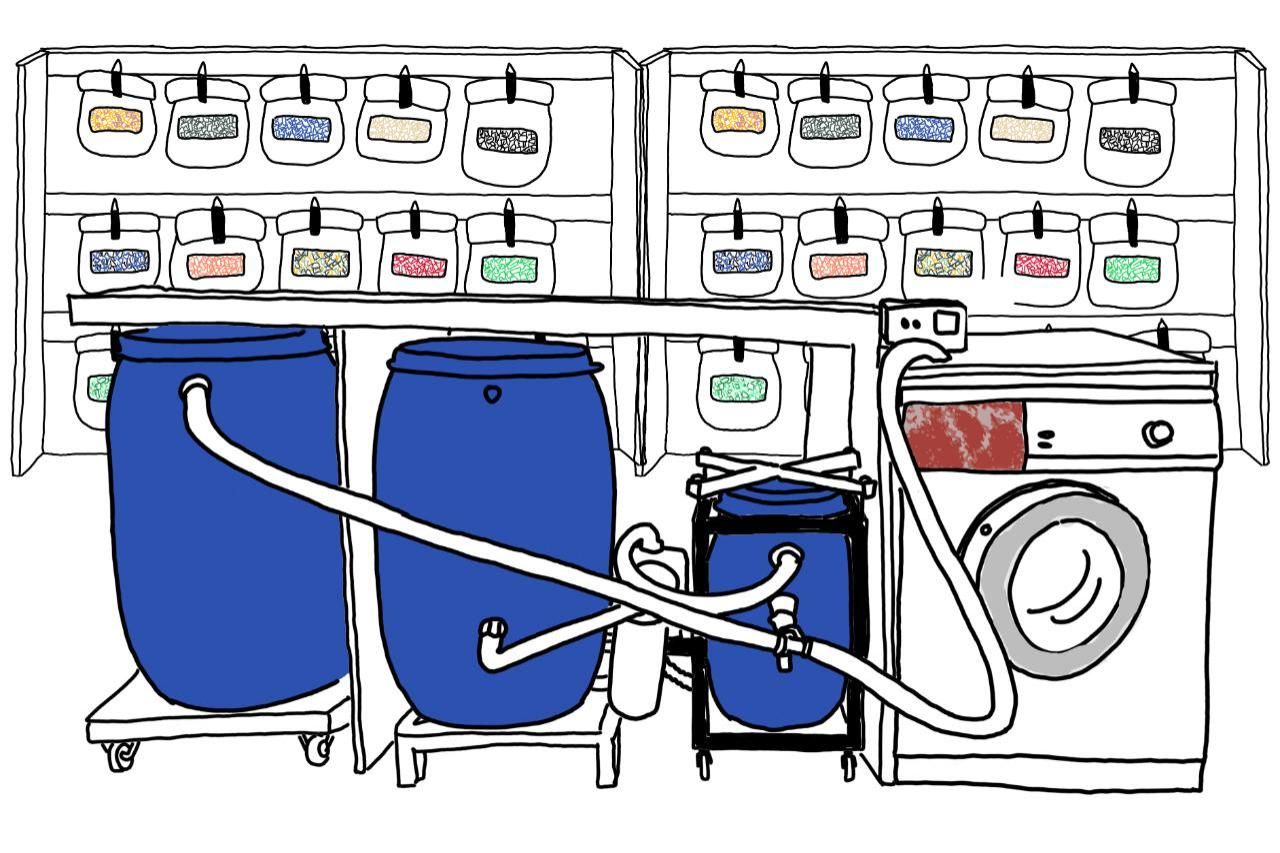
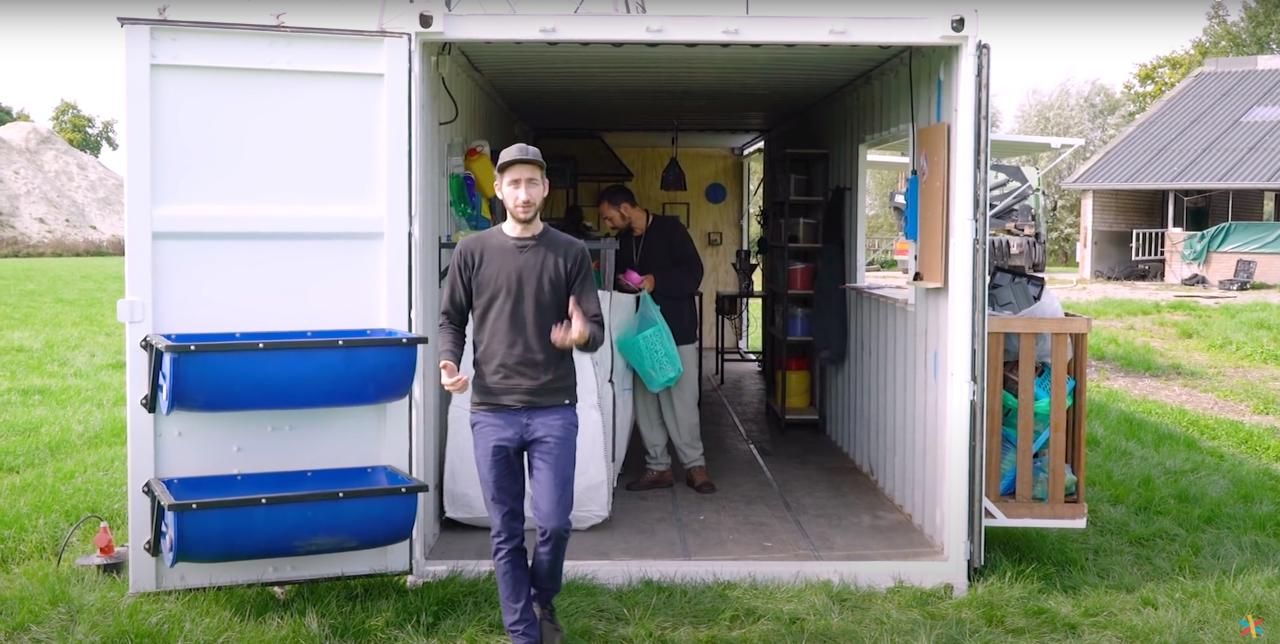
Places for inspiration
Created about 4 years agoUpdated about 4 years ago
We started our research looking for common solutions for cleaning materials, not only plastic, but also clothes, medical equipmen,t and even how the human body cleans itself.
We found some low-tech solutions like the bike washing machine in the first picture
We found some mid-tech solutions like a washing machine or dishwasher in the second picture
and some interesting high-tech solutions like ultrasonic cleaning as can be seen in the third picture
these different cleaning methods gave us a whole bunch of inspiration for potential plastic cleaners. Stay tuned for funky ideas ๐
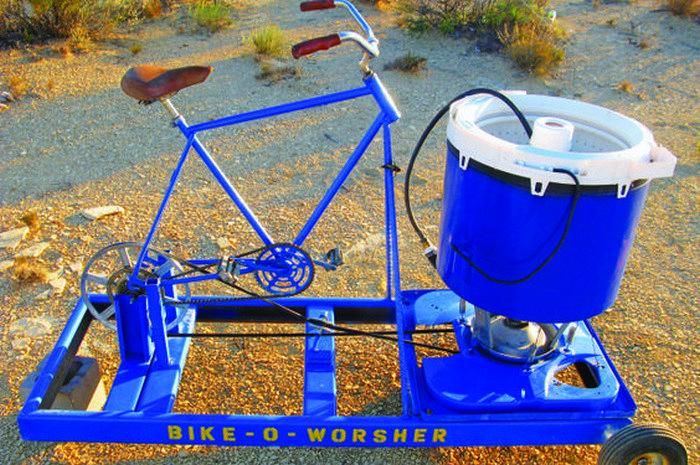
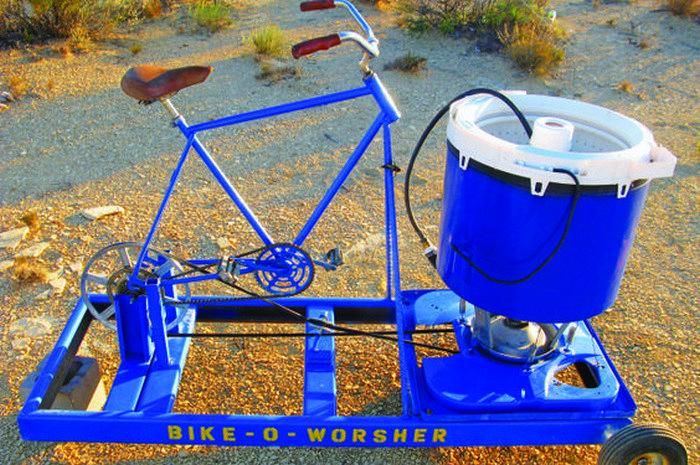
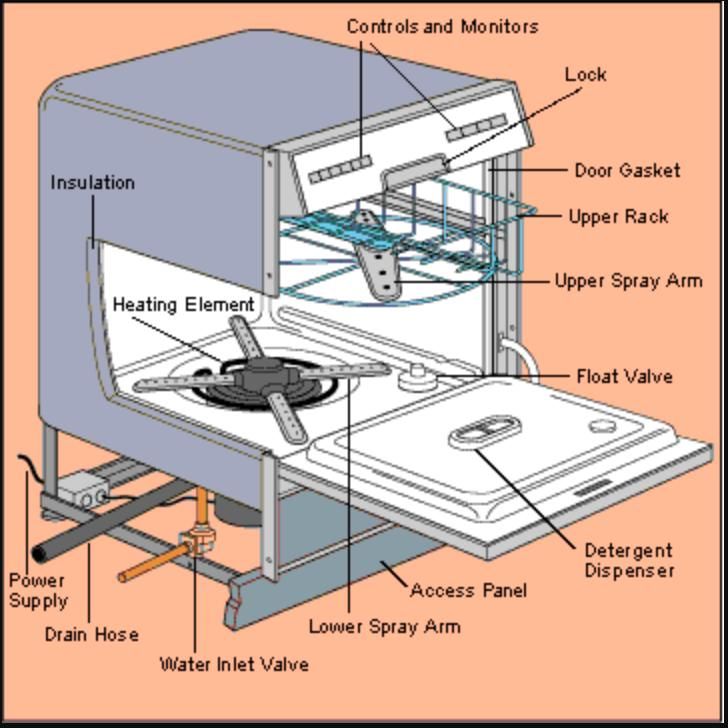

cleaning shredded or unshredded plastic
Created about 4 years agoUpdated about 4 years ago
Quite quickly we found that the properties of the material have a big influence on the cleaning system.
The first question we wanted to answer was whether we want to clean shredded or unshredded plastic.
Why clean shredded plastic๐ฉ
- The plastic has a uniform size
- No closed areas where the water cant reach
- More surface area makes drying easy
Why clean unshredded plastic ๐งผ
- The shredder shreds clean plastic
- No small particles in the washing system
In the end we chose to clean shredded plastic, this has the added benefit that we can use best practices from the industry since this seems to be the way the industry has done it for years.
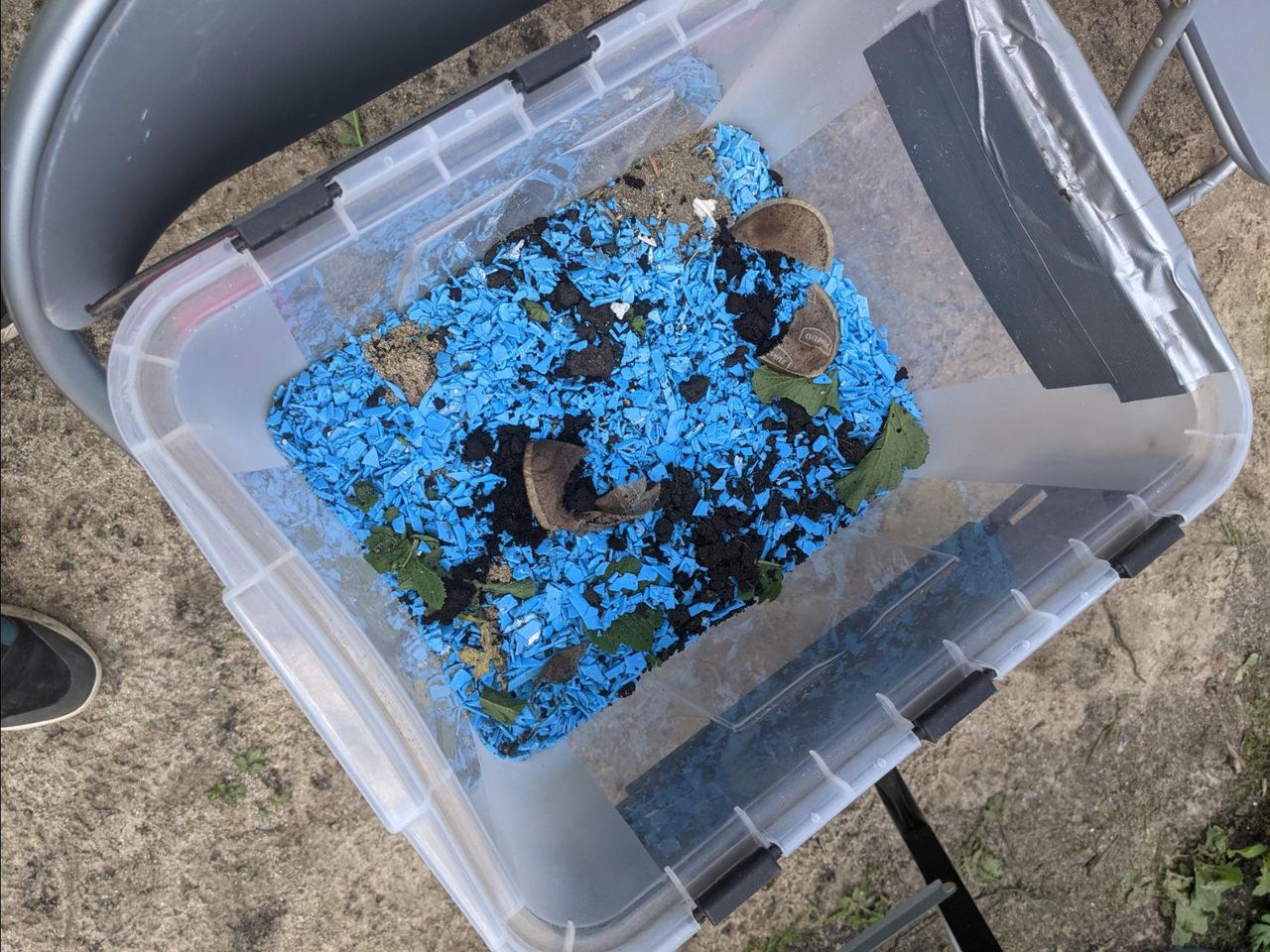
Concepts
Created about 4 years agoUpdated about 4 years ago
Based on the inspiration shared in an earlier post we started working on different concepts that could wash the plastic.
The concepts ranged from a big salad maker to a frying pan and back to stackable boxes.
we found that the following workflow made the most sense:
1. Sorting the plastic on type
2. Cutting big pieces so they fit the shredder basic
3. Remove big contaminants like food or rocks
4. Shred the plastic
5. Place plastic in the washing system
6. Let the system run
7. take plastic to the drying system
8. dry the plastic
9. store the plastic
Based on a scoring system we were left with two concepts
the overflow concept and the barrel concept
The overflow concept is based on three water containers overflowing from one into the other. In the first tank water is added with a pressure washer, the floating plastic overflows into the second tank where it is left to dwell, in the last tank there is room for sediment to settle to the bottom. After the plastic has gone through these tanks it can be captured in mesh bags and left to dry passively.
The barrel concept houses the plastic in one barrel throughout the whole process. First, the barrel is filled with plastic, in the second stage the plastic is cleaned with a pressure washer and in the last stage the water is removed and the plastic is dried.
The overflow system is on the left and the barrel system is on the right
We made the final decision to continue with the Barrel concept, this will now be our main focus!
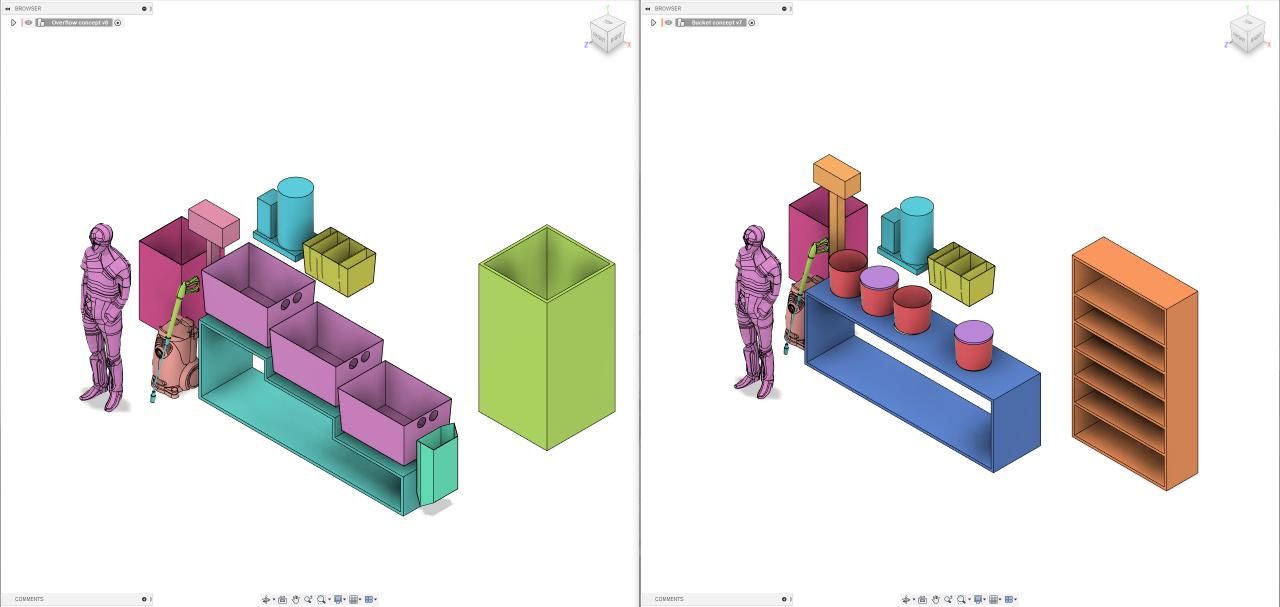
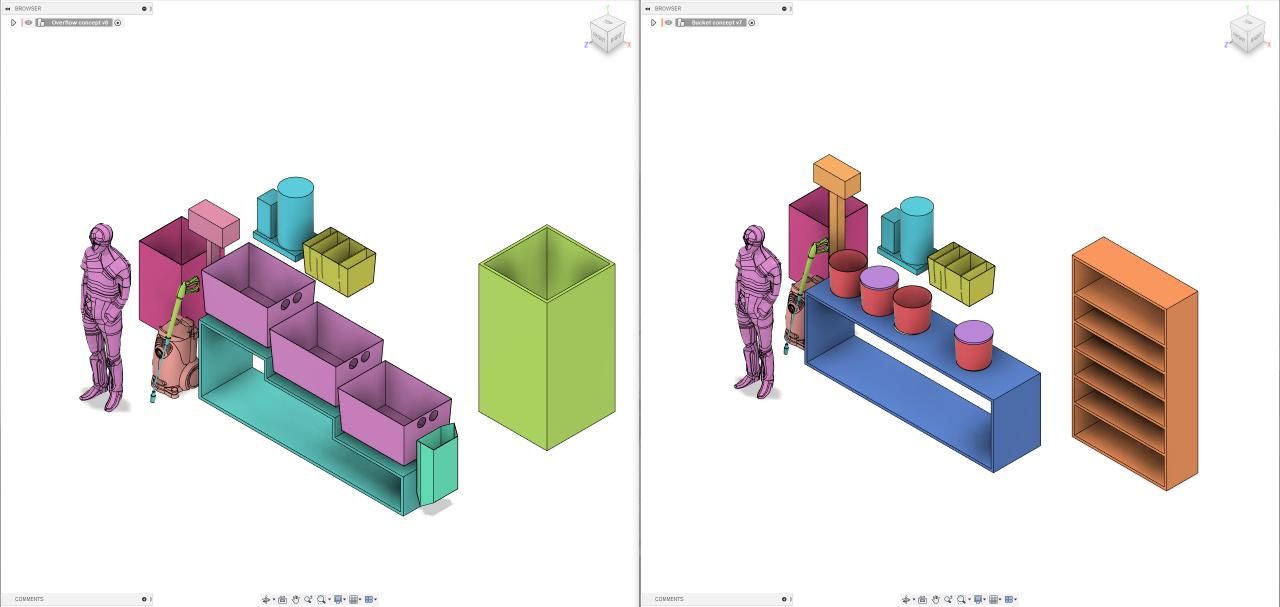
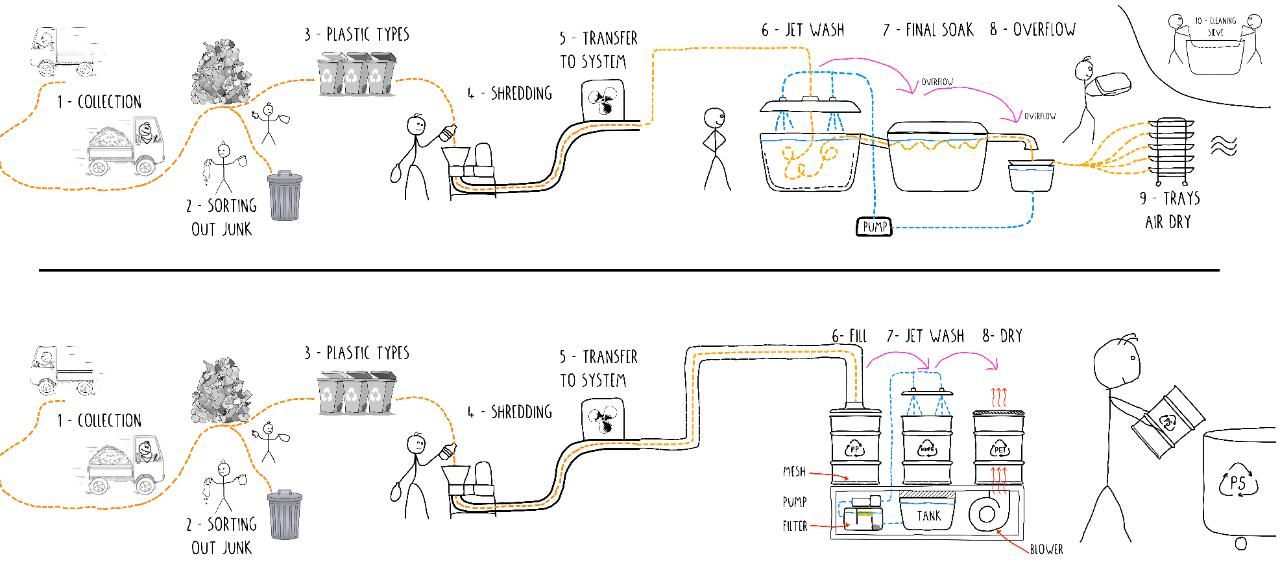
Nozzles
Created about 4 years agoUpdated about 4 years ago
From past experience, we know that agitating the plastic with a pressure washer works well.
Within the field of pressure washers there is a large degree of different nozzle's
Most common online are the two following:
5 - pack Quick connect nozzles (first picture) https://www.amazon.com/Twinkle-Star-Pressure-Multiple-Degrees/dp/B06XSHM8WB/ref=sr_1_3
1/4'' nozzles (second picture) https://www.amazon.com/Tool-Daily-Pressure-Replacement-Undercarriage/dp/B0813DY3R9/ref=pd_di_sccai_1/145-8384516-6970654
The dimensions around the quick connect system are quite vaque, is seems to be 11.6mm diameter quick connect nozzle and based on the ST-245 standard
The 1/4" nozzle often come in two flavours BSP and NPT, based on your location one might be easier to find than the other
BSP stands for British Standard Piping and is often a straight thread
NPT stands for National Pipe Thread and is often tappered


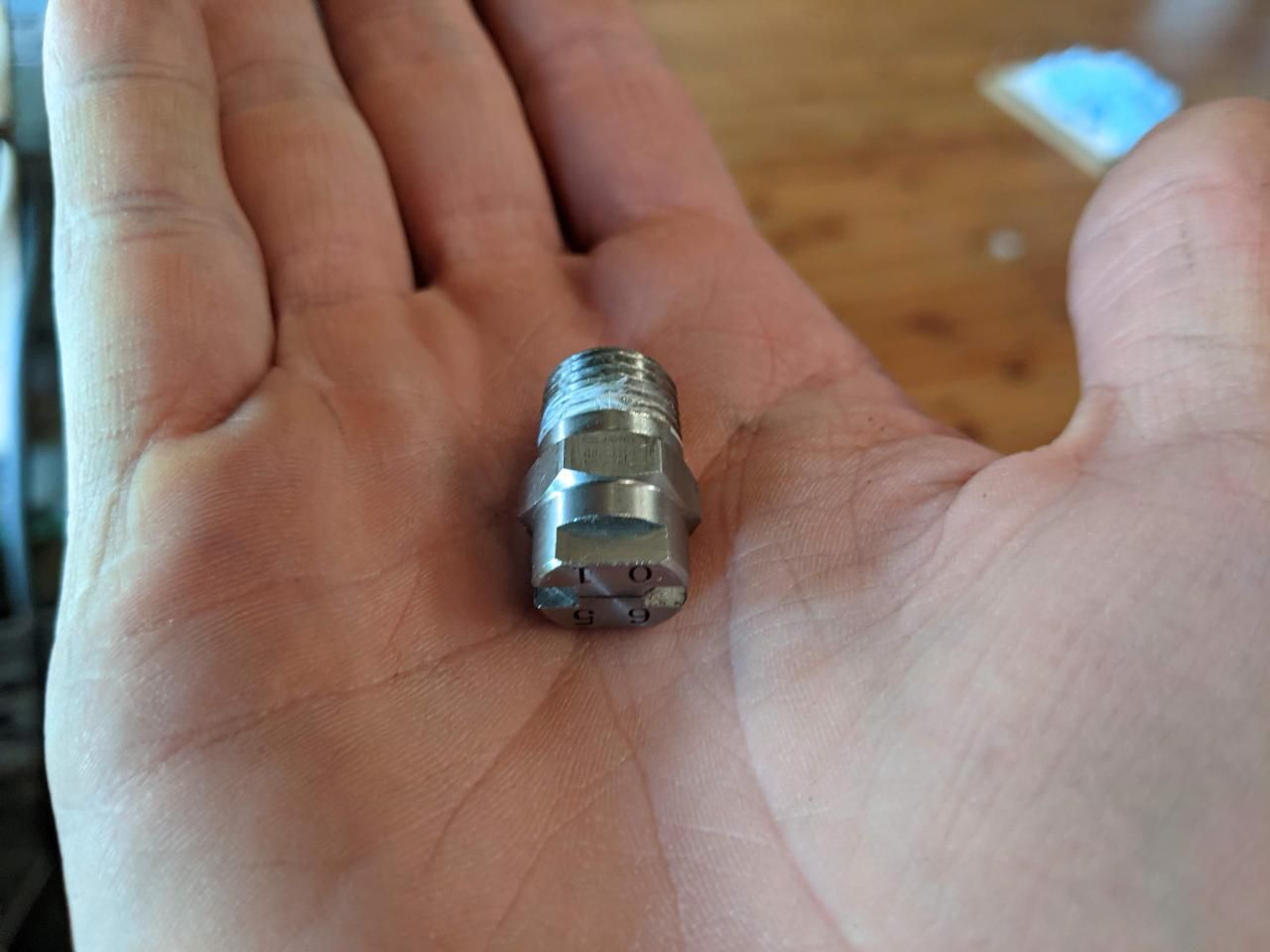
Barrels
Created about 4 years agoUpdated about 4 years ago
Now that we know we want to continue with the barrel concept we need to finalize the type of barrel. for this, both availability and size depend on your situation. We looked at:
- Plastic barrels
- Steel oil drums
- Beer kegs
- Gas bottles
For our situation, we found that 60L plastic barrels work best at the moment.
But you can have a look at this link to make a better decision.
https://docs.google.com/document/d/1cg22cTkioSAFsfuofmadWg8B90DUXwrSAAsXN7WKTRs/edit?usp=sharing
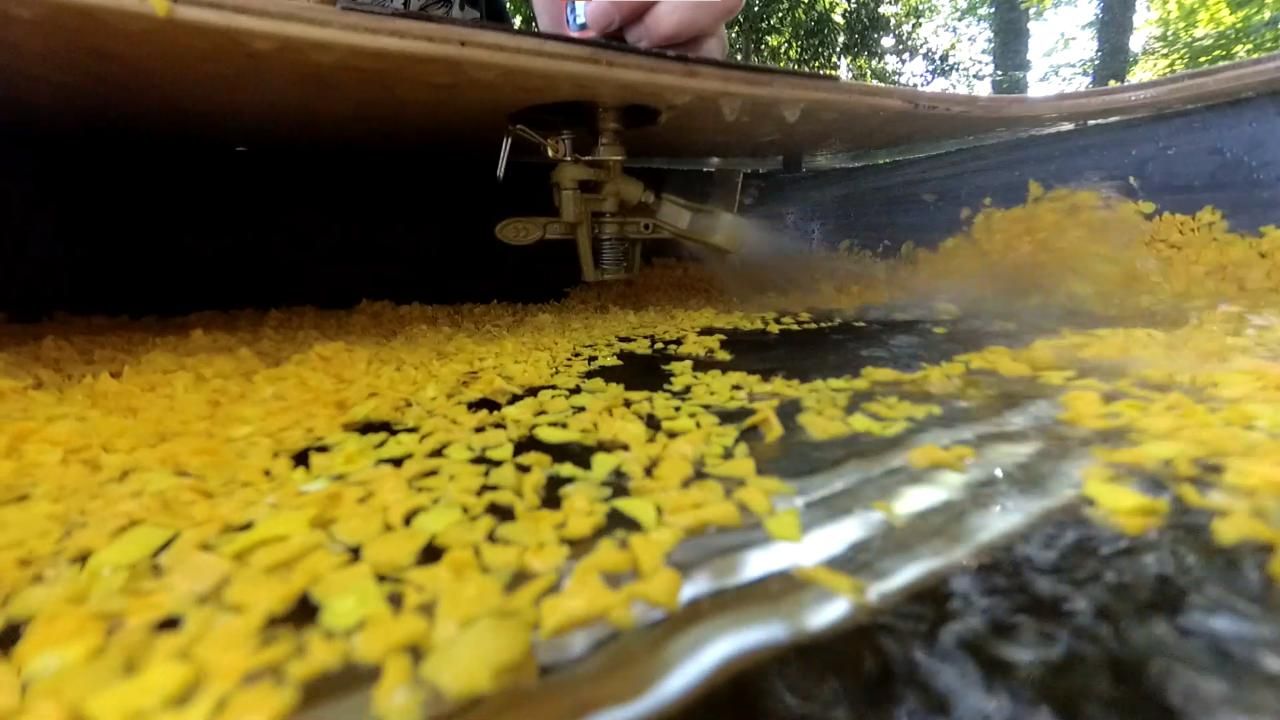
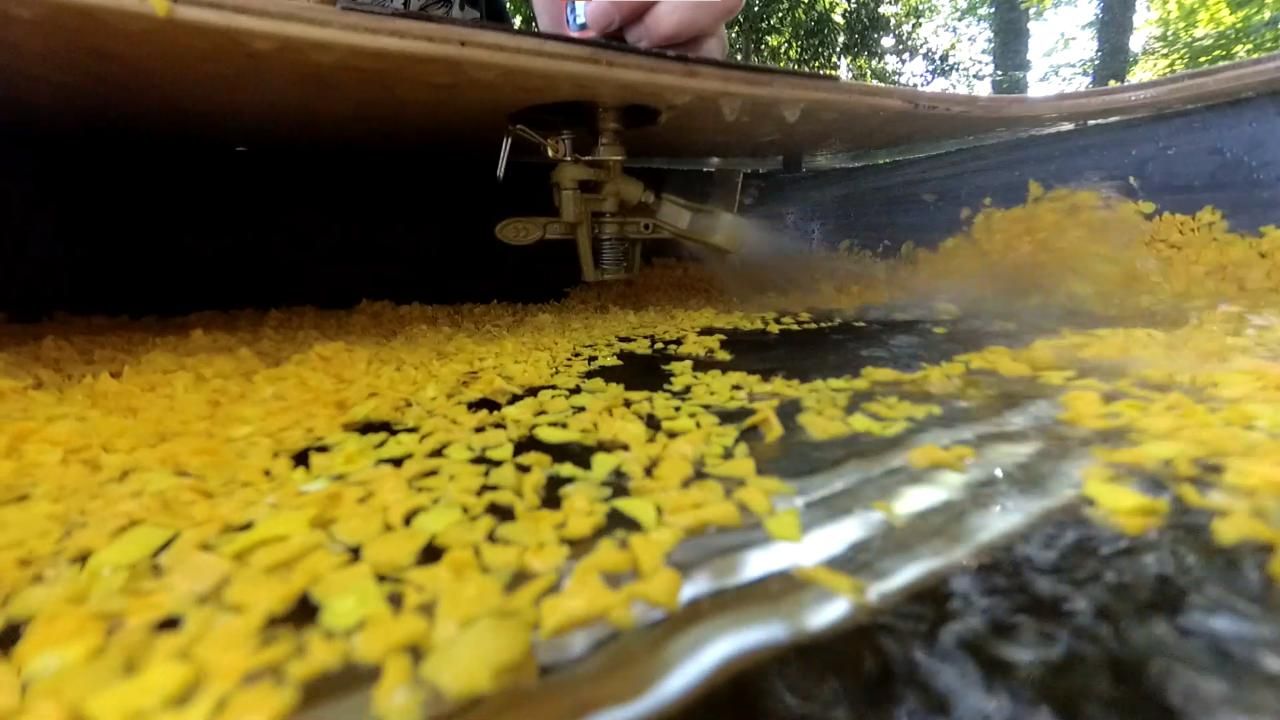
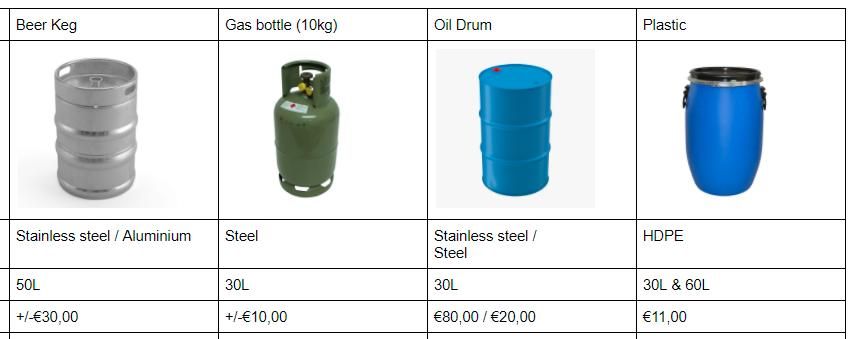
The barrel concept
Created about 4 years agoUpdated about 4 years ago
Apart from the 3D modeling we have done, it is good to test assumptions in real life.
One of the challenges we still had to resolve was:
- How to drain the water from the barrel without moving the barrels themselves
- How to dry the plastic within the barrel
Draining the water:
The most logical step to drain the water from the bottom is to add a valve at the bottom. But adding a valve at the bottom of each barrel is quite unhandy since you cant stack it anymore. the alternatives became
- a pipe on the inside where the water can be sucked from
- a one-way valve at the bottom
- a greedy cup mechanism
In order to choose from these we made a decision matrix in this link: https://docs.google.com/document/d/1m5F2cuWzINYW3SzyIPAi2euoB07TgAM2Yk9_fdbOFfQ/edit?usp=sharing
Drying in the barrel:
[Rory]
Conclusion:
Even though the principle of having the barrels move instead of moving the plastic has a lot of advantages the challanges with both the draining and drying made it not worthwhile to continue on this principle. Taking a step back and reviewing the concepts we previously looked in to gives us room to start moving toward a new concept. Taking the lessons learned from this to a new stage.
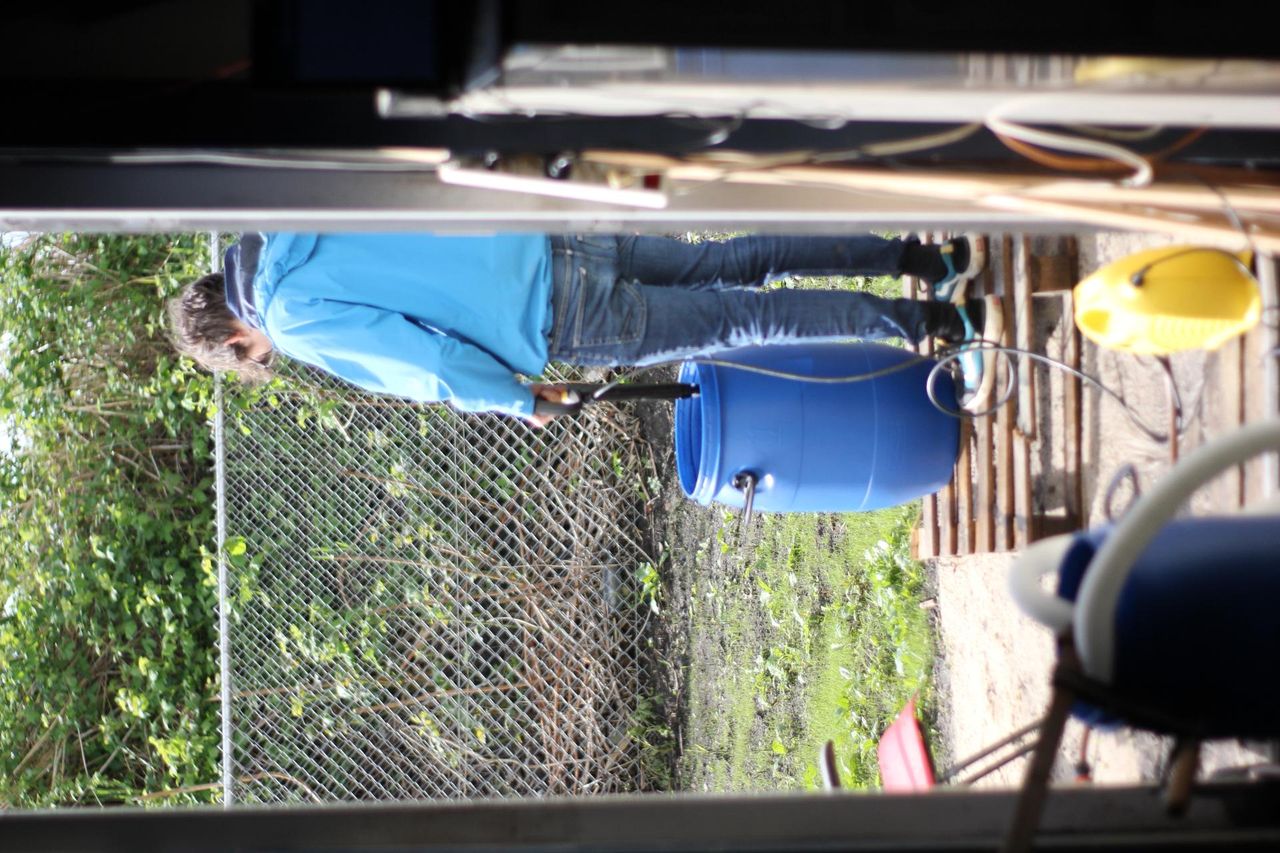
1. Process design
Created about 4 years agoUpdated about 4 years ago
A process needs to design in which the following conditions are taken in to consideration:
A. The user experience should be easy and fun.
B. The plastics should be agitated as much as possible for maximal cleanness.
C. The process should be easy repeatable.
D. The process should have some adaptability to change the process for less or more clean plastic.
These conditions came together in the following proces:
Washing:
A. The shreds are inserted into the system.
B. The system is closed off.
C. The shreds are agitated with water, causing the water level to rise above the shreds (and for most plastics making the shreds float).
D. The shreds are checked for cleanness.
E. If needed the agitation part of the process is continued.
F. If the required level of cleanness is met the water is drained until under the shreds.
G. The shreds have some time to drip out, and can be checked for cleanness.
H. The shreds are moved to the drying stage.
Drying:
[Rory]
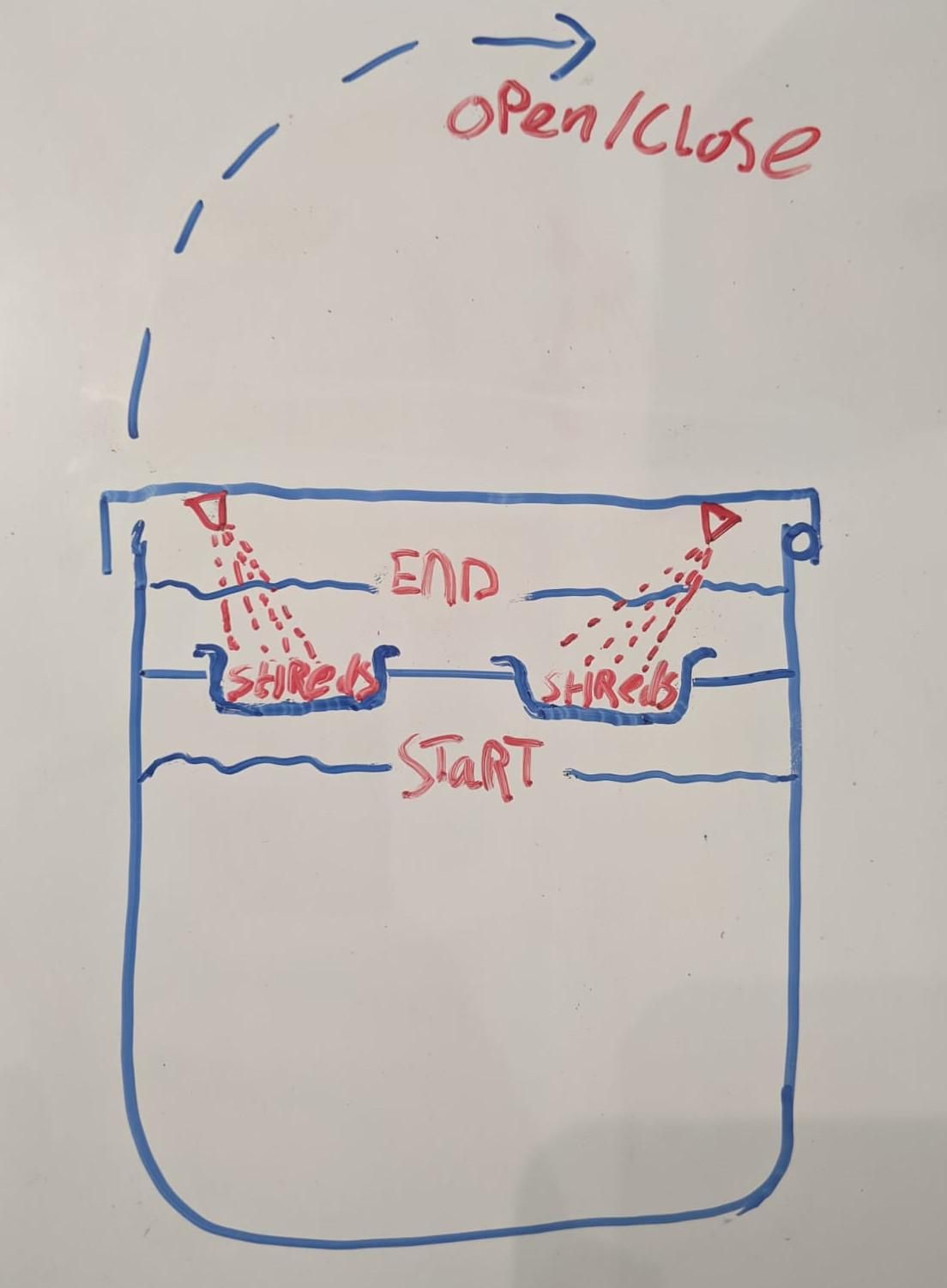
Operation Hose Down
Created about 4 years agoUpdated about 4 years ago
For a new prototype concept we started looking at the system in a different way. We broke the system apart even further than we did previously to find the best solutions to all smaller problems. We knew we had to get solutions for at least the folowing parts of the system.
Sub-solutions:
1. Process design
2. Containing the plastic
3. Containing the washing proces
4. Containing the water reserve
5. Reusing water (closing the loop)
Having partly developed the last concept we already had found some solutions to these problems and made a quick overview of our visions for the system.
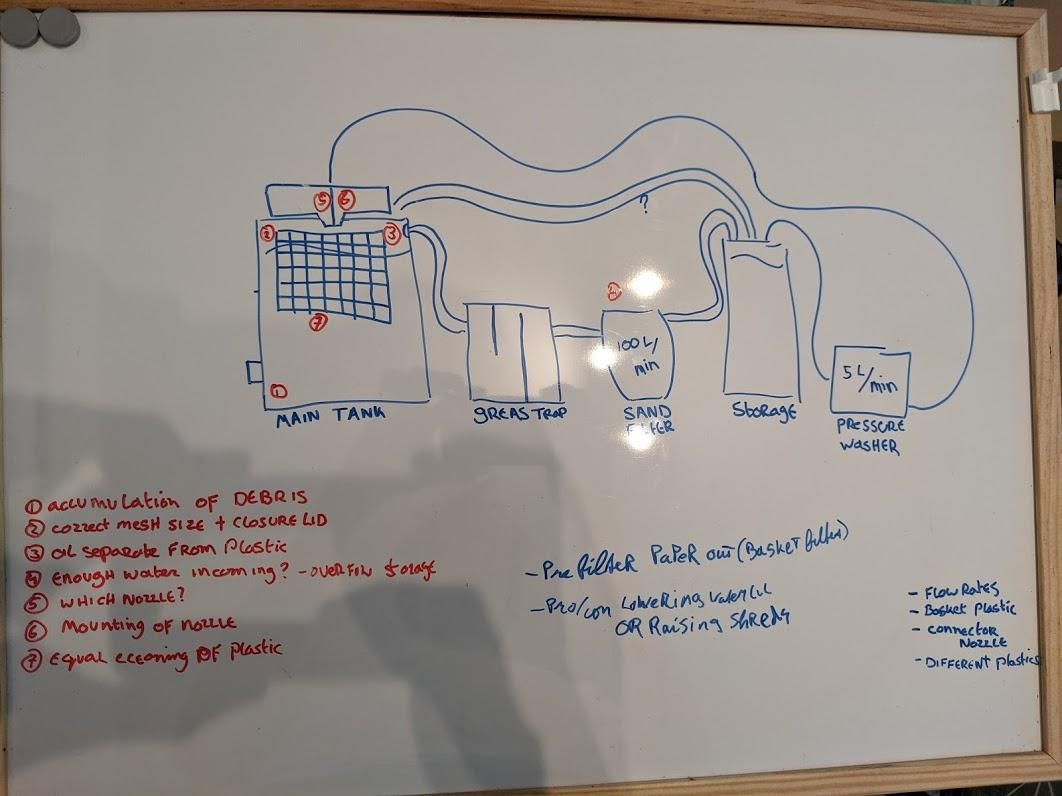
2. Containing the plastic
Created about 4 years agoUpdated about 4 years ago
There are multiple ways of containing the plastic and some experience within the community helped making this decision. The main ways of doing it would be:
A. Woven sacks
B. Mesh containers (eg. a strainer)
C. Floating on water surface (so only wash floating plastics)
Eventually we chose to go with option B for the following reasons:
- The woven sacks are nice as smaller pieces of plastic can't get out. A disadvantage is that dirt might also not be able to get out, and the sacks could absorb the debris we want to wash off.
- Letting it float on the water surface would mean scooping it out in someway, it would limit the system to floating plastics but it would also limit the effectiveness of the pressure washer as the plastics would have to much freedom to move.
- The mesh containers have the best of both worlds; they let water through easely (not holding the debris inside), the containers can be removed from the system instead of scooping the plastic out and the mesh creates a surface for the pressure washer to blast against.
Next we needed to find the most suitable container. This researched has been summarized in this google sheet: https://docs.google.com/spreadsheets/d/1SYMA2rWNijTsH8i4_4smJBMV4OEaATGPyeDEQWUmj4Y/edit?usp=sharing
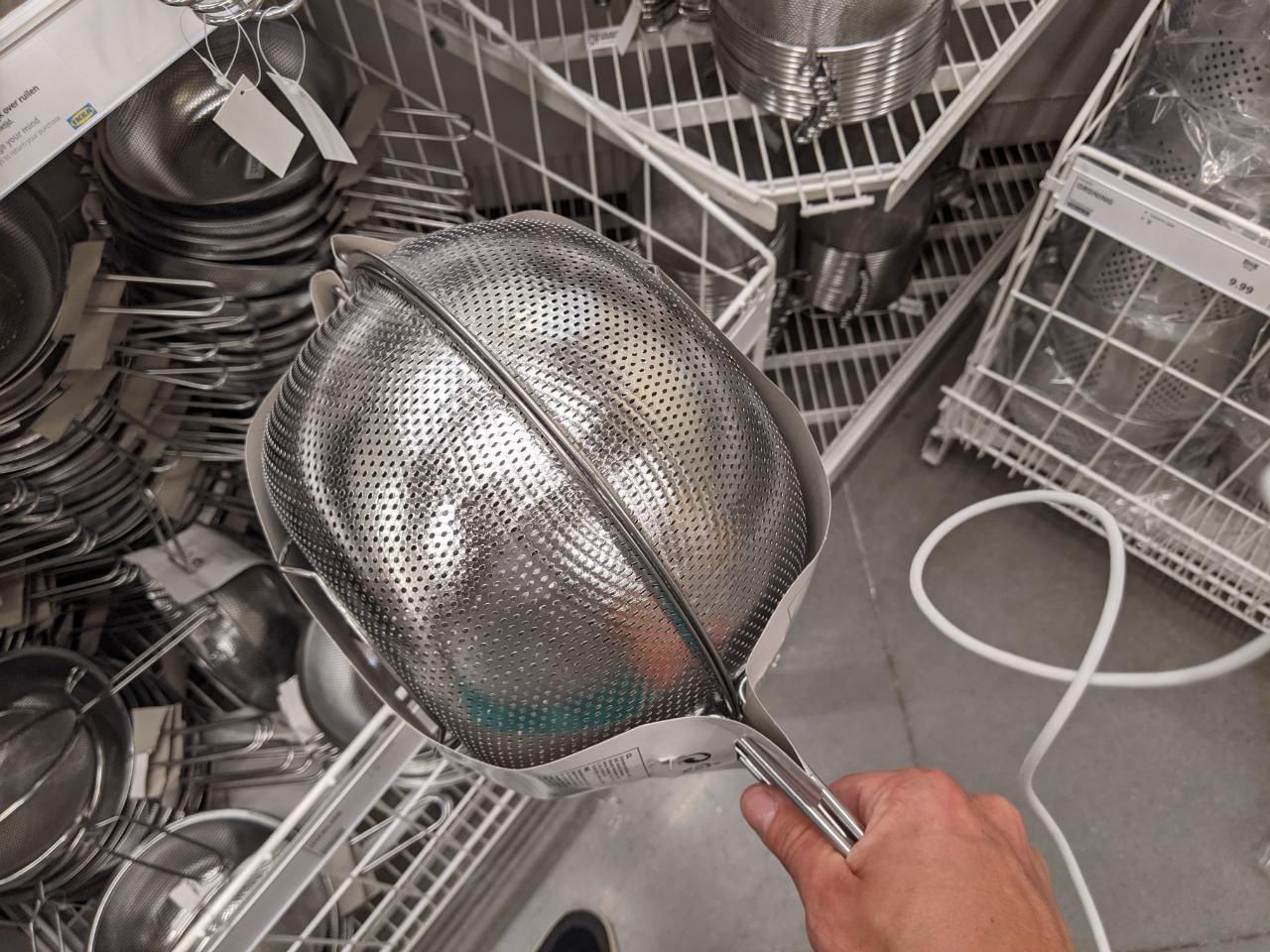
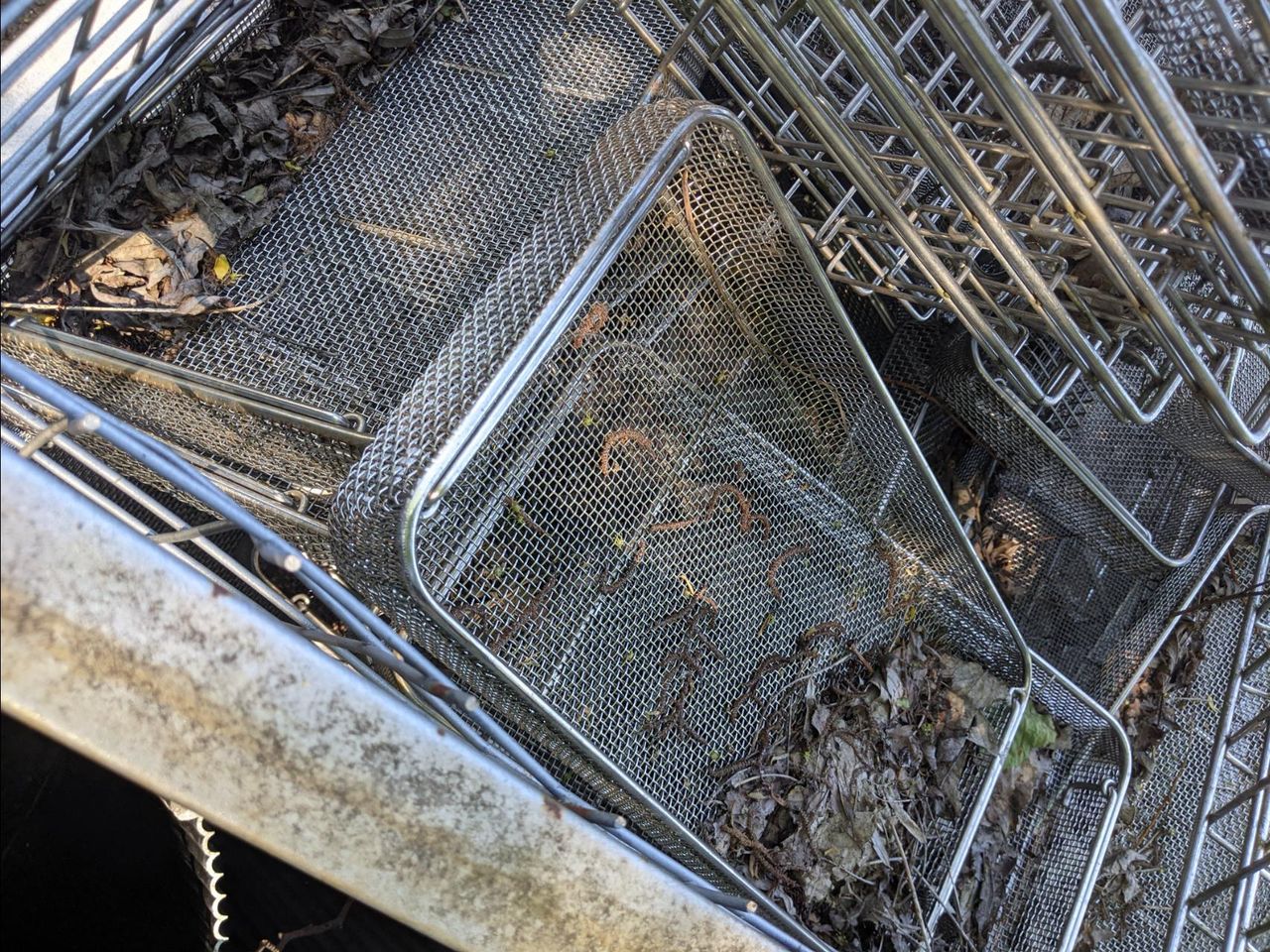
3. Containing the washing proces
Created about 4 years agoUpdated about 4 years ago
For containing the washing proces we need a waterproof enclousure in which we can easily mount and remove the mesh containers found in the previous part. We would like this to be as standardized as possible so it can be obtained cheap and easy. If we think about cheap watertanks we quickly come to IBC's (Intermediate Bulk Container). The most common is the 1000l one and can be obtained for about 70 euro used.
For our needs right now the 1000l one is too big, but IBC are available in smaller sizes as well. These are less common and therefore relatively more expensive. A 300l is least common but best suits our purpose.
The 300l IBC cost around 150 euro, so for testing purposes we use a 300l rain collection tank. These dont have a frame and are therefore less strong.
A frame to hold the tray's in the tank was quicly made from a sheet of recycled plastics and now we can place the tray's in the tank.
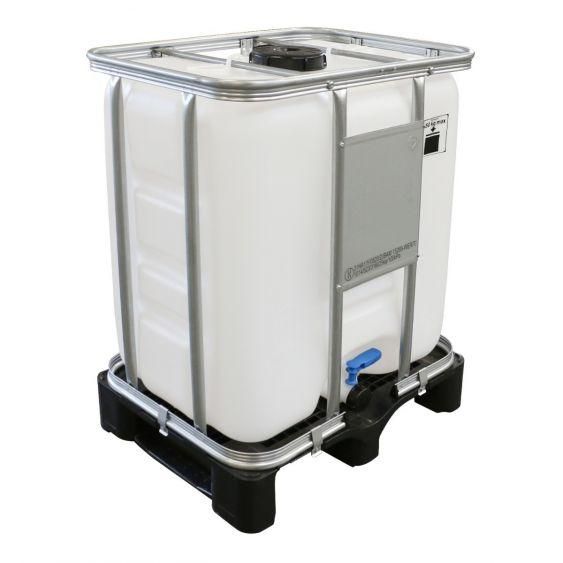
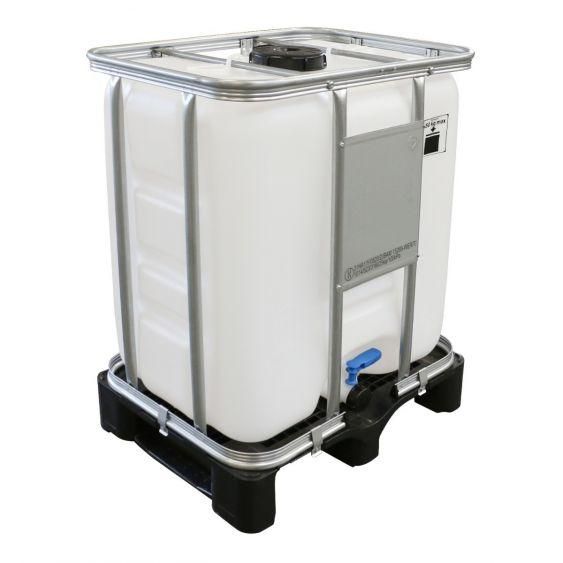
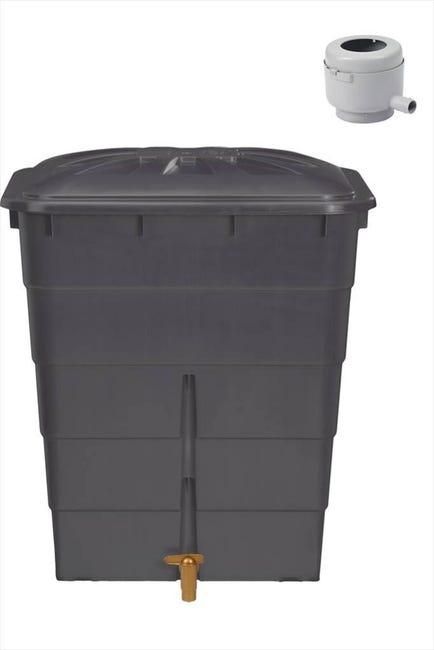
4. Containing the water reserve
Created about 4 years agoUpdated about 4 years ago
In almost all concept we have investigated the main way of cleaning was water. This means you will end up with dirty water, which needs to be either wasted or filtered and reused to create a closed loop. Of course we prefer to create a closed loop, and thus there is a place needed to save the clean water to be reused.
For storage tanks the following options were considered:
A. 1000l IBC
B. 300l IBC
C. 60l Storage barrel
D. Use no storage tank (or use the process container as storage)
The conclusion of this decision depends heavily on the process we choose, but for now we prefer to have no storage tank or the smallest possible one.
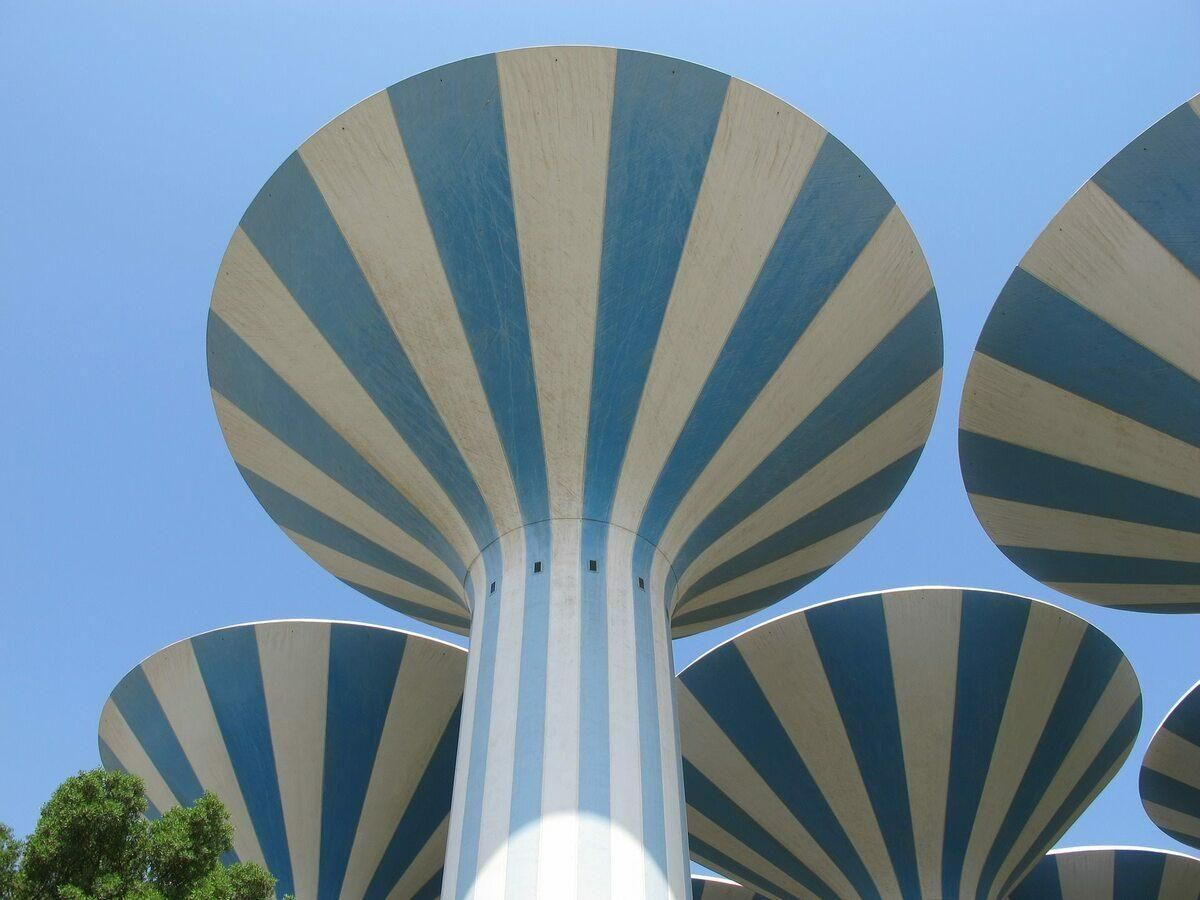
5. Reusing water (closing the loop)
Created about 4 years agoUpdated about 4 years ago
The last sub-solution is probably the most important (and most overlooked) part of every design process. In this case the closing of the loop isn't for the life cycle of a product but for the water we use and need to reuse.
Reusing the water means we need to filter the debris cleaned of of the plastic out from the water. To do this we first need to look at what possible contaminants there will be.
Expected contaminants:
A. Sand
B. Oil & grease
C. Micro plastics and other small pieces of plastic (as a side product from shredding)
D. Biological waste (eg Yogurt)
E. Paper labels
In previous versions a sand filter was used to clean the water. This works very well, but using this to clean out all debris would mean the sand in the filter needs to be replaced often. Also all the debris would be in the same place thus making it impossible to dispose of them separately. This is why different stages of filtering are used in series.
Filter steps:
1. Heavy particles have time to sink in the main tank (large volume in the bottom of the main tank).
2. A grease trap separates the oil and grease floating on the surface from the water.
3. Water flows into the dirty reserve, and gets pumped into the clean reserve by the sandfilter pump from where the water can be reused in the process.
Now for each part there should be a cleaning protocol, as some of the debris should be handled with care. This especially goes for the micro-plastics that will probably be in every part of the system.
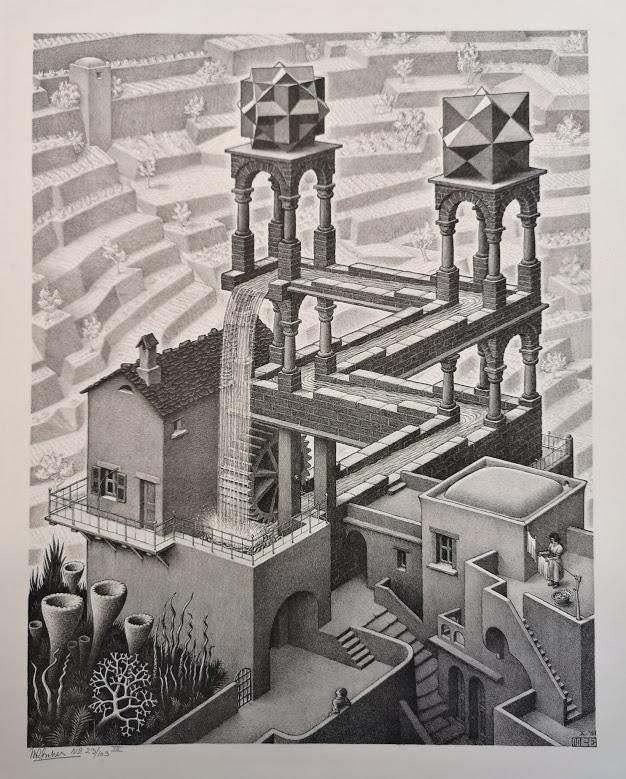
Cleaning: High-pressure or Low-pressure?
Created about 4 years agoUpdated about 4 years ago
Next focus: how will the water be moved? A pump would be the most logical choice, but then what kind of pump should that be? For this research update we will look into two different type's of pumps (to keep things simple).
We will be discussing:
- Pressure washer pump (HP up to 200 bar and low flow rate)
- Irrigation or surface water pump (LP up to 5 bar and high flow rate)
A HP system may seem the most logical choice (more force = more clean right?). Also a basic pressure washer seems to do the job just fine and they are pretty affordable. But the washing system should be durable and have a long life cycle as well. This is where the low pressure option gets interesting, because it turns out the yellow consumer pressure washers have a life cycle of about 500h, and they cannot run continuously.
A LP pump however is designed to run for hours or even days on end and the life cycle is closer to years than hours. The main downside however is that there is less force to clean the plastic, concentrating the force using a sprinkler will eliminate this to some degree but tests show there should at least be 4 sprinklers to be able to hit all plastics. Research shows that a big pump is needed for this, along with pretty rugged (and thus expensive) sprinklers, bringing the cost up.
In conclusion: the costs is probably equal for both systems, the low pressure is probably less maintenance but also less cleaning. So a professional pressure washer is the way to go.
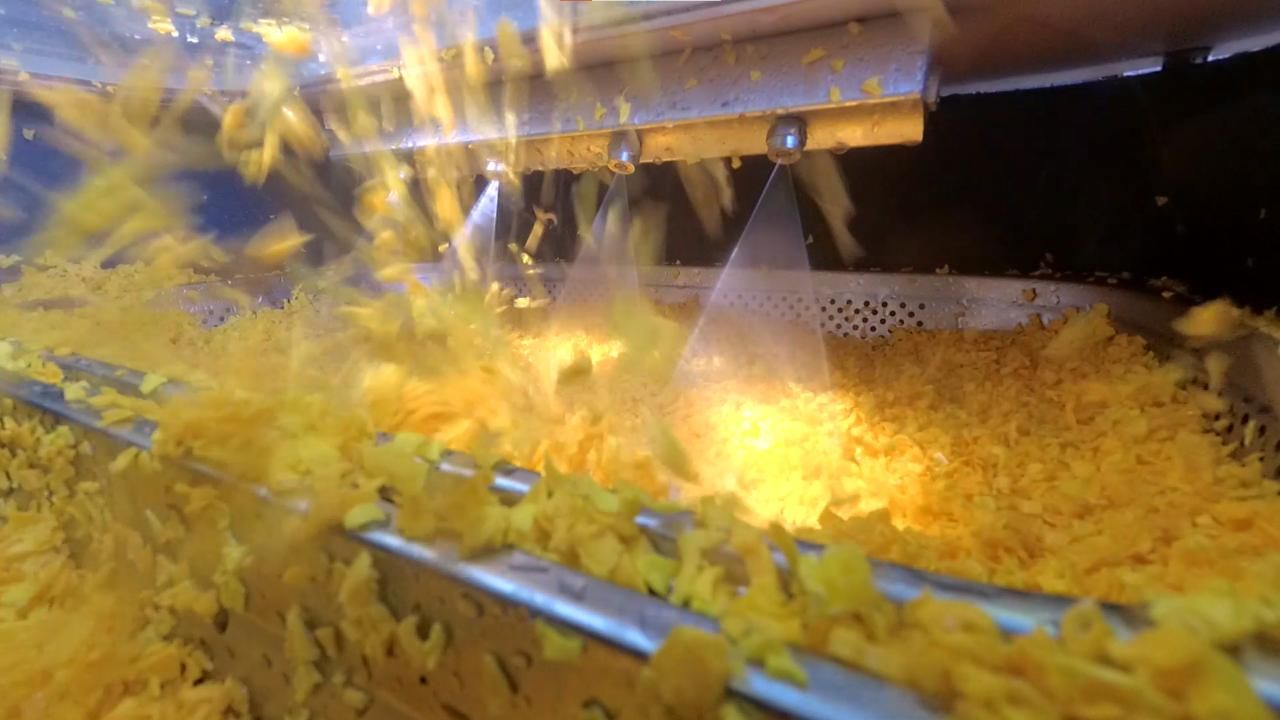
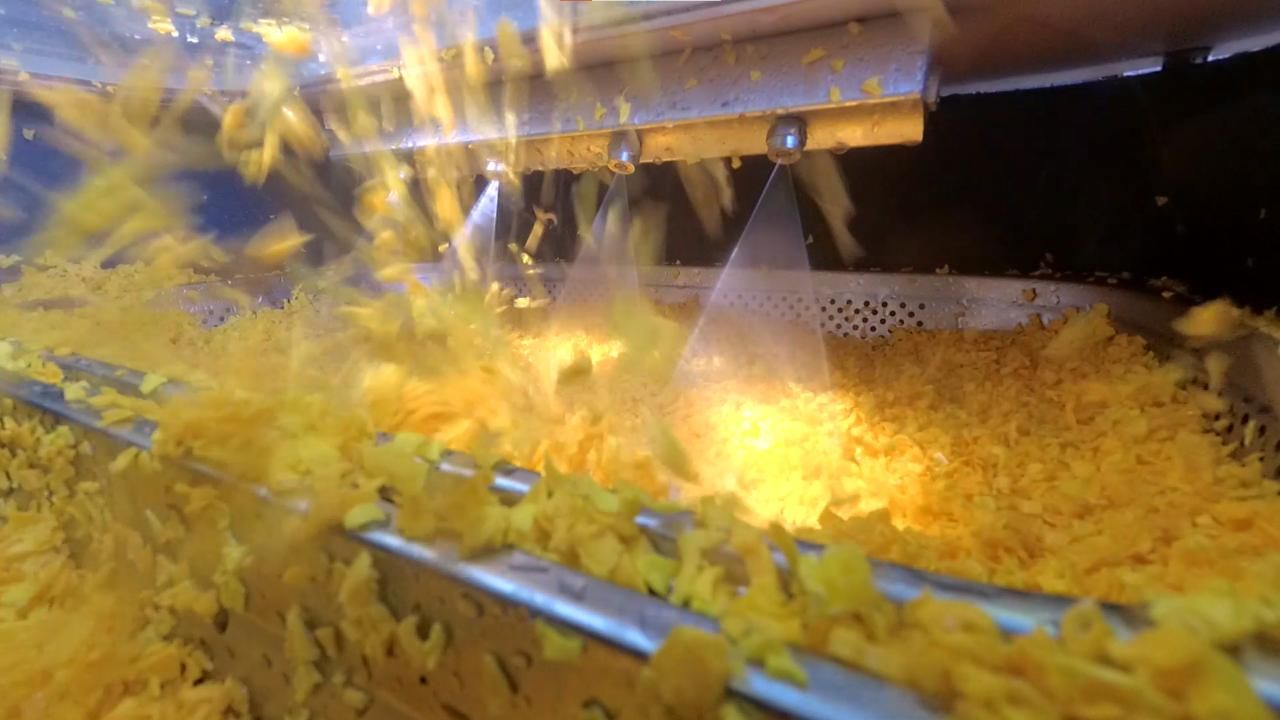
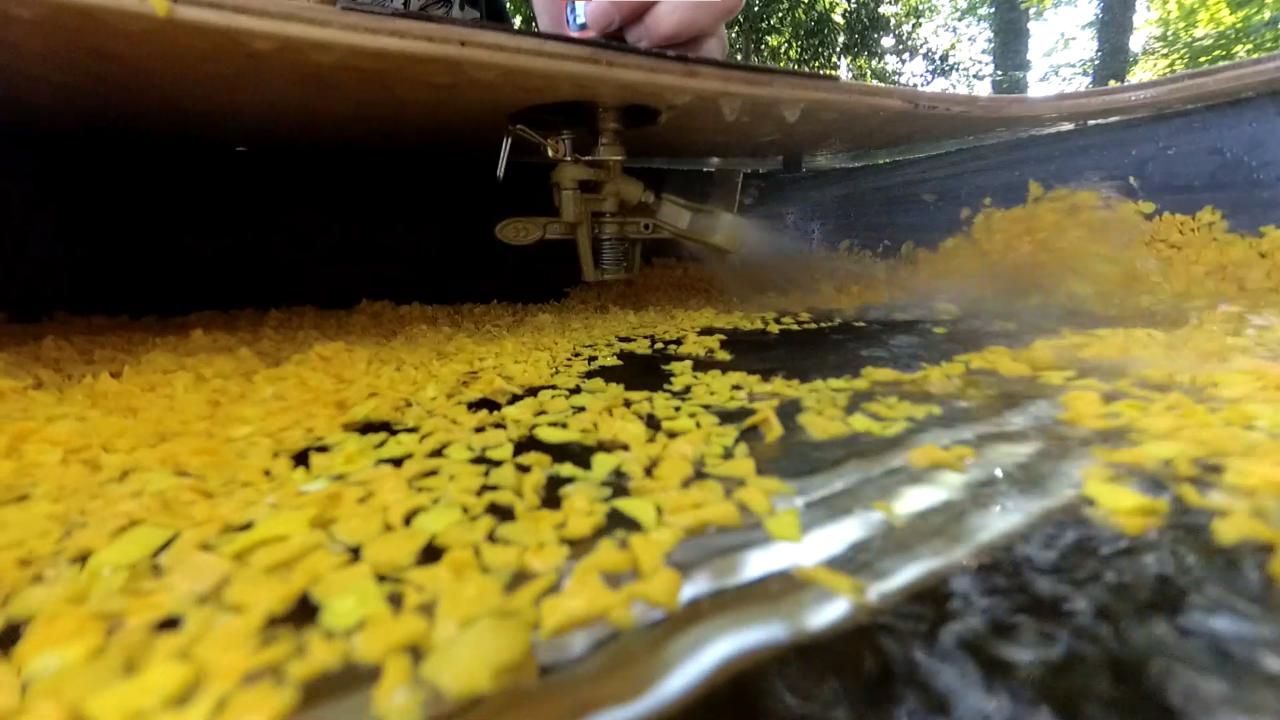
High pressure or high flowrate?
Created about 4 years ago
After making the decision to go with high pressure cleaning the next step is to find a suitable pressure washer. The system is designed to clean 4 kg of plastic per hour. For this we want to use 4 rotating nozzles, one in each corner of the main tank.
First we tested with rotating nozzles with a 040 orifice, and a pressure washer with 9l per minute. In this test we found that the combination of 4 large nozzles and a pressure washer with a normal flow was not ideal. We tried to find the smallest possible orifice on the rotating nozzles which is 025. Four of these in combination with the same pressure washer gave a decent pressure on the nozzles (not a pleasure to point at your hand).
Conclusion: The ideal pressure washer has a high flow-rate, the pressure is less important. Also the life span of the machine is important. The usual household pressure washers are not meant to be running for hours per day, we found that these have a life span of 500 hours (50h per year * 10 Years). The professional ones have ceramic plungers and brass pump heads.
Find the pressure washer that suits your situation! You might be able to use cheap second hand ones if your usage is different. As we need the machine to operate 8 hours per day we are going with a semi-professional one with a flow rate of 10,5l per minute.
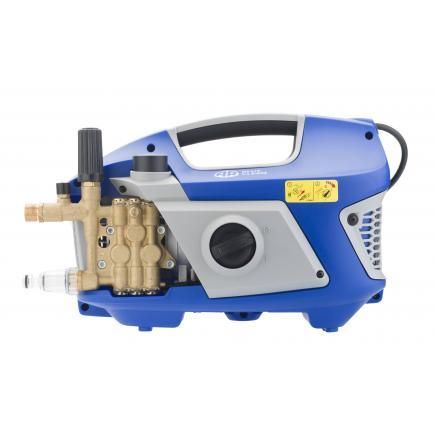