Machines
Automatic Injection Molding Machine
An automatic injection machine using a linear actuator for Precious Plastic is an advanced recycling device that automates the injection molding process. The linear actuator precisely controls the movement of the injection mechanism, ensuring consistent and accurate plastic flow into molds. This machine efficiently melts shredded plastic waste and injects it into various molds to create new products. The integration of a linear actuator enhances the precision, reliability, and repeatability of the molding process, making it a valuable tool for sustainable and scalable plastic recycling efforts. This machine was co-designed and co-manufactured by Precious Plastic San3a Tech team.injection
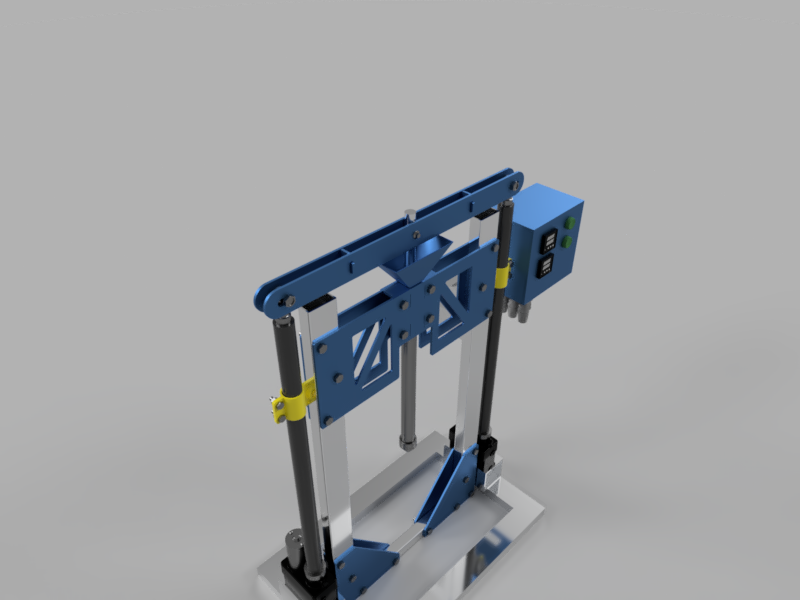
More Information
1
Getting Ready
Click the yellow download button (above) to get the following files:
- 3D .step files
- Laser cut files .dxf
- Bill of materials.
- Blueprints
To build this machine you'll need to have access to:
- Metal laser cut
- Metal cutting tools: Angle grinder, hacksaw, or metal shears for cutting and shaping metal parts of the frame.
- Welding machine
- Drill press: For drilling holes in the frame and other components.
- Basic tools: spanners, Pliers ,screwdrivers and wrenches, etc.
- Measuring tools: Tape measure, calipers, ruler for accurate measurements during construction.
- Safety glasses and gloves: Essential for protecting yourself during metalworking
2
Construct the Frame
The frame design was inspired by the Injection Machine - Designed for disassembly. Build a sturdy frame from metal to house all the components. The frame should be able to handle the pressure exerted by the actuator. To get accurate measurements, use laser-cut parts made of MDF wood as guides for drilling holes in the frame. Once you finish drilling and welding, assemble the metal laser-cut parts.
You can know more about the Injection Machine - Designed for disassembly:
https://community.preciousplastic.com/how-to/injection-machine---designed-for-disassembly?utm_source=user-profile
-1906a9176b2.jpg?width=956&resize=contain)
-1906aa0e1a1.jpeg?width=956&resize=contain)
3
Mount the Linear Actuator
Secure the linear actuator to the frame, ensuring its pushrod aligns with the injection barrel. The linear actuator comes with a metal clamp; weld the clamp to the metal frame for a secure attachment. Make sure that the two motors are aligned with each other.
*Note: To reduce vibration and motor slipping, insert rubber pieces between the motor and the metal clamp that comes with the linear actuator.*
Linear Motor Specification:
- Input 36VDC
- Load Capacity 3500N
- Strock Length 600mm
- Full Load Speed 5 mm / sec
- Limit Switch Adjustable
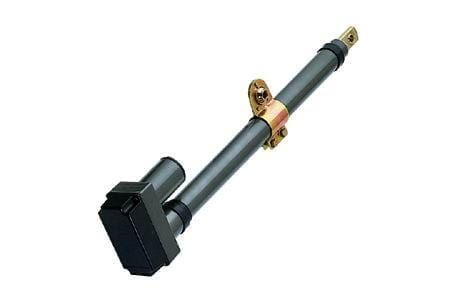
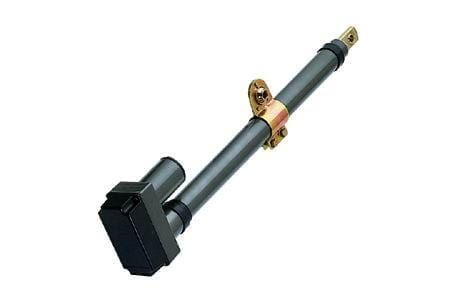
-1906a9ecc34.jpg?width=956&resize=contain)
4
Integrating the Electronics Systems
I used the same design of precious plastic's injection machine.
Set Up the Heating Element and Temperature Control
- Attach the heating element around the barrel where the plastic will melt.
- Install temperature controllers to regulate the heating element.
- Connect the Wiring and Electronics
- Wire the heating element, temperature controller, and linear actuator.
- Ensure all electrical connections are secure and insulated.
5
Testing and Refinement:
Initial Testing:
- Begin with manual control to test the movement of the actuator and injection process.
- Adjust the settings for temperature based on your material and mold design.
- Perform safety checks to ensure all components are secure and functioning properly.
- Make any necessary adjustments to improve efficiency and reliability.
-1907058cfbf.jpeg?width=956&resize=contain)
6
Begin Production
How to use the machine
1. Turn on the machine and fill the barrel with plastic.
2. For the first injection, wait 25 minutes since the machine was turned on and filled.
3. Place the mold against the nozzle.
4. Turn on the motor to move down the piston, pushing the molten plastic inside the mold.
5. Remove the mold without moving the motors to maintain the pressure.
6. Open the mold and take out the injected part
7. For continuous injections turn the motor backwards to move the piston up, then refill the barrel.