Moulds
Make a Modular Furniture Clip + Mould
As part of the PPOSF, Sustainable Design Studio was tasked with creating a modular furniture clip. Original Research Topic: https://community.preciousplastic.com/research/modular-furniture-clip The modular furniture clip mould makes it easy to create versatile and stylish furniture, displays, or storage solutions. Designed for 9mm—18 mm thick sheet materials, this mould allows you to join panels together with a handful of clips, enabling endless design configurations. Whether you’re assembling furniture, setting up trade show displays, or organizing your space, this mould is perfect for small-scale production and DIY projects.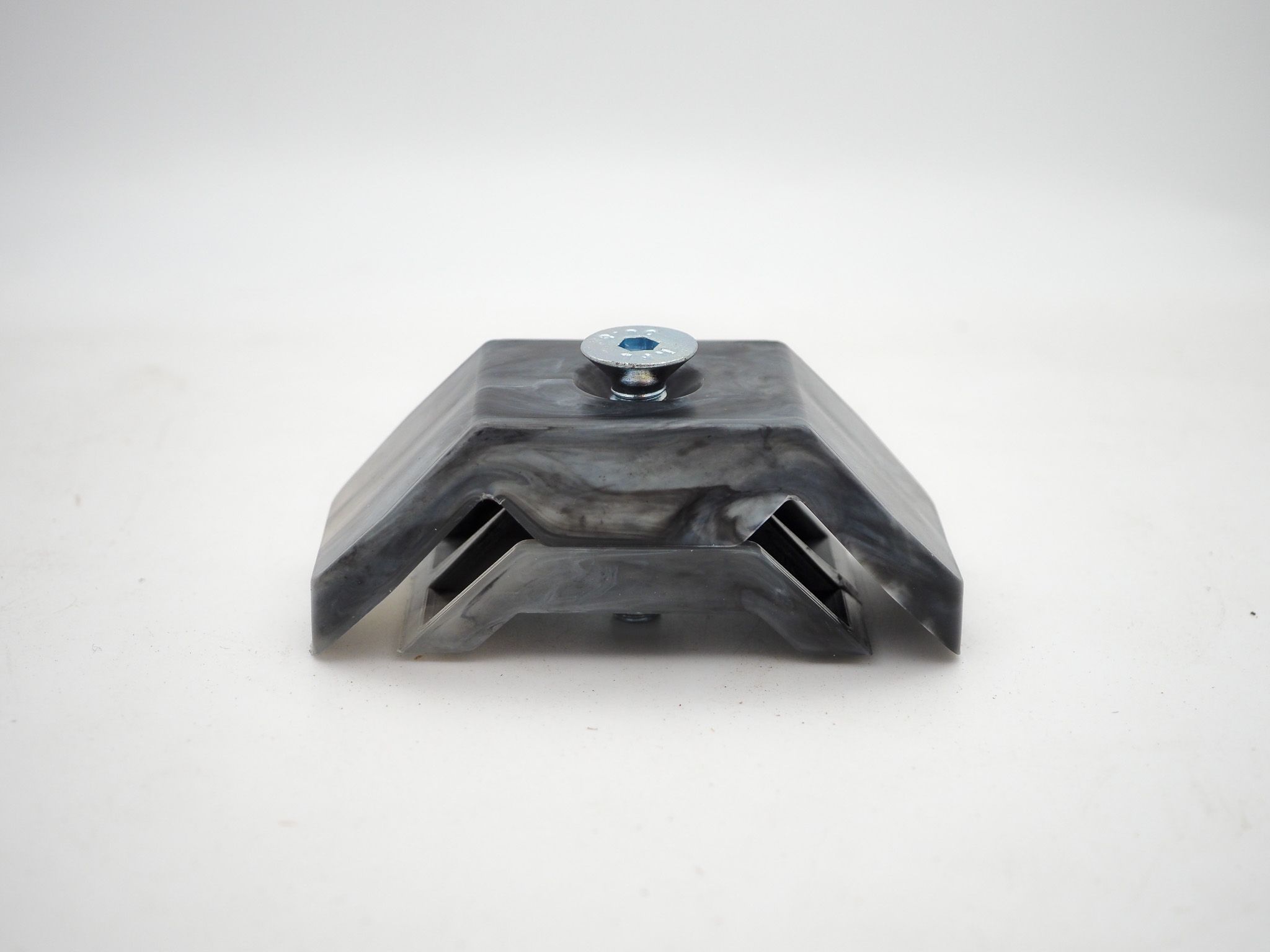
More Information
1
Download & Machine the Mould
In the .zip folder you will find all the files you will need to machine your own mould (Part A and Part B) in STEP format.
Please note the STEP file is in "mm".
The mould fabrication of this part is very complex, with multiple curved and drafted angles. Therefore, we wouldn't recommend attempting to machine your own mould without knowing what you are doing or seeking the advice of a professional machinist.
Additional information:
- Due to the intricacies of the design you will need a R1(mm) ball bit to achieve the precision of this design.
- The mould should be machined from Aluminium 7075 to ensure long-term durability and strength.
- We recommend the mould be anodised to achieve a better finish.
- The mould requires:
4pcs M8x80mm
8pcs M8 Washers
4pcs M8 Nuts
If you want to have the mould fabricated for you. We sell the mould on the Precious Plastic Bazar here:
https://bazar.preciousplastic.com/moulds/injection-moulds/premium-mould-20-modular-furniture-clip-mould/
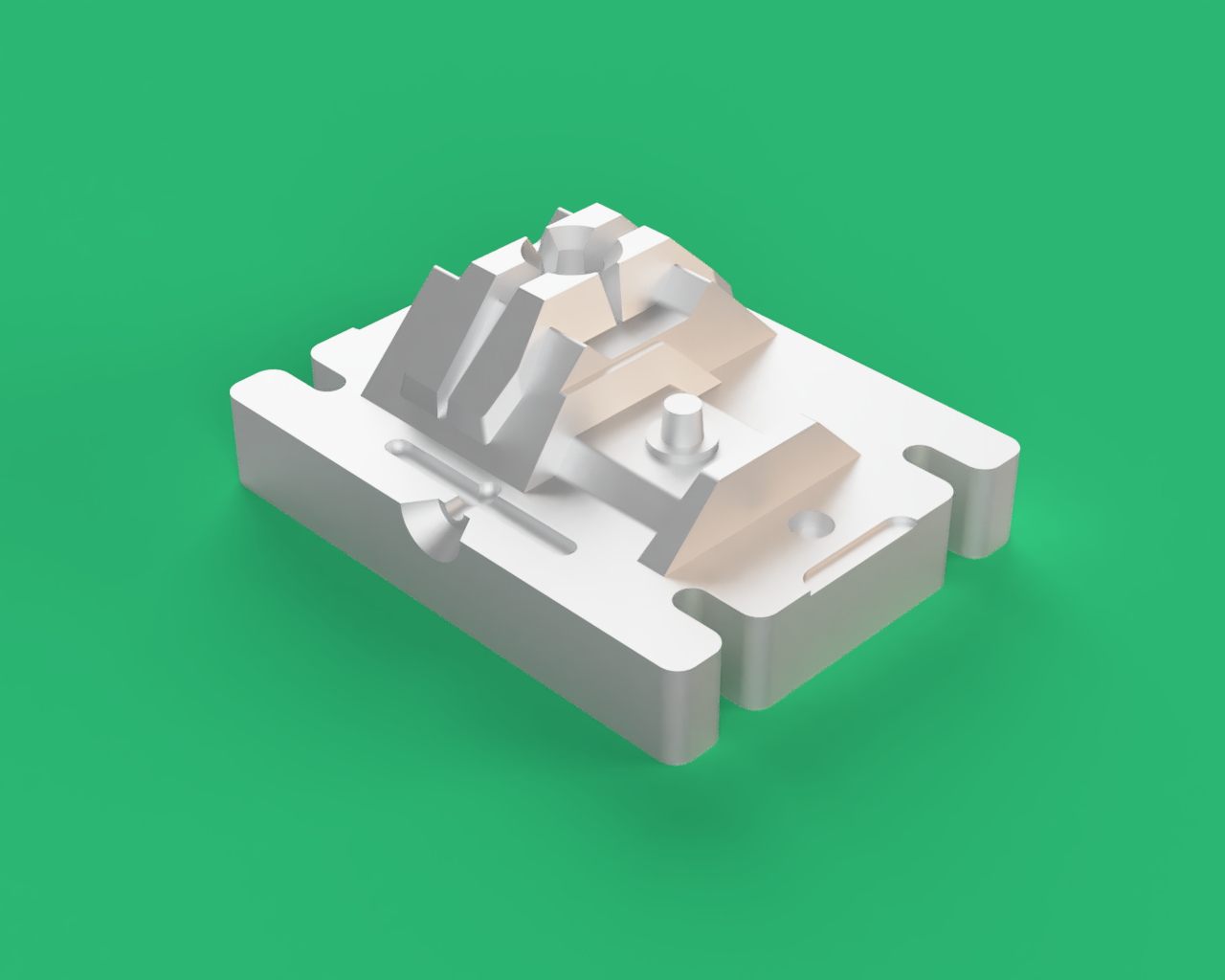
2
Inject
When injecting with this mould there are a few important things to take note:
- Since this mould is for structural use. We recommend injecting with PP, and avoid HDPE. HDPE is to soft and bends over time. PP is stronger and lasts longer.
- A warm mould is required to inject into to ensure success. Its also best to remove the item while its still hot. Due to large amount of draft angles, it will only get harder to remove when it's cooled down.
- Each injection uses about 37g of plastic.
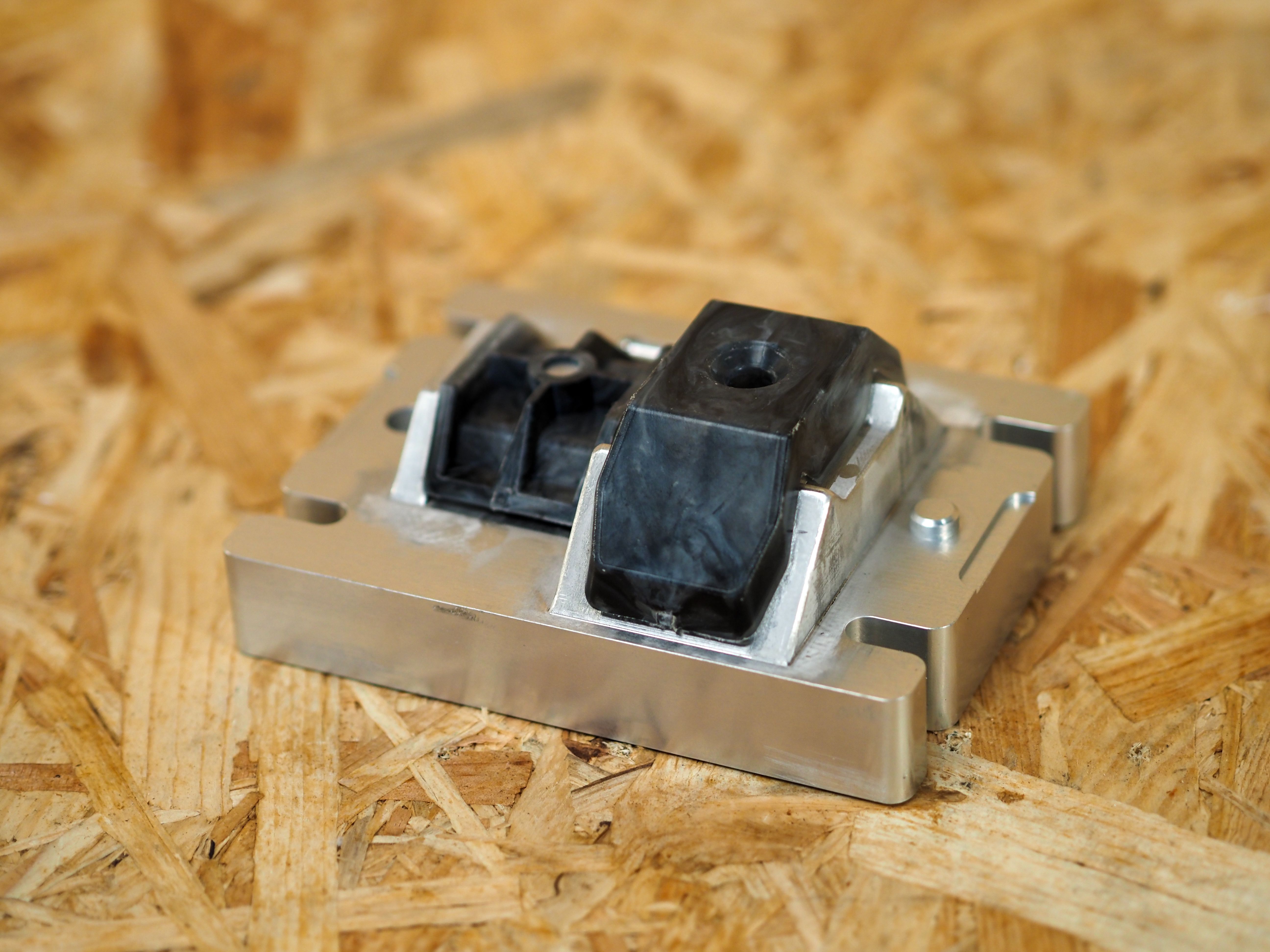
3
Build
With all the components needed to build your furniture, it's time to build.
The build process requires you to cut 9mm-18mm sheets down to size. In our example, we used a 30cm x 30cm template of 12mm chipboard to create a modular shelving unit.
Example units can be created however here is the maths for several different sizes.
1x1:
5x (300x300x12mm) Panels
12x Clips
1x2:
7x (300x300x12mm) Panels
1x (300x646x12mm) Panels
24x Clips
2x2:
14x (300x300x12mm) Panels
1x (646x646x12mm) Panels
42x Clips
2x4:
26x (300x300x12mm) Panels
1x (646x1338x12mm) Panels
74x Clips
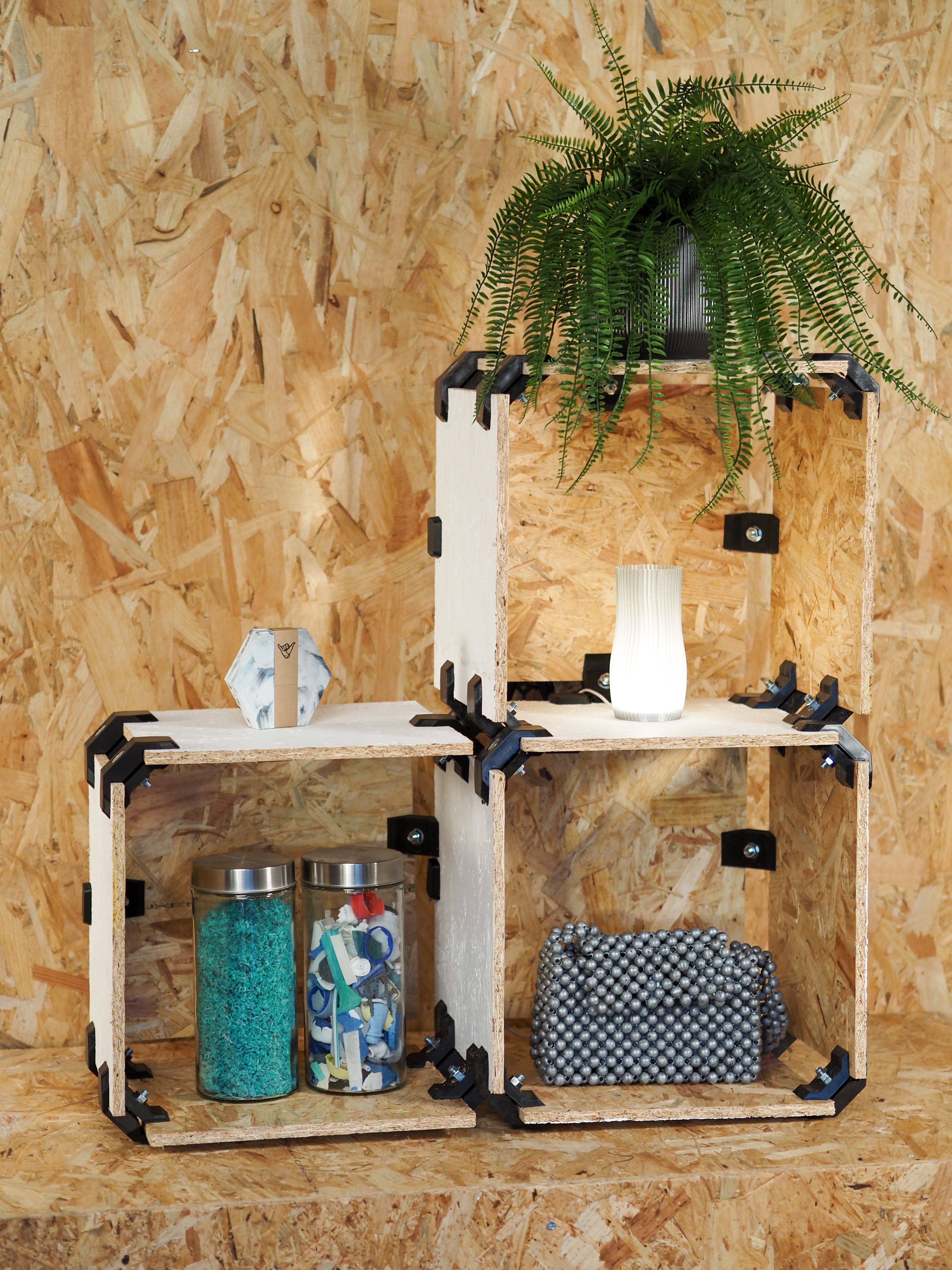
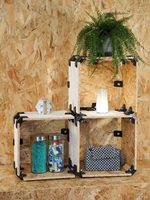
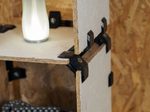