Moulds
Making an Injection Mold Without a Computer
This guide demonstrates a proof of concept for using high-temperature silicone to create a mold for injection molding without the need for a computer. It represents the first iteration of this process, leaving room for improvement. Hopefully, this guide will inspire further development and refinement of the technique.injectionPPmould
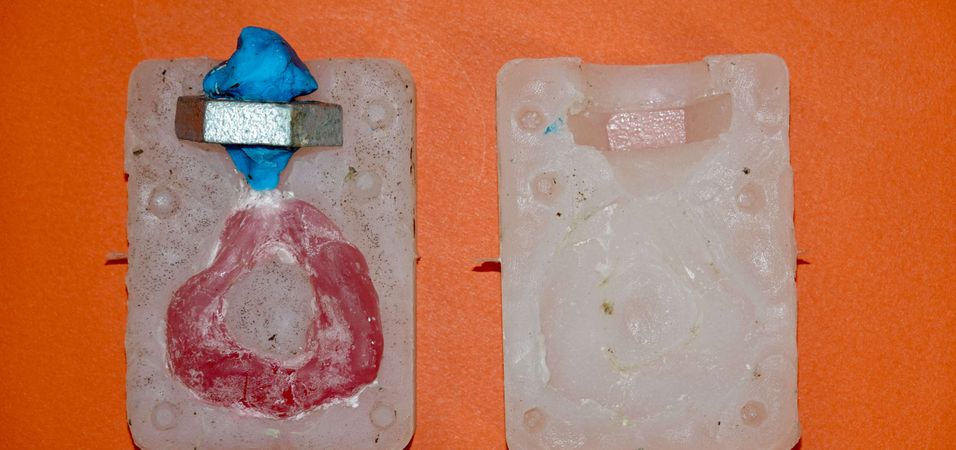
More Information
1
Master Pattern
Select or create an object to use as the master pattern—the object you're making a mold of. In this case, I used air-drying clay, which was difficult to model, so I ended up making a simple, organic-shaped "O." Since silicone is somewhat flexible, some standard injection mold rules, like overhangs and draft angles, can be more relaxed. This flexibility makes the process easier but reduces precision. It's crucial that the master pattern is completely solid before making the mold. You could also 3D print the master pattern or use an existing object.
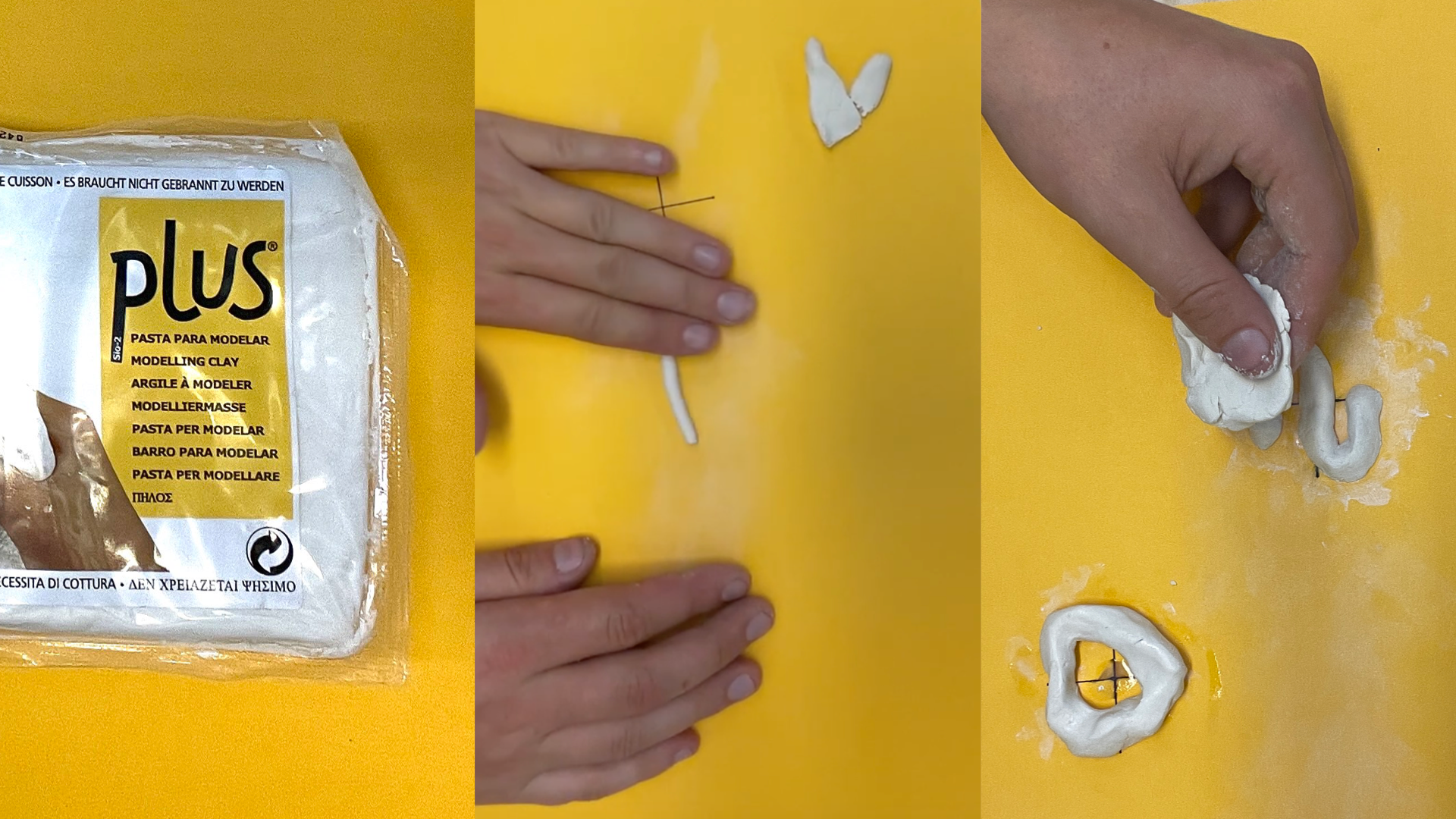
2
Prepare mould
Prepare your two-part silicone mold. For this step, I used a 3D-printed box, but you can easily substitute it with cardboard or wood (see the linked YouTube video for guidance). I've also attached the 3D models to this guide.
Start by creating a clay base for the master pattern to rest on. Embed half of a 1/2 inch lock nut into the clay, and use playdough to form channels for the plastic to flow into the mold. Cover the master pattern with decorative clay along its parting line and place it on the base. Finally, use a hex key to create alignment points where the two parts of the mold can be secured together.
https://www.youtube.com/watch?v=kuIqpiQ1000
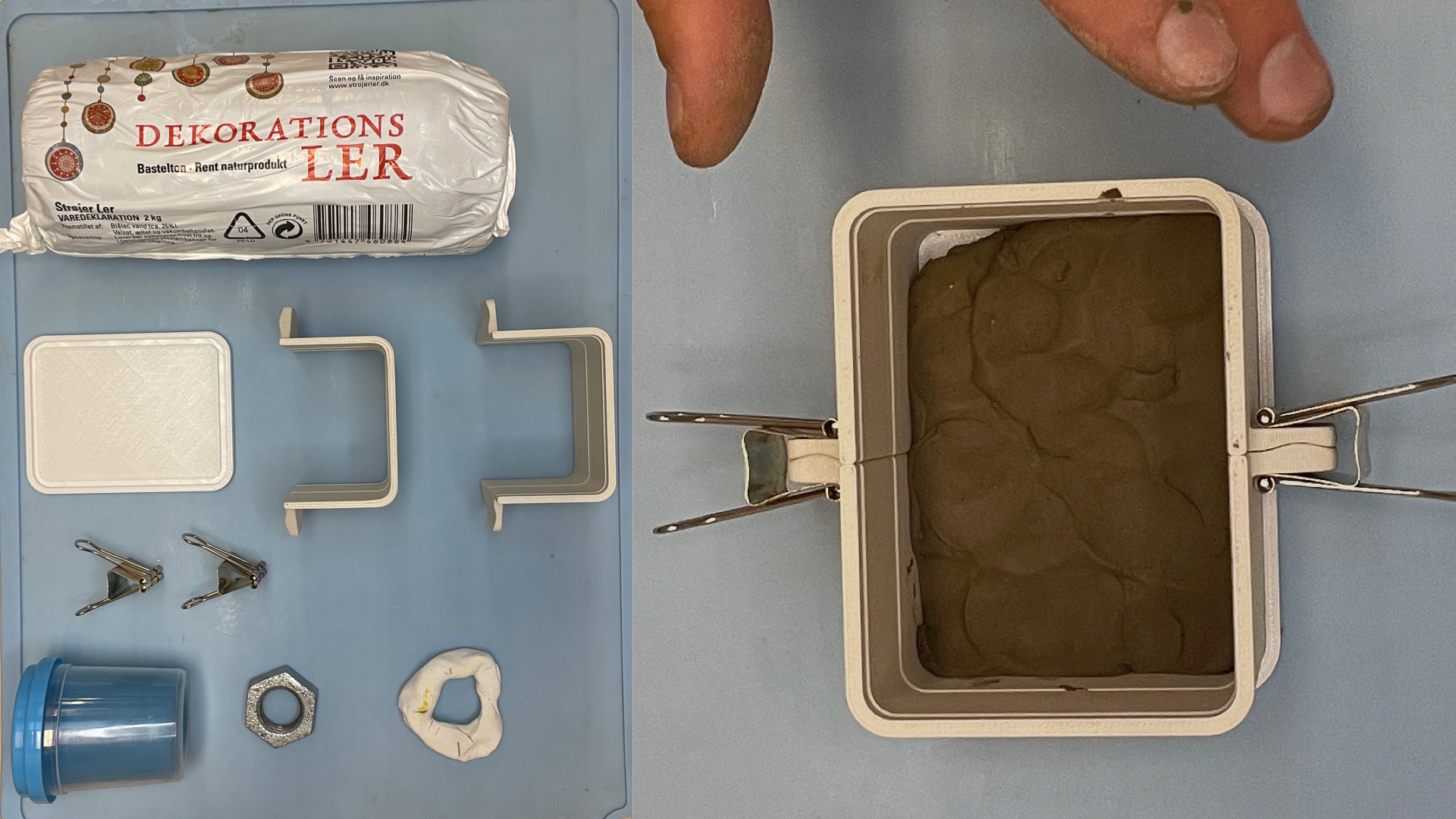
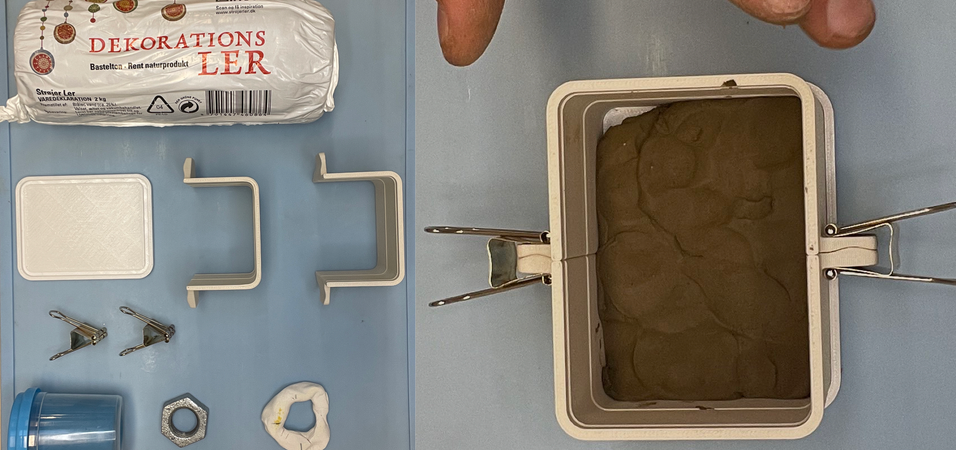
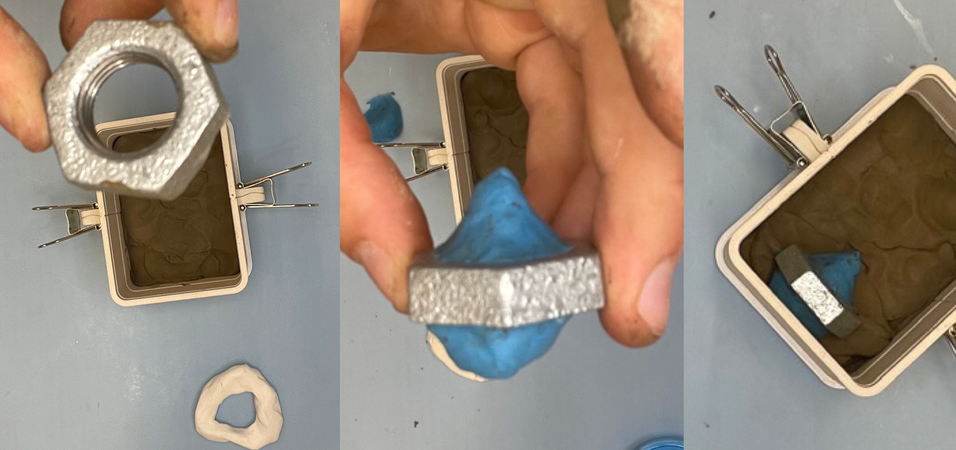
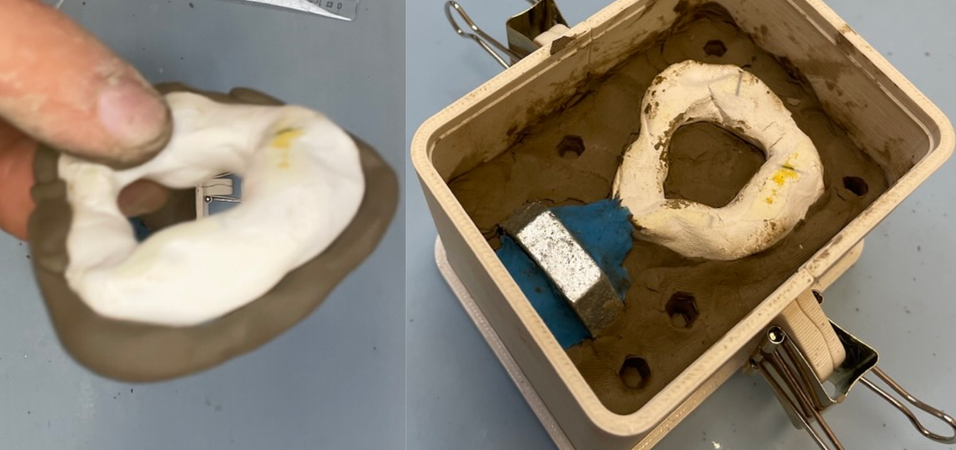
3
Pour 1st part.
Since the plastic we’re injecting is very hot, it’s crucial to use heat-resistant silicone. The silicone I use can withstand temperatures up to 250 degrees Celsius.
First, measure the two parts of the silicone, then mix them thoroughly according to the instructions for your specific product. I used a weight for this but you could also use measuring cups. Once mixed, slowly pour the silicone into one corner of the box, allowing it to flow over the master pattern naturally. This method helps prevent air bubbles. Leave the mould to cure for the recommended time specified for your silicone.
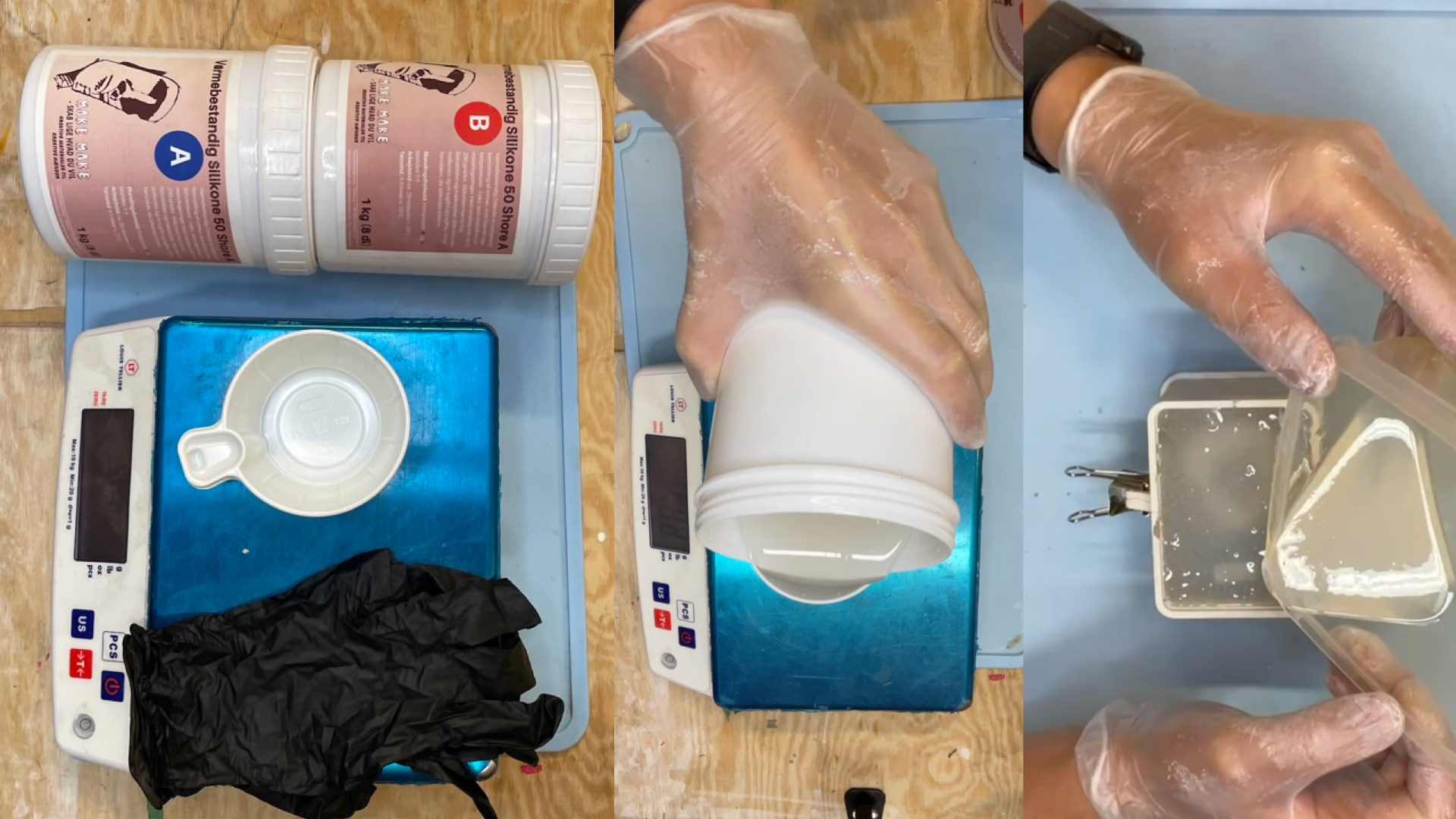
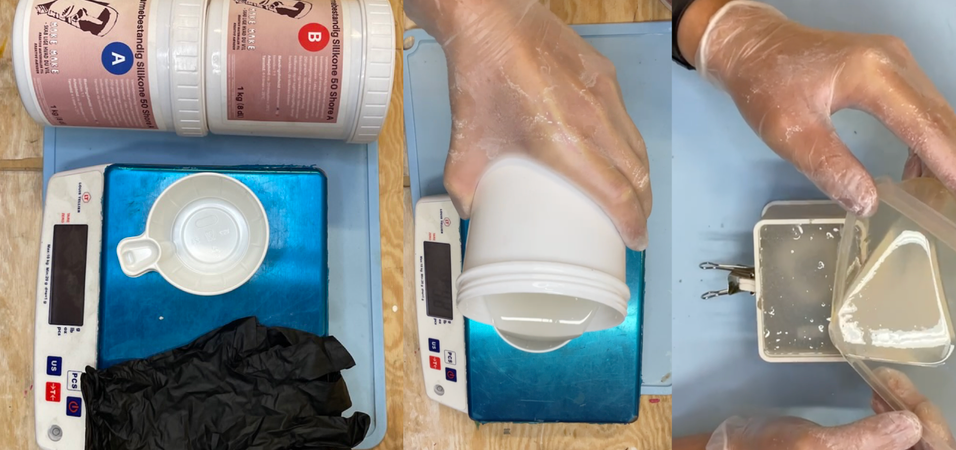
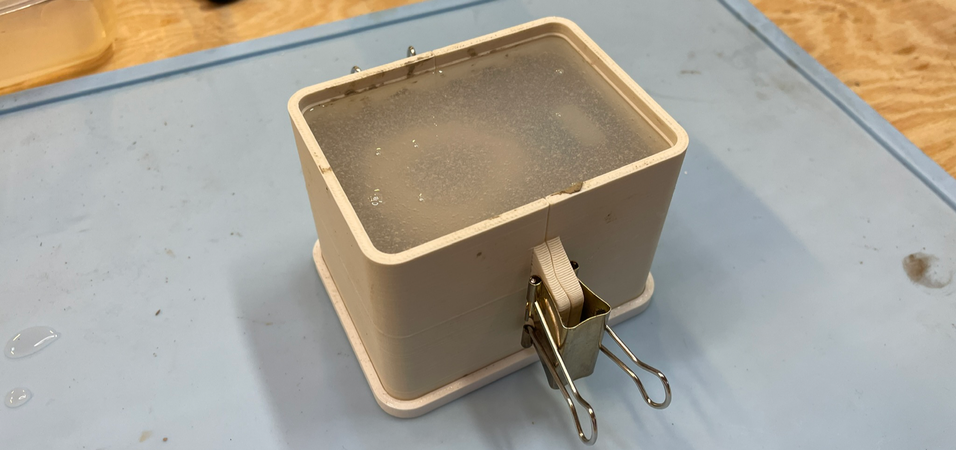
4
Pour 2nd part
Once the silicone has cured, carefully remove it from the box. Next, take out all the decorative clay while keeping the playdough, lock nut, and master pattern in place. I found cleaning out the decorative clay quite challenging, so consider using a different material for easier cleanup.
After cleaning, place the first part of the mold back into the box, positioning it at the bottom. Spray it with mold release, then pour a new mixture of heat resistant silicone over it.
Once cured, the two mold halves should separate easily. You can then remove the playdough, lock nut, and master pattern, and wash the two parts thoroughly.
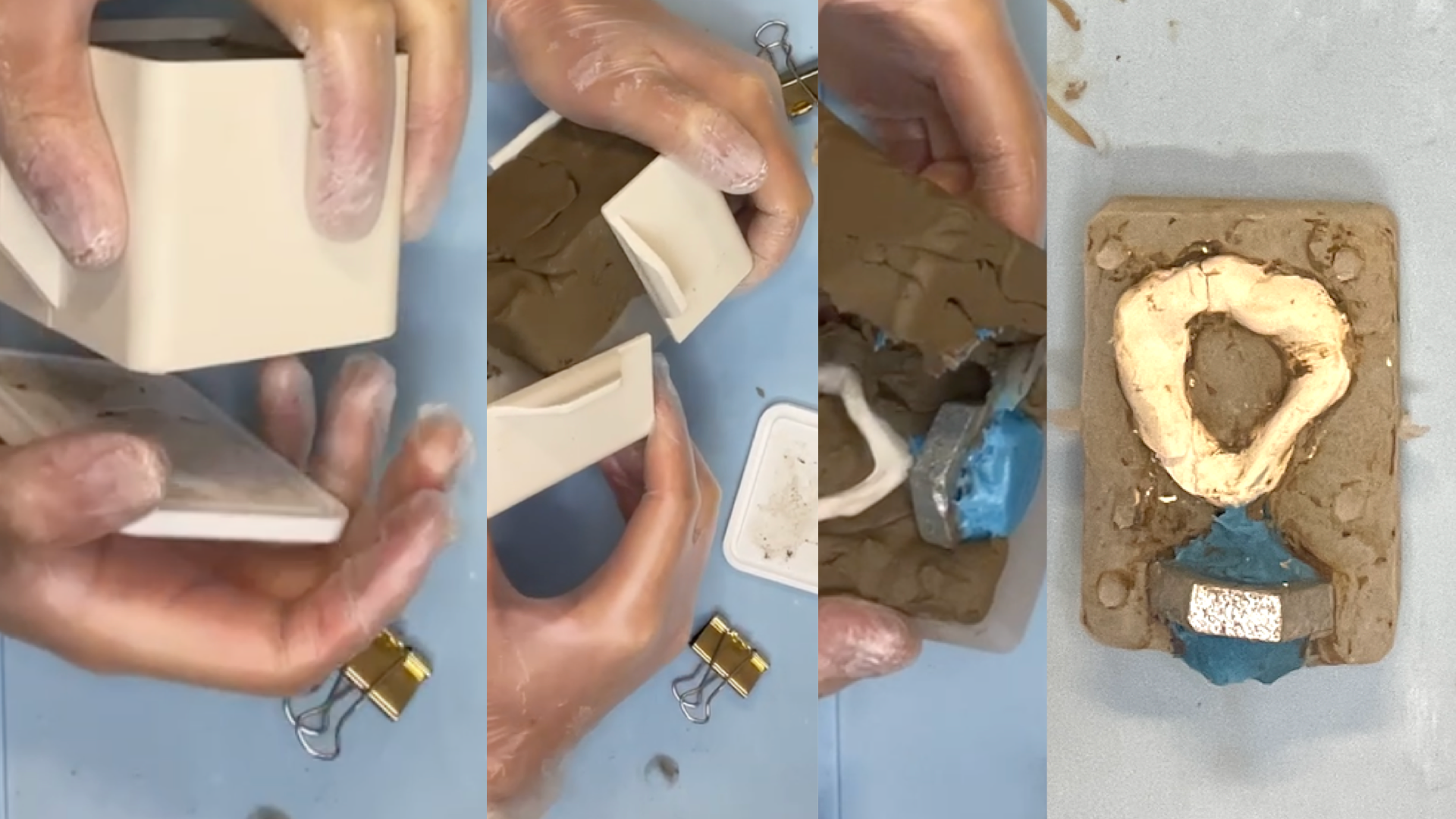
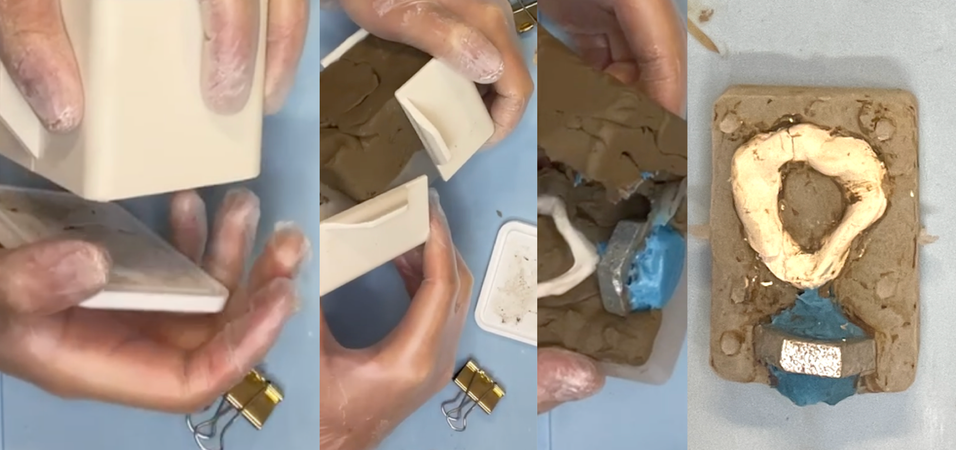
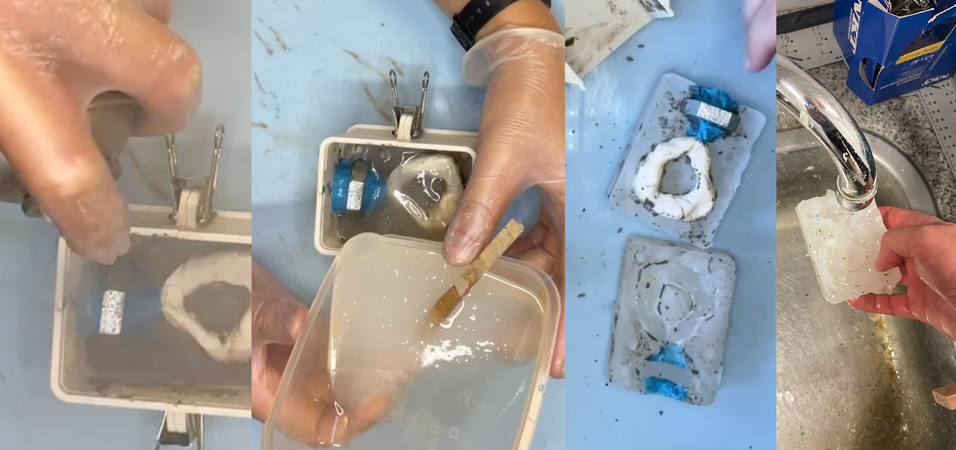
5
Inject
Now set up your Precious Plastic injection mould. I used PP and heated it up to 230 degrees.
Assemble your mould by inserting the lock nut and spraying some mould release into it. Once prepared, screw the mould onto your injection mould. No need for a jack or anything. Remember to wear proper safety clothing and shoes during this process, as working with heated plastic and high pressure can be hazardous. Excessive pressure during injection can cause dangerous failures, so handle the equipment carefully.
For my first attempt, I just taped the two parts together. This wasn’t strong enough, and the plastic floated out. For the second try, I clamped it between two boards, which worked better—only a thin layer floated out, making cleanup easy with an X-Acto knife.
In the future, creating a dedicated box for the mould to be inserted into might improve the process.
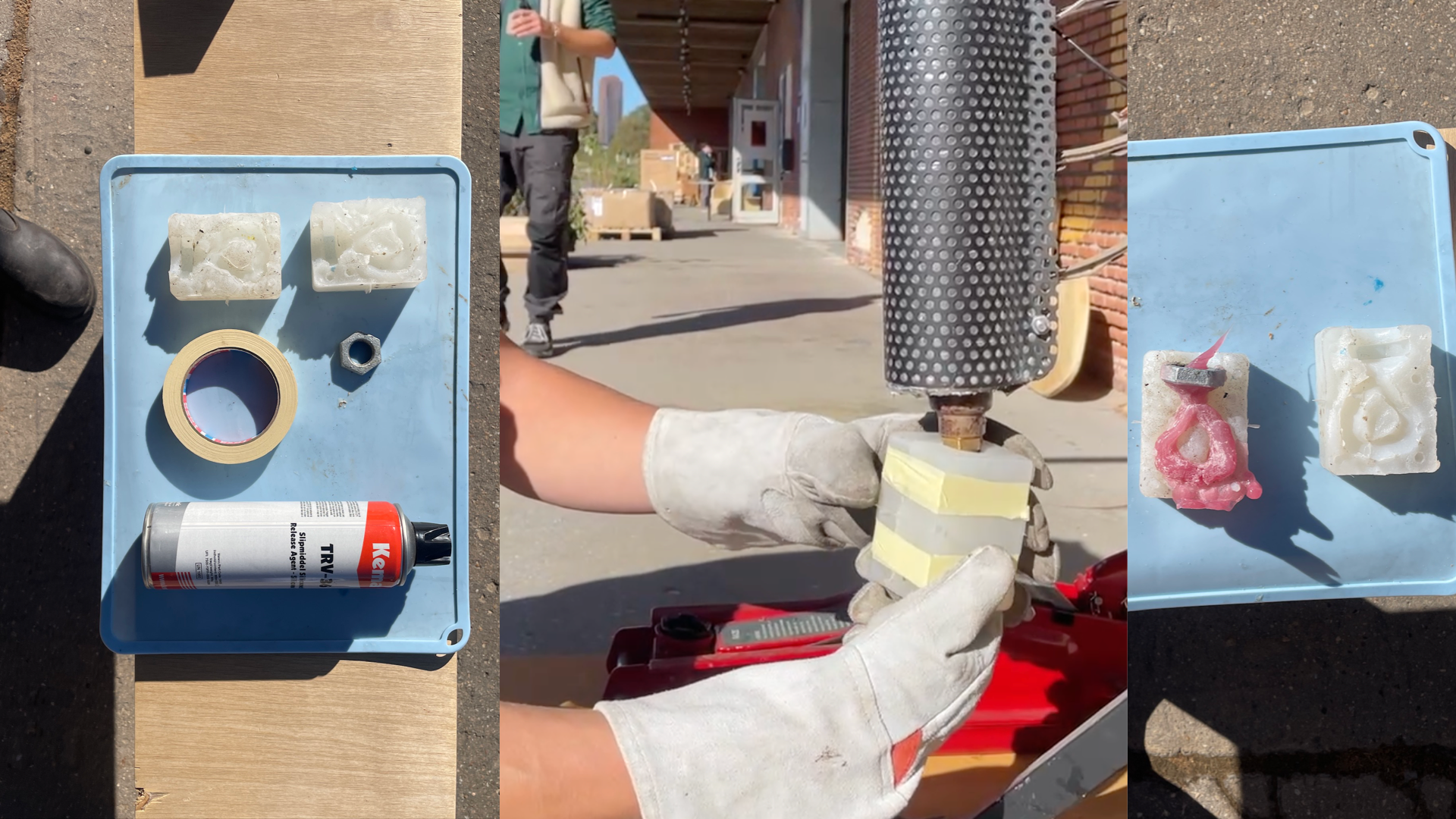
6
Finish
As mentioned in the introduction, this process is still far from perfect, but I believe there is significant potential, especially for products where high precision isn't critical. This method could be valuable for designers creating specific details for a limited number of parts, such as custom components, action figures, or prototypes for small-scale projects.
Unlocking the ability to create your own plastic products is increasingly important, especially since it's now easier and more affordable than ever to order parts made from virgin plastic. Additionally, with very low minimum order quantities (MOQs), Precious Plastic's injection molding process can effectively compete in this market.
Please feel free to reach out with any questions or suggestions.
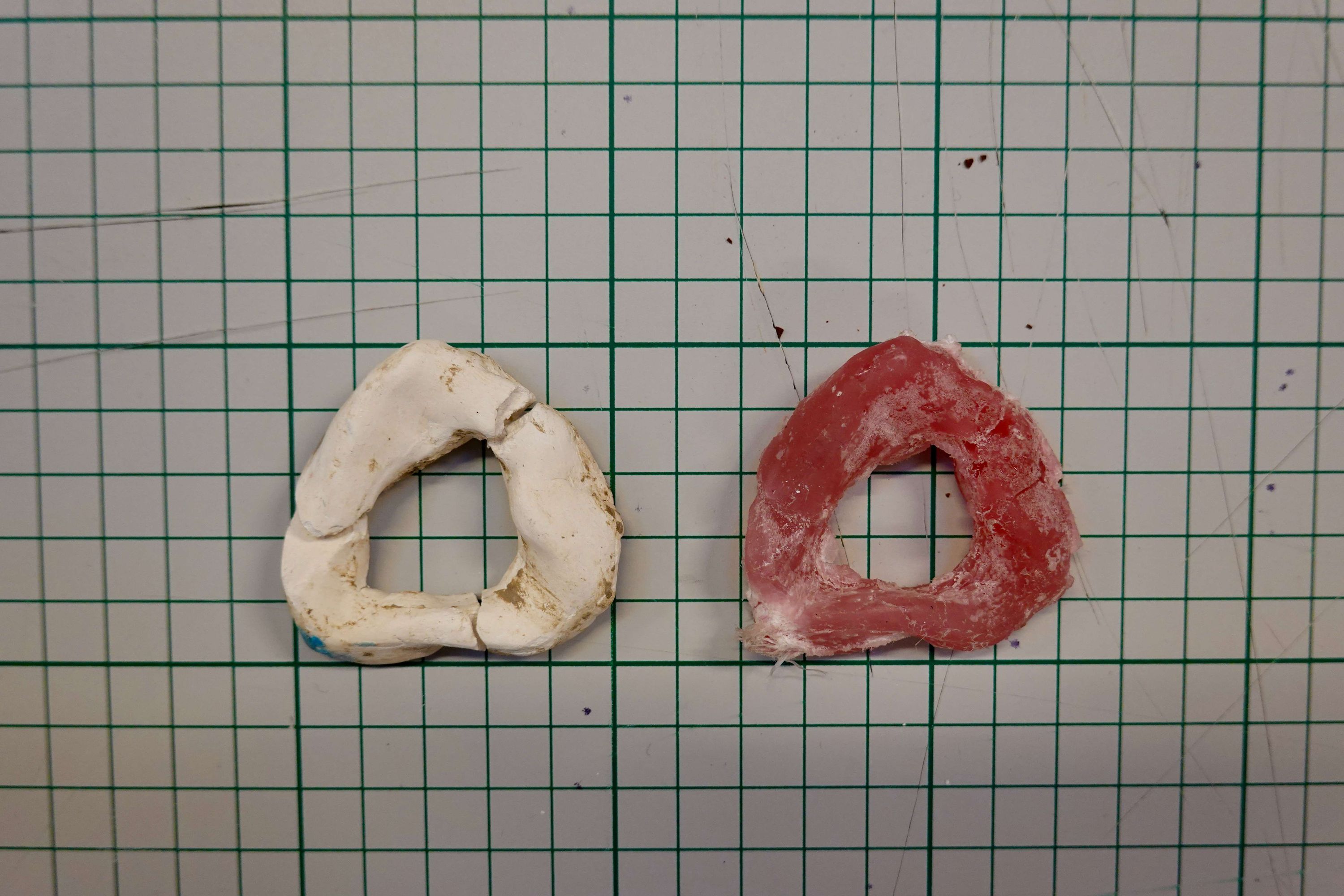
7
SAFETY FIRST!
SAFETY FIRST!
Heat-Resistant Silicone
Wear gloves when handling, as silicone can be difficult to remove from skin.
Injection Molder
Always wear safety glasses.
Use heat-resistant gloves to prevent burns.
Depending on the type of plastic, consider wearing a mask to avoid inhaling fumes.
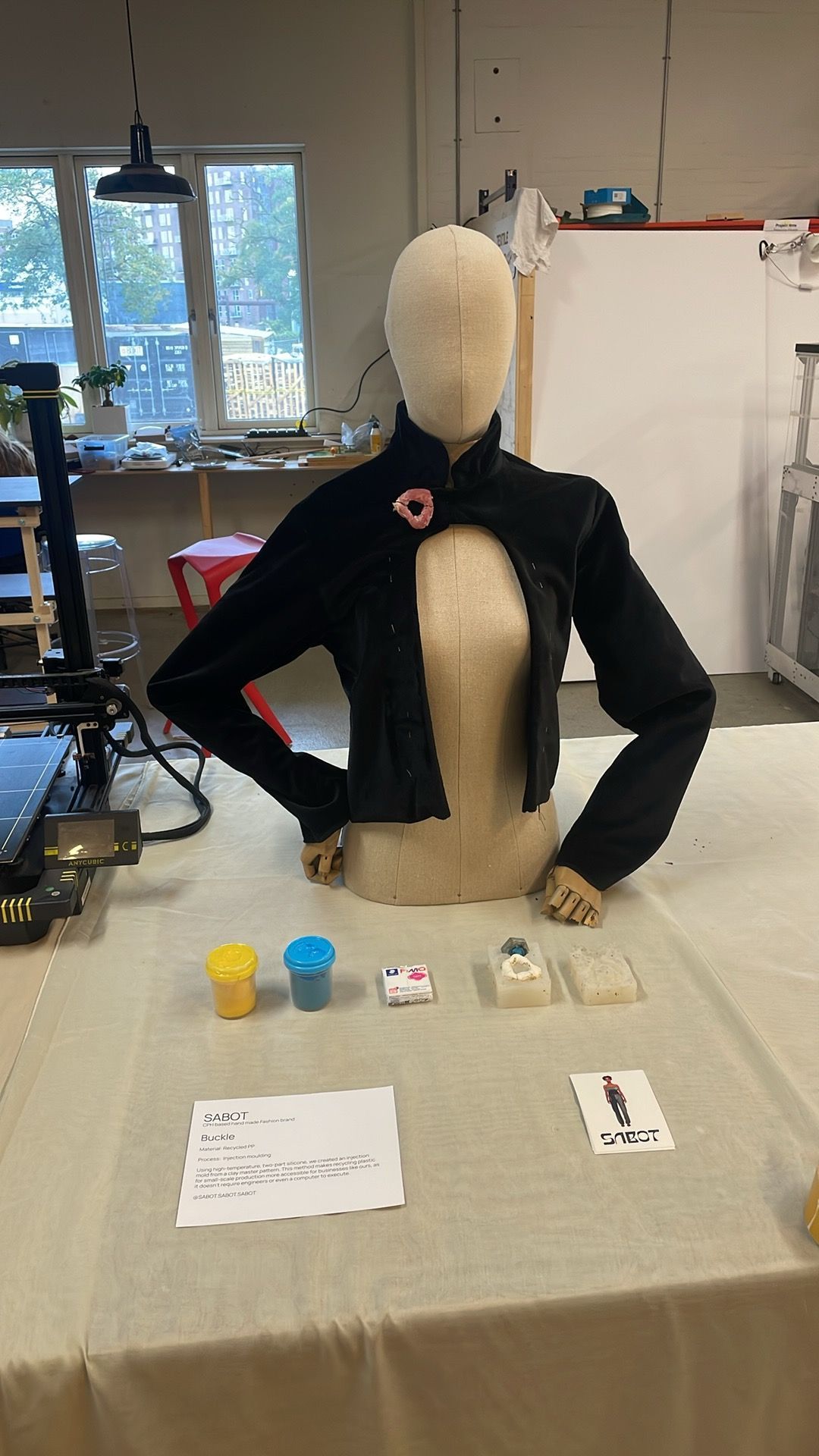