Products
Buckle mould
Precious Plastic and NoPlasticSunday have collaborated to create this buckle. The buckle mold is now openly shared as open-source, allowing everyone to freely use them. NoPlasticSunday conducted research on the structure of a buckle tightly interlocked and proceeded with 3D modeling to create a form suitable for injection molding.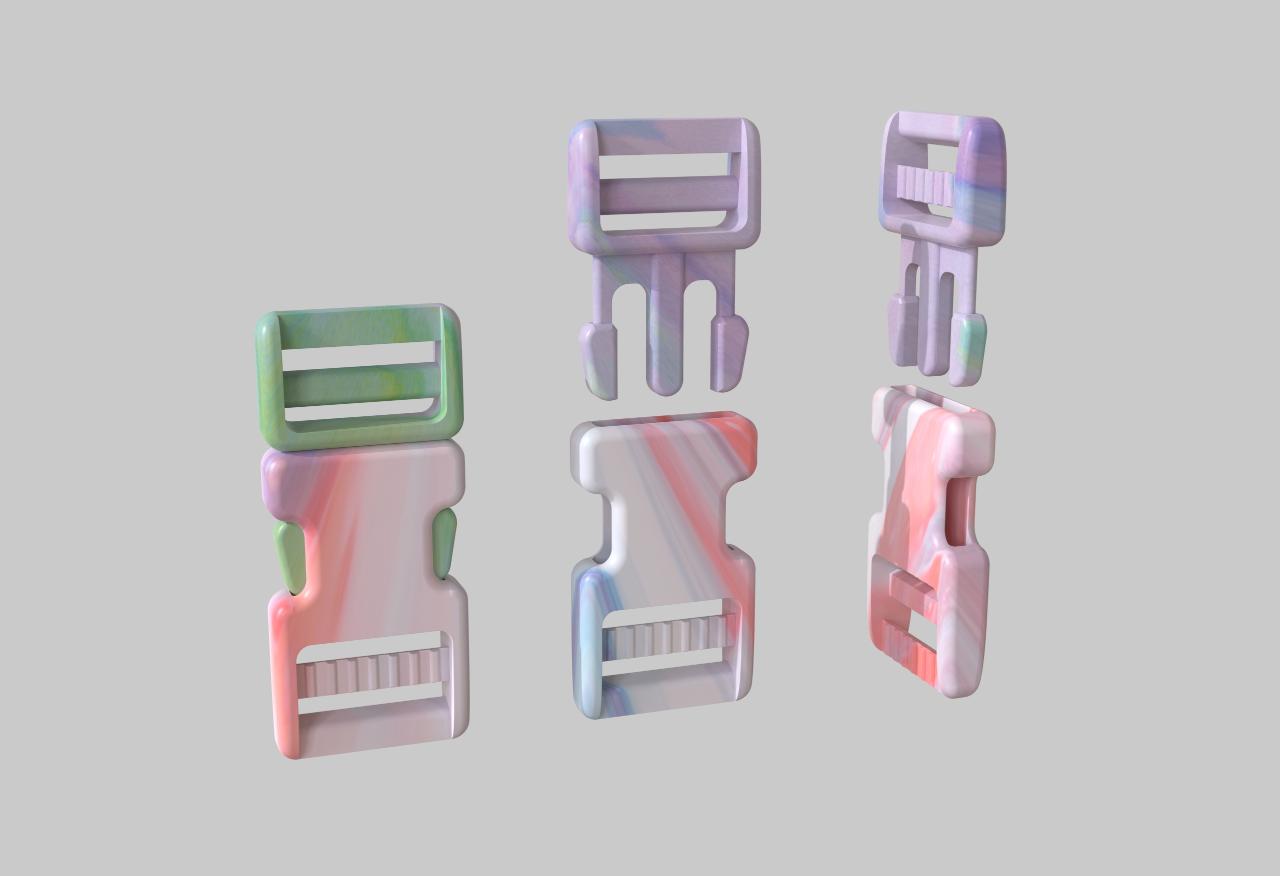
More Information
1
Product Modeling
Precious Plastic and NoPlasticSunday collaborated to create this buckle. The buckle and its mold will be openly shared as open-source, allowing everyone to freely use them. We conducted research on the structure of a buckle tightly interlocked and proceeded with 3D modeling to create a form suitable for injection molding.
For the buckle, a significant amount of time was spent in the design process to control the elasticity of the opening and closing parts using recycled plastic materials (PP or PE). Since the effectiveness of the design will be tested after the mold is made, we proceeded with the modeling keeping in mind the possibility of several mold modifications.
2
3D Printing Mock-up
We make a physical-sized prototype using 3D printing to verify the functionality of the product. After confirming the 3D printed prototype, we proceed with mold production.
However, for the buckle, due to its opening and closing function, achieving perfect functionality was challenging due to the limitations of the 3D printing material (PLA) and the manufacturing method.
3
Injection Mold Design
We design the mold for the product to be injected. We inspect the structure to ensure there are no issues with deforming the injected material. Typically, molds consist of two parts, but depending on the form, they might be made with three or more parts. We place and form the runners, which are the pathways through which plastic is injected into the mold, according to the product's specifications.
Also, we consider designing undercuts to ensure that the injected material can be easily released from the mold during injection.
4
Inject Mold Making
We use QDM molds made of aluminum material. Using CNC machines, we process aluminum to create the molds. After making the molds, we conduct injection tests and sometimes undergo modifications as needed.
During the injection testing process, several functional issues arose with the buckle. After several structural modifications, we were able to create a buckle without any functional problems.
5
Recycled Plastic Injecting
NoPlasticSunday sorts discarded plastic waste by color, crushes it, and turns it into material. We've created 20 sample colors for recycled plastic. We prepare for injection by blending materials based on desired color combinations.
Setting the machine at around 250 degrees, we press a button to inject the plastic into the mold. After the cylinder goes down, we wait for about 5 to 10 seconds before removing the mold to make sure the plastic fill the mold.
As we pening the mold, we can see buckles injected with a colorful marbled pattern of recycled plastic. After removing the plastic from the mold, we trim the runners.
After this lengthy process, the buckle product is finally complete!